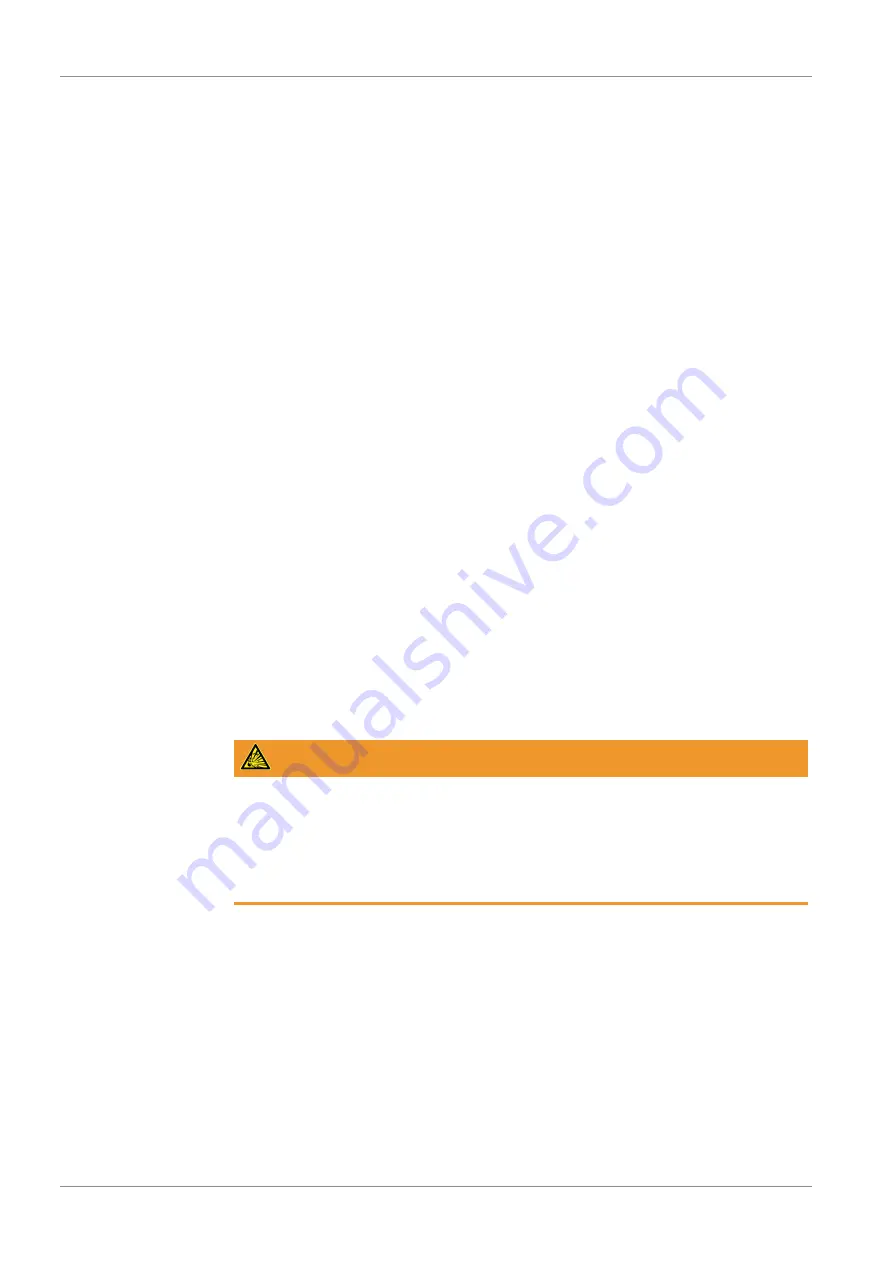
5 | Installation
12 / 40
0870572240_RA0400-0630C_Ex_-0011_IM_en
• Make sure that the installation space or location is vented such that sufficient cooling
of the machine is provided.
• Make sure that cooling air inlets and outlets are not covered or obstructed and that
the cooling air flow is not affected adversely in any other way.
• Make sure that the oil sight glass (OSG) remains easily visible.
• Make sure that enough space remains for maintenance work.
• Make sure that the machine is placed or mounted horizontally, a maximum of 1° in
any direction is acceptable.
• Check the oil level, see
• Make sure that all provided covers, guards, hoods, etc. are mounted.
Version with water-oil heat exchanger:
• Make sure that the cooling water complies with the requirements, see
If the machine is installed at an altitude greater than 1000 meters above sea level:
• Contact your Busch representative, the motor should be derated or the ambient
temperature limited.
Make sure that the monitoring devices are correctly connected and integrated into a
control system such that operation of the machine will be inhibited if the safety limit val-
ues are exceeded, see
Electrical Connection of the Monitoring Devices [
.
If additional electrical components not included in scope of delivery should be added:
• Make sure that they have a better or equal ATEX classification than that of the
machine, see the ATEX marking on the nameplate (NP).
For classification type “C” and “D” (see
ATEX Classifications and Associated Accessor-
• Make sure that the installation space or location is ventilated enough in order to
prevent the formation of an explosive area.
5.2 Connecting Lines / Pipes
WARNING
The connection lines can build up an electrostatic charge.
Risk of severe injury!
Risk of explosion!
• The connection lines must be made out of conductive material or provisions must be
made against creating an electrostatic charge.
• Remove all protective covers before installation.
• Make sure that the connection lines cause no stress on the machine‘s connection; if
necessary use flexible joints.
• Make sure that the line size of the connection lines over the entire length is at least as
large as the connections of the machine.
In case of long connection lines it is advisable to use larger line sizes in order to avoid a
loss of efficiency. Seek advice from your Busch representative.