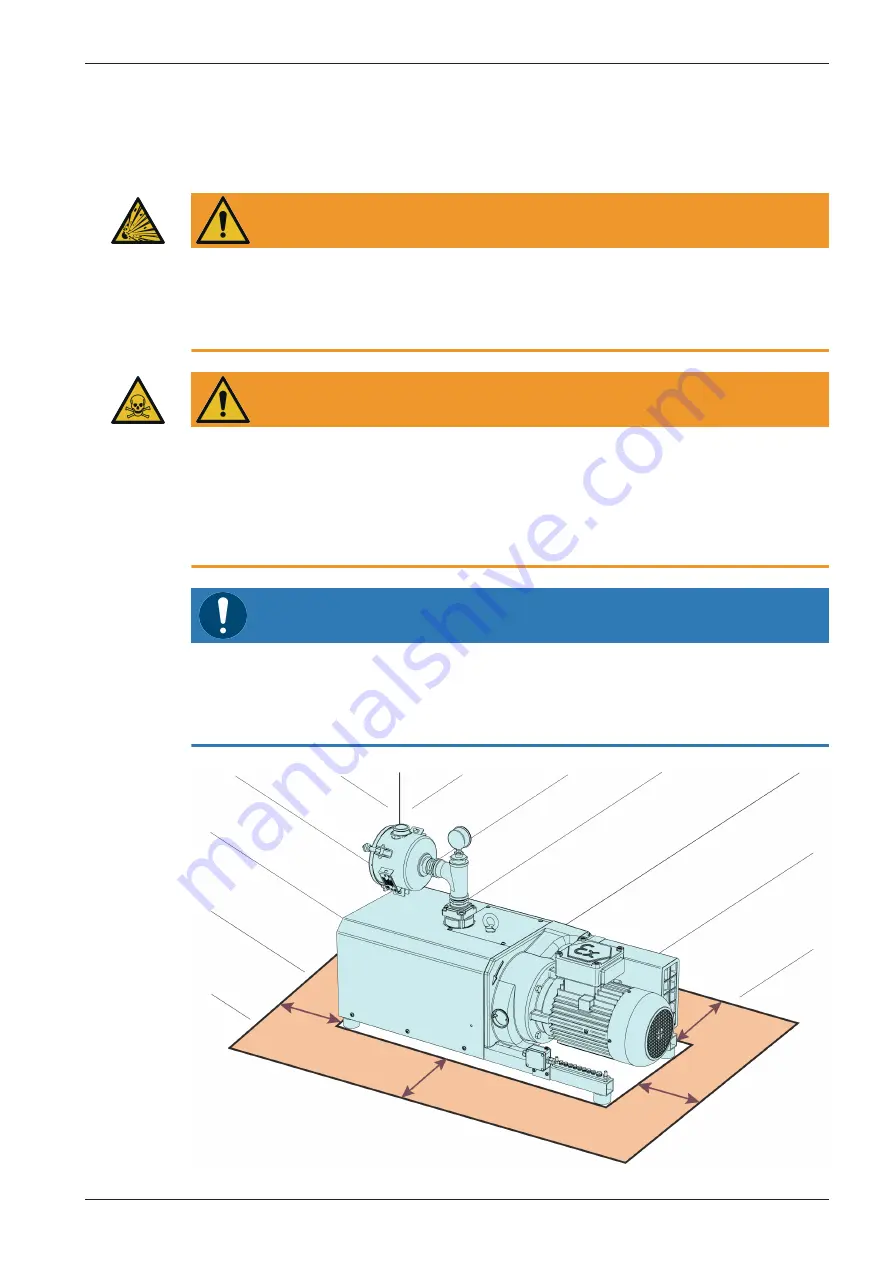
Installation | 5
Instruction Manual MINK MM 1104-1142 BV ATEX_EN_en
13 | 40
5
Installation
5.1
Installation Conditions
WARNING
The installation conditions are not respected in an ATEX environment.
Risk of severe injury!
Risk of explosion!
●
Take care that the installation conditions are met.
WARNING
Gas tight version:
The machine is not absolutely gas tight, possible leakages of dangerous media.
Risk of poisoning!
Risk of infection!
●
Make sure that the ambient atmosphere of the machine is sufficiently ventilated.
Closed air cooling systems are not suitable and therefore prohibited.
NOTICE
Use of the machine outside of the permitted installation conditions.
Risk of premature failure!
Loss of efficiency!
●
Take care that the installation conditions are fully complied with.
~ 1 m
~ 1 m
~ 1 m
~ 1 m