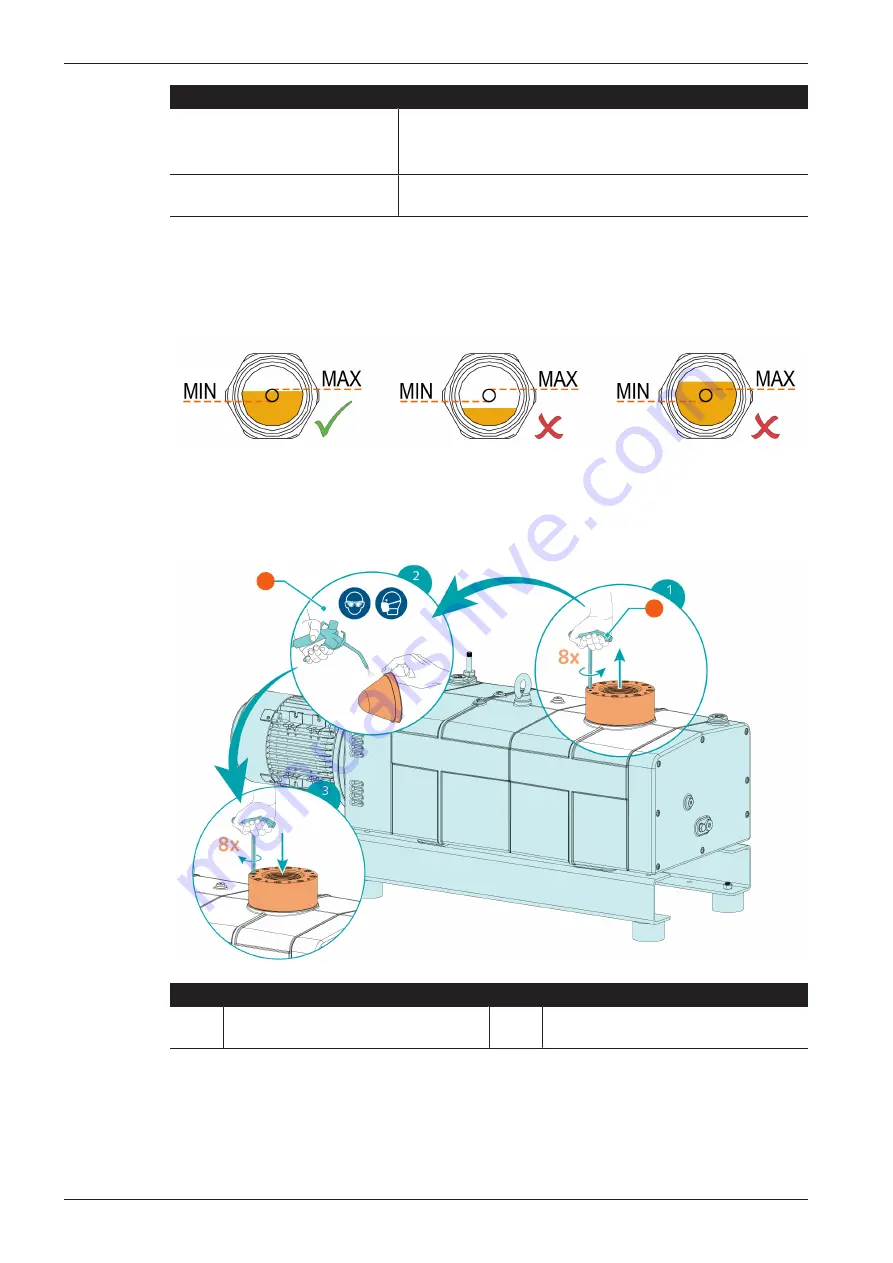
8 | Maintenance
26 | 40
Instruction Manual COBRA NX 0450-0650 A WCV_EN_en
Interval
Maintenance work
Every 8500 hours or after 1 year
●
Change the oil of the gear and bearing housings (both
sides), see
●
Clean the magnetic plugs (MP).
Every 25000 hours or after 4
years
●
Have a major overhaul on the machine (contact Busch).
8.2
Oil Level Inspection
●
Shut down the machine.
●
When the machine is stopped, wait 1 minute before checking the oil level.
●
8.3
Cleaning the Inlet Screen
1
2
Description
1
Use a hexagonal key
2
Use compressed air and wear protec-
tive eyewear and mask