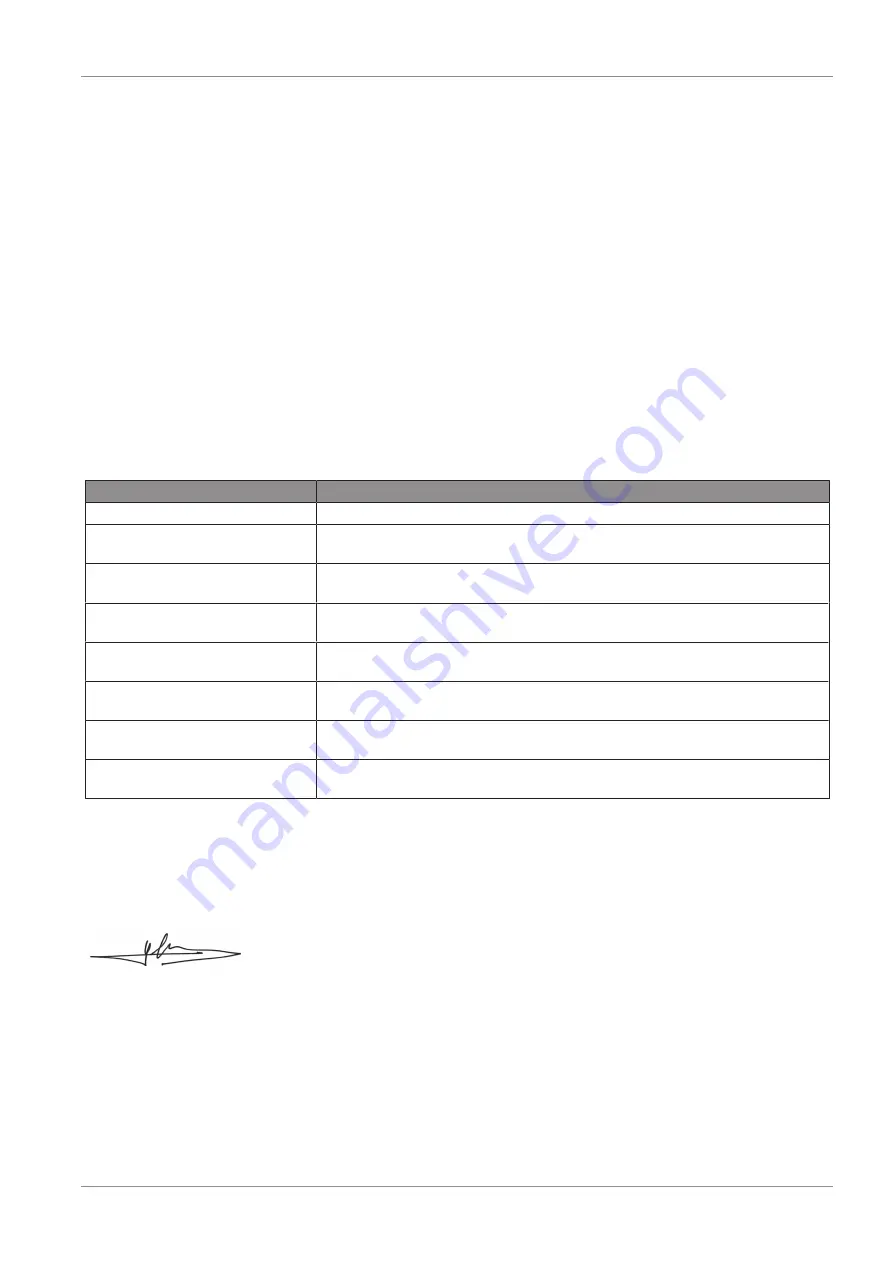
EU Declaration of Conformity | 15
Instruction Manual COBRA NC 2500 B WCV_EN_en
39 / 44
15 EU Declaration of Conformity
This Declaration of Conformity and the CE-mark affixed to the nameplate are valid for the machine within the
Busch scope of delivery. This Declaration of Conformity is issued under the sole responsibility of the manufac-
turer.
When this machine is integrated into a superordinate machinery the manufacturer of the superordinate machin-
ery (this can be the operating company, too) must conduct the conformity assessment process for the superor-
dinate machine or plant, issue the Declaration of Conformity for it and affix the CE-mark.
The manufacturer
Ateliers Busch S.A.
Zone Industrielle
CH-2906 Chevenez
declares that the machine(s):
COBRA NC 2500 B
fulfill(s) all the relevant provisions from European directives:
– ‘Machinery’ 2006/42/EC
– ‘Electromagnetic Compatibility’ 2014/30/EU
– ‘RoHS’ 2011/65/EU Restriction of the use of certain hazardous substances in electrical and electronic
equipment (incl. all related applicable amendments)
and comply(-ies) with the following designated standards that have been used to fulfil those provisions:
Standard
Title of the Standard
EN ISO 12100 : 2010
Safety of machinery - Basic concepts, general principles of design
EN ISO 13857 : 2019
Safety of machinery - Safety distances to prevent hazard zones being
reached by the upper and lower limbs
EN 1012-1 : 2010
EN 1012-2 : 1996 + A1 : 2009
Compressors and vacuum pumps - Safety requirements - Part 1 and Part 2
EN ISO 2151 : 2008
Acoustics - Noise test code for compressors and vacuum pumps - Engineer-
ing method (grade 2)
EN 60204-1 : 2018
Safety of machinery - Electrical equipment of machines - Part 1: General re-
quirements
EN IEC 61000-6-2 : 2019
Electromagnetic compatibility (EMC) - Generic standards. Immunity for in-
dustrial environments
EN IEC 61000-6-4 : 2019
Electromagnetic compatibility (EMC) - Generic standards. Emission stand-
ard for industrial environments
EN ISO 13849-1 : 2015
(1)
Safety of machinery - Safety-related parts of control systems - Part 1: Gen-
eral principles for design
(1)
In case control systems are integrated.
Legal person authorized to compile the technical file
and authorized representative in the EU
(if the manufacturer is not located in the EU):
Busch Dienste GmbH
Schauinslandstr. 1
DE-79689 Maulburg
Chevenez, 14.05.2021
Christian Hoffmann, General Director