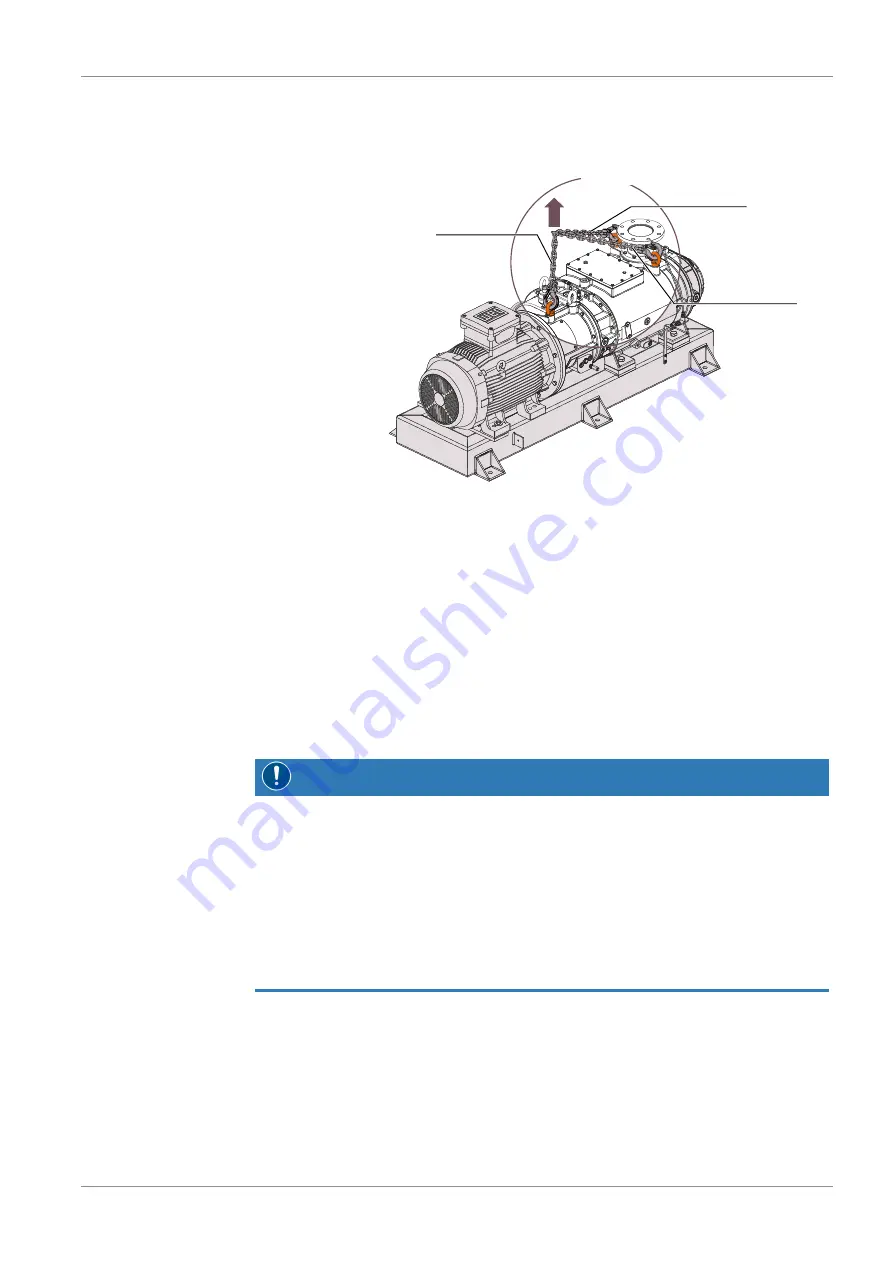
Storage | 4
0870549537_NC2000B_VR_A0004_IM_en
7 / 28
• Make sure that the eyebolt(s) (EB) is/are in faultless condition, fully screwed in and
tightened by hand.
Machine weight:
see the technical data or the nameplate (NP)
l3 = ~1030 mm
l1 = ~770 mm
l2 = ~1020 mm
• Check the machine for transport damage.
If the machine is secured to a base plate:
• Remove the machine from the base plate.
4
Storage
• Seal all apertures with adhesive tape or reuse provided caps.
If the machine is to be stored for more than 3 months:
• Wrap the machine in a corrosion inhibiting film.
• Store the machine indoors, dry, dust free and if possible in original packaging
preferably at temperatures between -20 ... 60 °C.
NOTICE
Long storage time.
Risk of damage to the machine!
• If the machine is equipped with oil lubricated mechanical seals, we recommend to
completely fill the oil chamber before a long storage, see “Oil filling” in chapter
. This protects the mechanical seals during a long storage. Use the
standard pump oil, see chapter
• Before restarting the machine, drain the oil to the normal oil level, see “Oil draining”
.