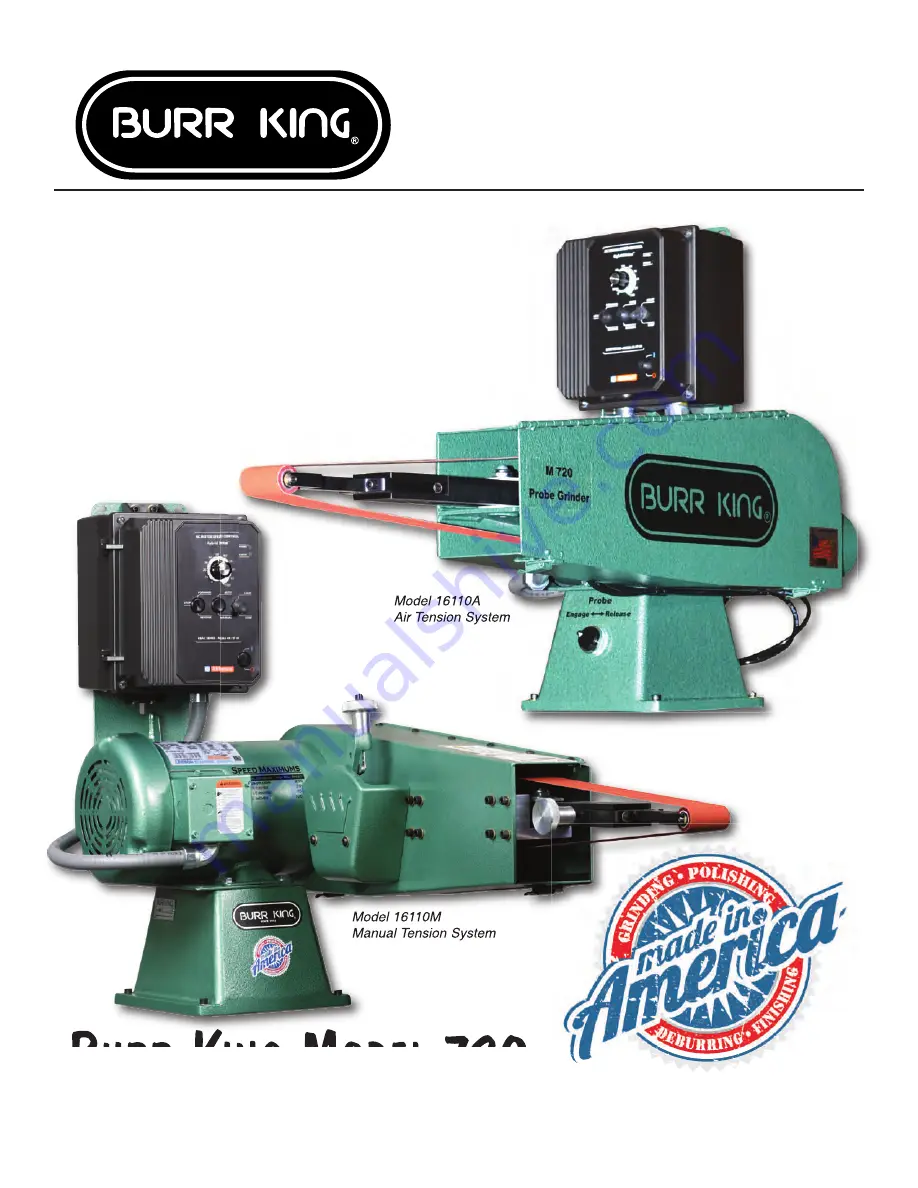
BURR KING MFG. CO., INC
1220 Tamara Lane
Warsaw, MO 65355
www.burrking.com
(660)438-8998 • 800-621-2748
Fax (660)438-8991
B
URR
K
ING
M
ODEL
720
T
WO
W
HEEL
P
ROBE
G
RINDER
M
ODEL
720
I
NSTRUCTION
M
ANUAL
M
ANUAL OR
A
IR
T
ENSION
Model 16110A
Air Tension System
Model 16110M
Manual Tension System
2021
Design