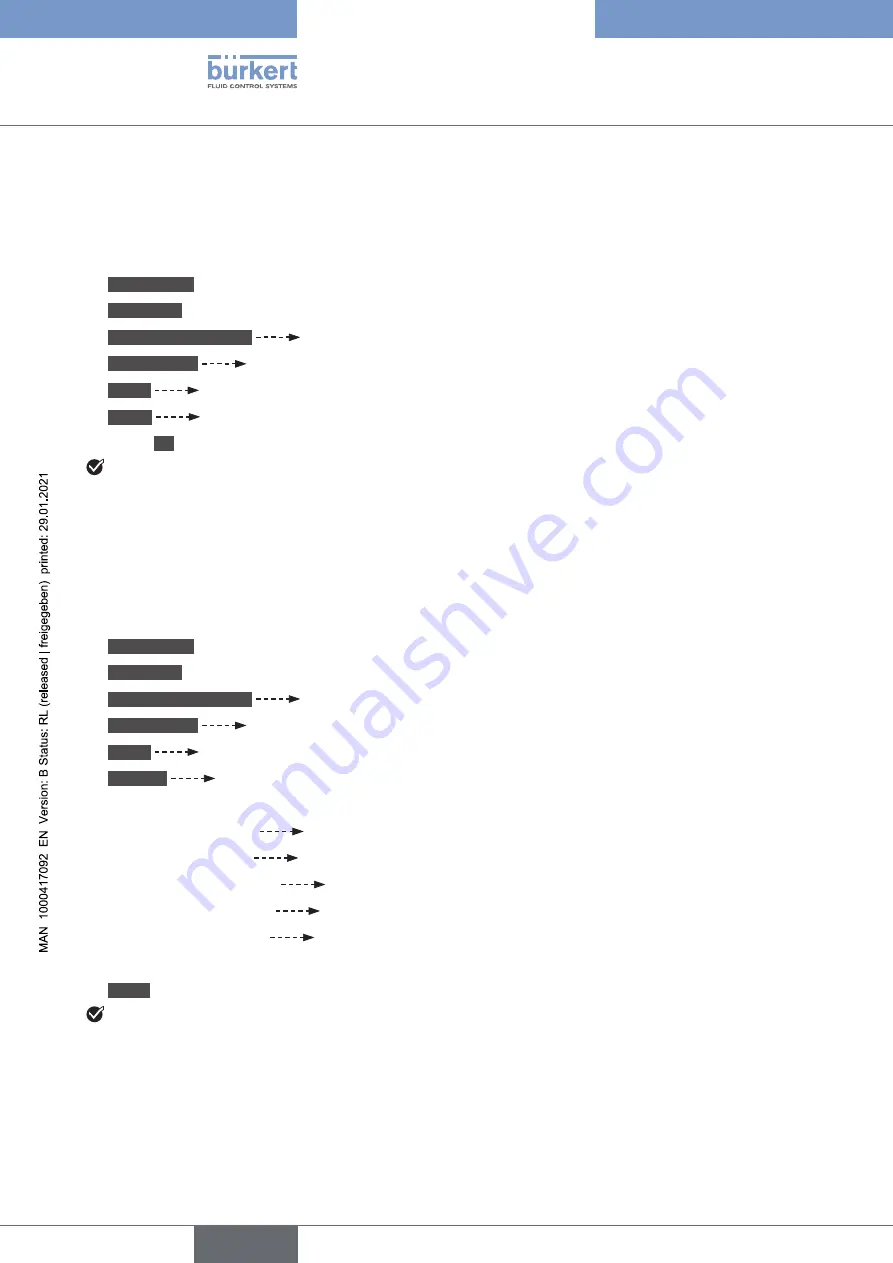
86
SAW sensor - Parameter
Type 8098
13.5.6
Deactivating the monitoring of the liquid temperature
By default, the liquid temperature values are not monitored. If the monitoring of the liquid temperature is
active, do the following to deactivate it:
→
Select the device in the navigation area.
→
SAW sensor
→
Parameter
→
Stand. meas. values
→
Temperature
→
Limits
→
Active
→
Select
No
The monitoring of the liquid temperature is inactive.
13.5.7
Changing the error limits, the warning limits and the hysteresis
of the liquid temperature
To change the error limits, the warning limits and the hysteresis of the liquid temperature, do the following:
→
Select the device in the navigation area.
→
SAW sensor
→
Parameter
→
Stand. meas. values
→
Temperature
→
Limits
→
Settings
The current settings are displayed.
→
Set the high error limit
→
Set the low error limit
→
Set the high warning limit
→
Set the low warning limit
→
Set the hysteresis value
The new settings are displayed.
→
Finish
The limit values and the hysteresis value are changed.
English