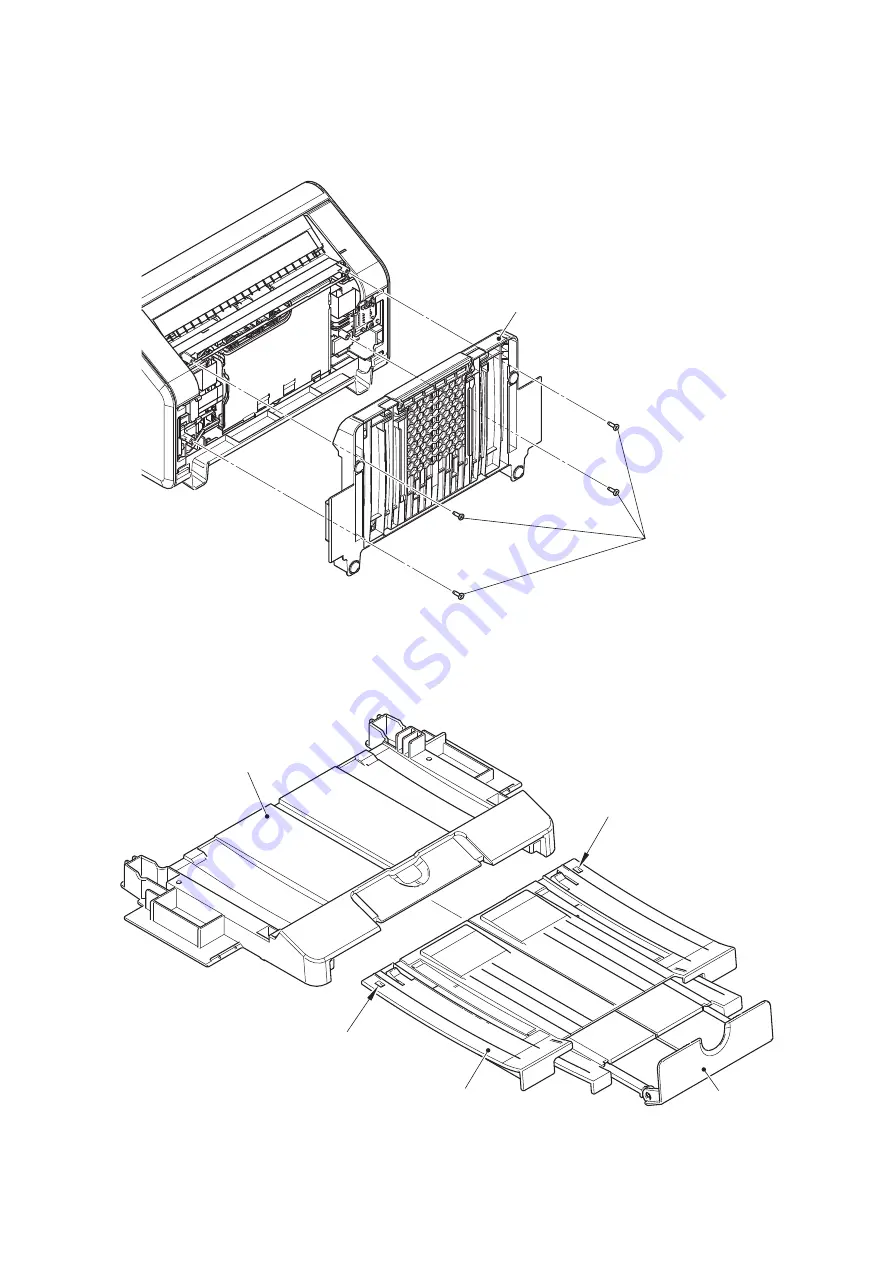
3-14
Confidential
9.2
Bottom cover ASSY / Exit stopper
(1) Remove the four taptite bind B M3x8 screws, and remove the bottom cover ASSY from the machine.
Fig. 3-4
(2) Remove the two stoppers, and remove the exit tray ASSY from the bottom cover ASSY.
(3) Remove the exit stopper from the exit tray ASSY.
Fig. 3-5
Bottom cover ASSY
Taptite bind B
M3x8
Stopper
Bottom cover ASSY
Stopper
Exit tray ASSY
Exit stopper
Summary of Contents for ImageCenter ADS-2800W
Page 24: ...2 4 Confidential 2 2 Paper Feeding Fig 2 2 Feed path Front side Back side ...
Page 50: ...3 2 Confidential 2 PACKING ...
Page 53: ...3 5 Confidential 5 LUBRICATION There are no applicable parts for lubrication ...
Page 54: ...3 6 Confidential 6 OVERVIEW OF GEARS There are no gears to be disassembled ...