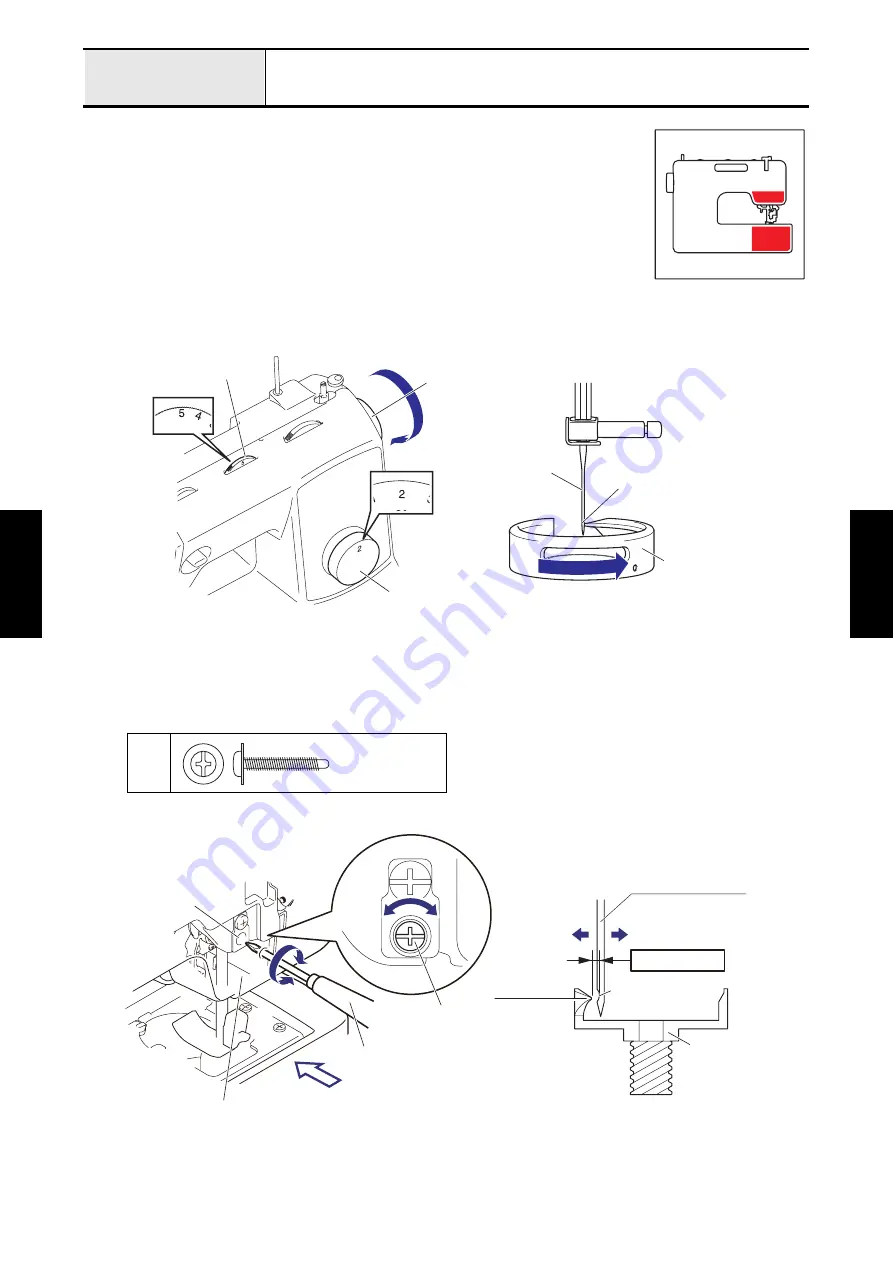
In
spection and Adjustment
In
spection and Adjustment
4 - 22
Adjustment
Needle clearance
[Standard]
At pattern selection dial [2] (straight stitch) and stitch width dial [5] (left base line), the
clearance between the scarf of the needle and the outer rotary hook point should be 0.15 to
0.3 mm when the rear side of the needle aligns with the outer rotary hook point.
[Adjustment]
1. Remove the needle plate assy, the presser foot and the inner rotary hook assy.
2. Attach the size 90/14 needle.
3. Turn the pattern selection dial until the [2] is the topmost position.
4. Turn the stitch width dial until the [5] is the topmost position.
5. Turn the pulley by hand until the outer rotary hook point aligns with the back side of the needle.
6. Insert a screwdriver into the hole of the rear cover, adjust the clearance between the scarf of the needle and the
outer rotary hook point by turning the screw
1
.
*Key point
• Loosen the screw
1
. (turn to the direction of “A”)
→
Move the needle to front side. (needle clearance is larger)
• Tighten the screw
1
. (turn to the direction of “B”)
→
Move the needle to rear side. (needle clearance is smaller)
1
Back side of needle
and tip coincide
Outer rotary
hook assy
Pattern
selection dial
Stitch width dial
Needle
Pulley
Cup screw
M
3X20
Size 90/14 Needle
Hook point
Back (B)
Front (A)
Outer rotary
hook assy
Scarf of needle
0.15 - 0.3 mm
Rear cover
Screwdriver
A
B
Back side view
1
1
Summary of Contents for AE2700
Page 1: ......
Page 2: ......
Page 3: ......
Page 30: ...2 14 Zigzag mechanism Basic Basic Zigzag mechanism location diagram BasicofDisassembly ...
Page 56: ...2 40 Zigzag mechanism Basic Basic Zigzag mechanism location diagram BasicofAssembly ...
Page 69: ...2 53 Main frame and Covers Basic Basic Main frame and Covers location diagram BasicofAssembly ...
Page 201: ...6 1 6 Motor 3P supply assy 6 2 LED lamp 6 4 Special Instructions of Wiring ...
Page 205: ......