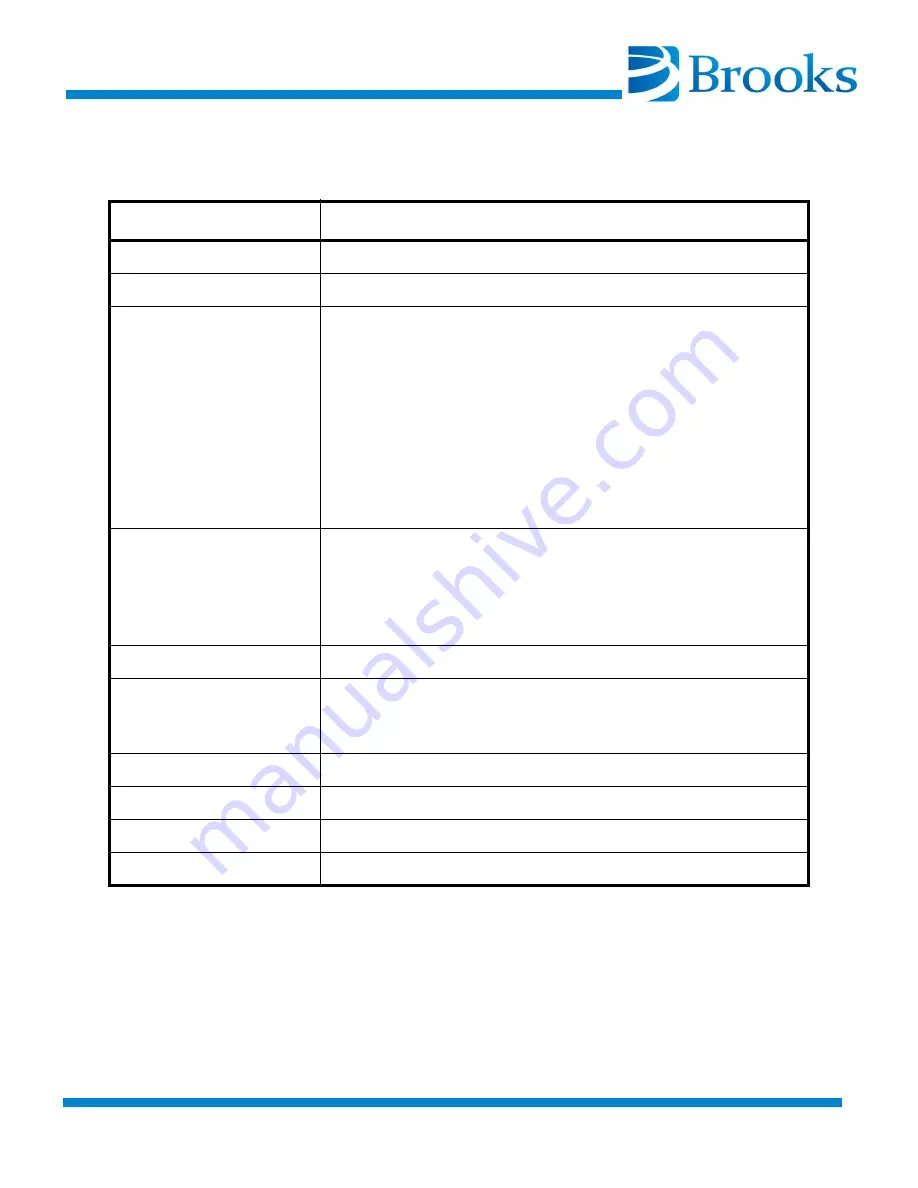
1-8
©2013 Brooks Automation Inc.
Pub. No. 8040564, Rev. AA, 01/15/13
ECO No. 64541
Specifications
Table 1-1: On-Board 8 GLE Cryopump Specifications
Parameter
Specifications
Input Power
208 VAC 50/60 Hz
Rough Pump Connection
NW 25 ISO KF
Integrated Hardware
Keypad/Display
Roughing Valve
Purge Valve
Cryopump TC Gauge
1st Stage Diode
2nd Stage Diode
1st Stage Heater
2nd Stage Heater
2 Setpoint Relays
RS-232 Interface
Pumping Speeds:
Water
Air
Hydrogen
Argon
4000 liters/sec
1500 liters/sec
2200 liters/sec
1200 liters/sec
Argon Throughput
700 sccm (9 torr-liters/sec)
Capacity:
Argon
Hydrogen
1000 std. liters
12 std. liters @ 5 x 10
-6
torr
Crossover
150 torr-liters
Cooldown Time
2 hours nominal
Dimensions
Refer to Installation/Interface Drawing
Weight
63 lbs.
Summary of Contents for On-Board 8
Page 1: ...On Board GLE Cryopump Installation and Maintenance Instructions 8040564 Revision AA...
Page 6: ...This Page Left Intentionally Blank...
Page 8: ...This Page Left Intentionally Blank...
Page 36: ...This Page Left Intentionally Blank...
Page 52: ...This Page Left Intentionally Blank...