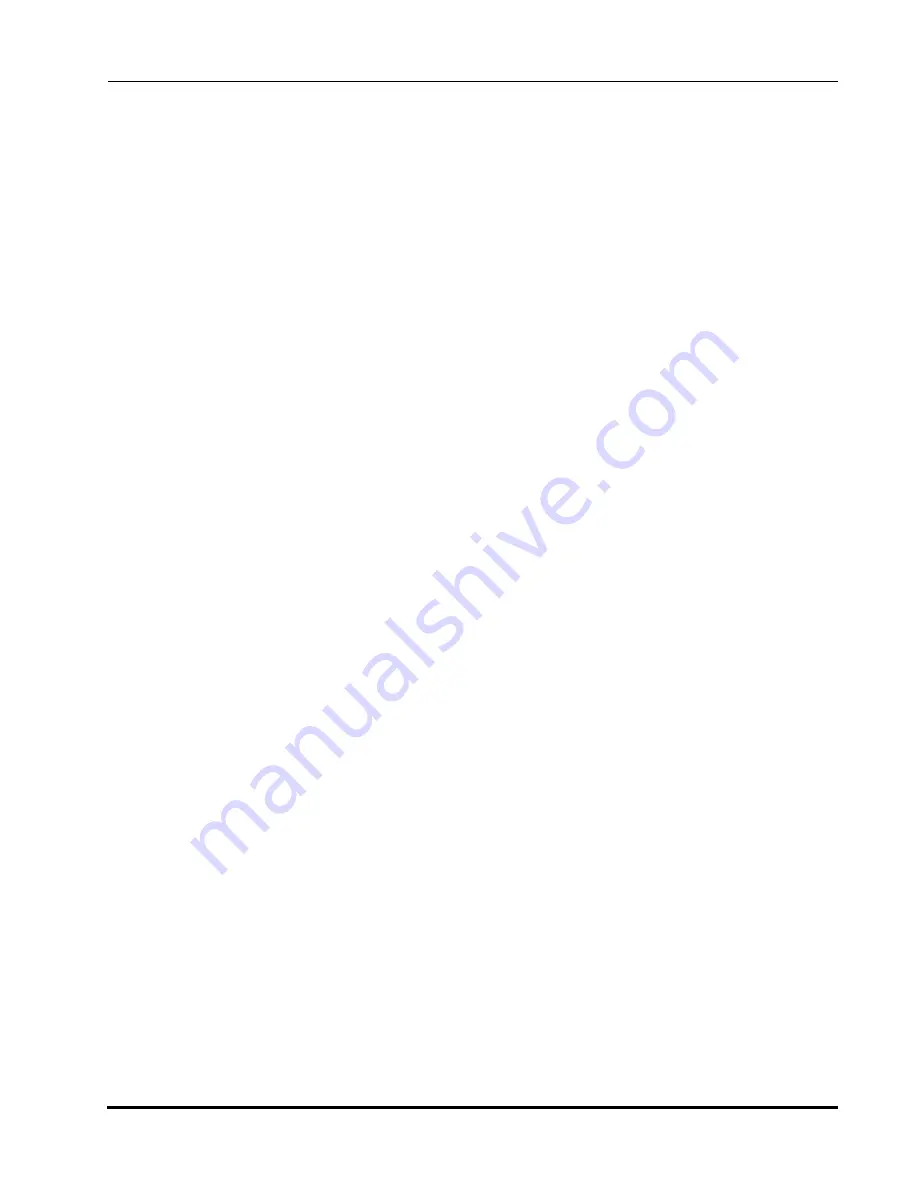
MagnaTran 7.1 User’s Manual
Operation
MN-003-1600-00
Discrete I/O Control (DIO)
Brooks Automation
Revision 2.2
6-45
Discrete I/O Control (DIO)
Discrete Control through the robot's 50-pin discrete I/O port provides all the control
functions necessary to operate the robot in a system. Although serial control provides
a more comprehensive command set, DIO control is also useful in changing configu-
ration or troubleshooting the robot.
DIO Control System
The robot has been designed for interface with a discrete I/O control unit for auto-
matic sequencing. Suitable devices include: computers with parallel I/O interface
ports, programmable logic controllers, and discrete logic devices.
DIO Control Programming
The DIO interface functions in a command/acknowledge format. Whenever possible
the output signals should be checked for the appropriate acknowledgment signal
before initiating the next command. For example, if a MOVE command has been
asserted (PI 0-21 Pin-25 LOW), check for the COMMAND STATUS\ response (PO 0-
21 Pin-24 LOW) before proceeding.
Initial DIO Configuration Procedure
Before operating the robot, the values for the station parameters must be set. The
robot offers independent, software-selectable parameters for all stations. These sta-
tion parameters may be set through either the serial port or the robot's Control/Dis-
play Module (CDM).
For serial control, see Chapter 5 for connections and Chapter 8 for commands.
For CDM control, see Chapter 4 for command flow and Chapter 6 for opera-
tion.
DIO Fault Conditions
A motion error on any of the three servos will trigger a latched, clearable fault condi-
tion.
Common causes of obstruction during extension include a closed valve,
improper station configuration, or improper sequencing. Take all possible precau-
tions to avoid obstruction of the arm during rotation, since damage to the arm or the
robot mechanism may result. Permanent damage to the robot is unlikely, but the
wafer should be checked for damage after any motion error has occurred.