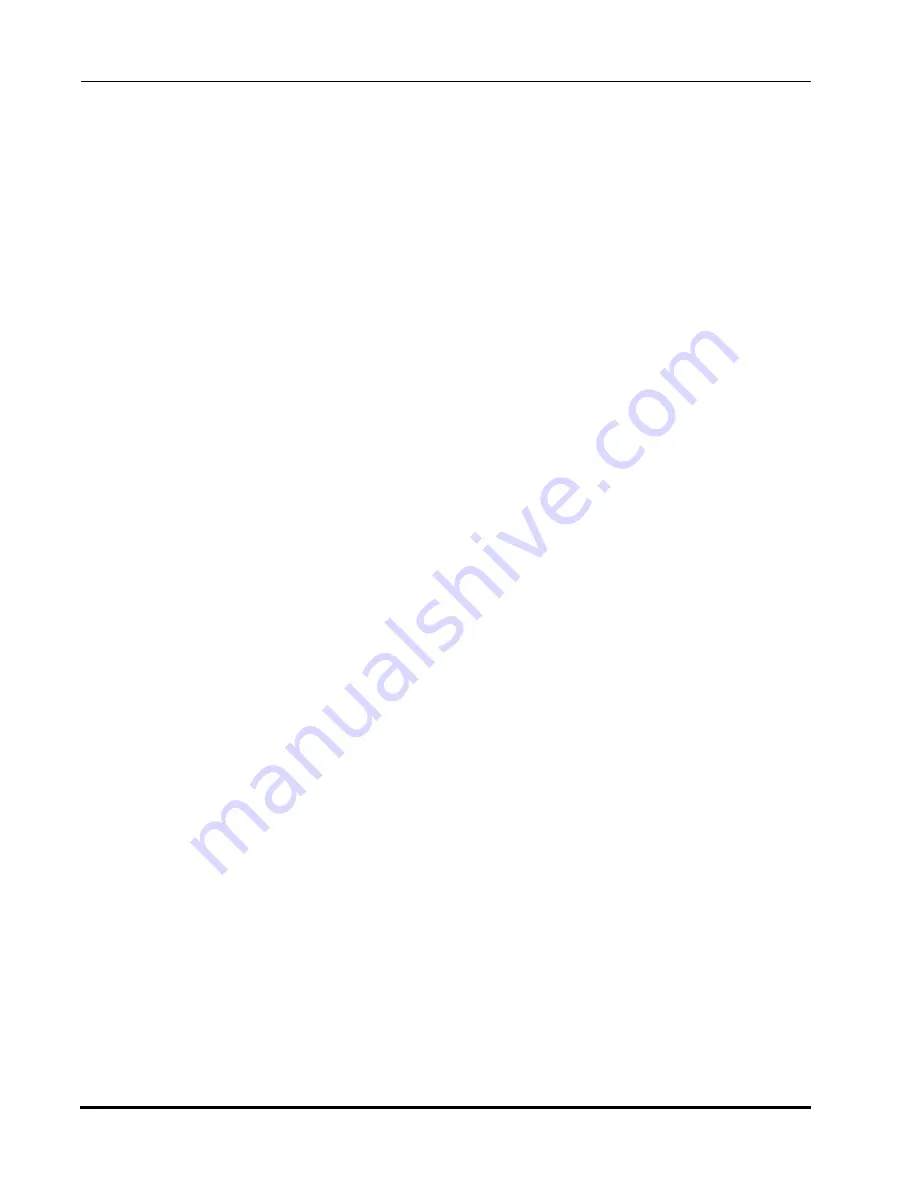
Operation
MagnaTran 7.1 User’s Manual
MagnaTran 7.1 Wafer Handling Robot Overview
MN-003-1600-00
Brooks Automation
6-6
Revision 2.2
Leapfrog™ Same-Side Dual Arm Set
On all three axis of motion [radial (R), rotational (T for Theta), and vertical (Z)],
the left and right sides of the arm set for both arm ‘A’ and arm ‘B’ are driven
simultaneously moving both end effectors as required. For vertical (Z) and
Rotational (T) motion, the arms move at the same time and with the same
velocities and accelerations.
For radial motion, the arms are driven simultaneously by the shoulder shafts,
one always extending while the other retracts slightly. Due to the kinematics
of the arm, the linear motion profile of the ‘A’ and ‘B’ arms will differ as the
arms move from Arm A fully extended to Arm B fully extended with the inac-
tive arm remaining in the retract position while the active arm extends or
retracts. End effectors are spaced approximately 10 to 16mm apart, depending
on application and calibrated at the factory.
The rotary motion of the independent drive shafts is coordinated by the Per-
sonality Board and profiled to provide smooth motion to the arms as the end
effector is accelerated from or brought to rest. The software produces a motion
profile at the T1 and T2 drive shafts that will obey the motion constraints for
arm A and B defined by the user.
While the maximum radial extension is dependent on the geometry of the arm
specified by the user, the MagnaTran 7 is typically supplied with a Leapfrog
arm that meets the specification of a 1050 mm reach from the center-line of the
robot to the center-line of the wafer. This version of the arm accommodates a
load of up to 1.0kg (2.2lbs) on each end effector. The actual extension and
retraction positions of the arms are software selectable.