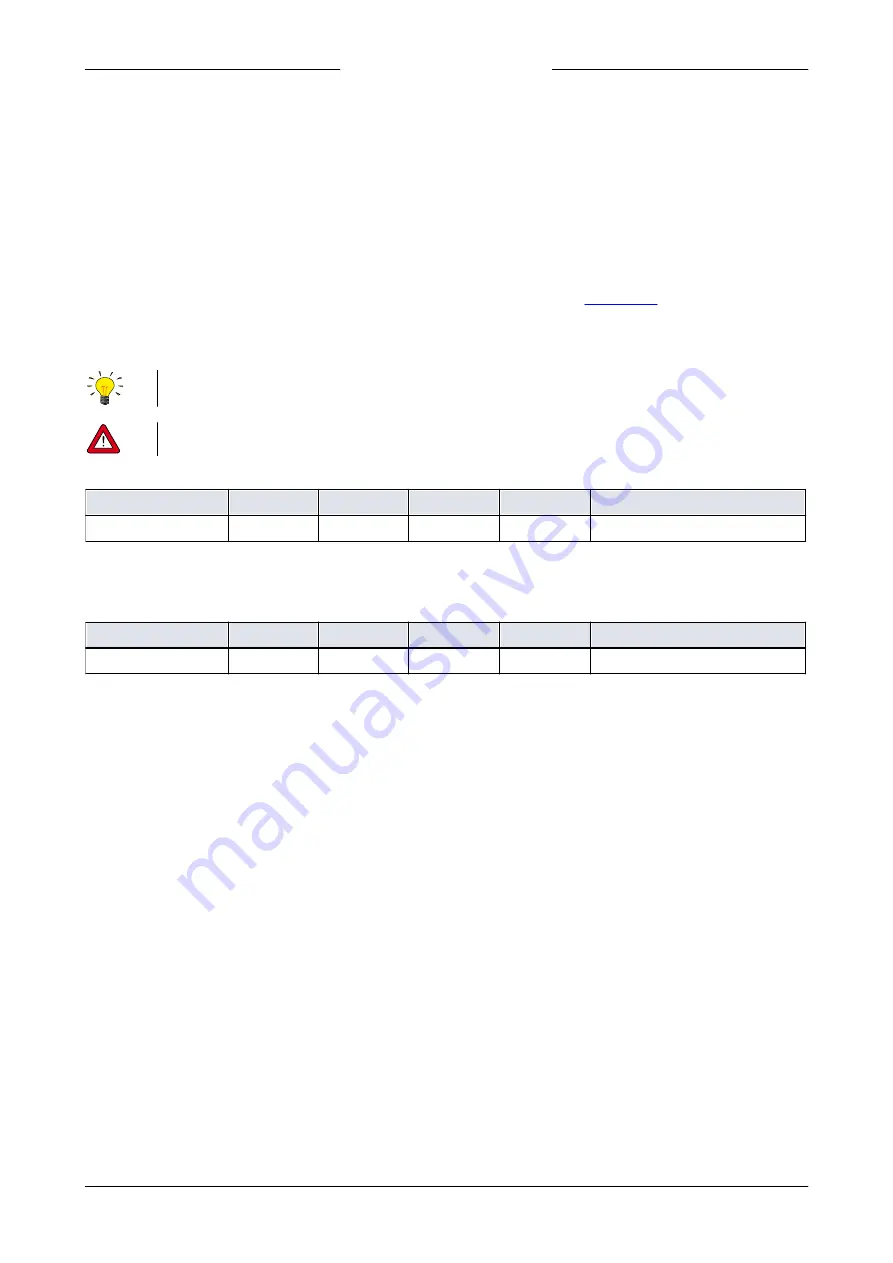
Bronkhorst®
Instruction Manual ES-FLOW™
9.17.116B
42
3.4.9
Master/slave configuration
Normally, there is no communication between slave instruments in a fieldbus system. The FLOW-BUS protocol, however,
provides a feature to set up a master/slave relationship between two instruments. The typical behavior of a slave
instrument is to automatically set its own setpoint relative to the output (measurement value) of its master.
The output value of any instrument connected to FLOW-BUS is automatically available to all other instruments (without
extra wiring). A FLOW-BUS system can have multiple masters and slaves. A slave instrument can also be a master to other
instruments.
To setup a master/slave relationship between instruments, first determine which instrument should be the master and
which should be the slave, then set
Control Mode
of the slave instrument to ‘FLOW-BUS Slave’ (value 2) or ‘FLOW-BUS Analog
Slave’ (value 13), depending on how the setpoint should be calculated (see parameter
).
The slave instrument periodically polls the output value of its master and multiplies it by the slave factor, thus setting its
own flow to a percentage of the master's.
Setpoints from master instruments can be received via FLOW-BUS only.
To avoid damage to the instruments an/or the systems they are connected to, be sure to avoid circular references between
devices on the same fieldbus. The FLOW-BUS system does not have a protection mechanism.
Master Node
Type
Access
Range
FlowDDE
FLOW-BUS
Modbus
Unsigned char
RW
1…128
158
33/14
n/a
Set the master node for the instrument
Note that this parameter only is effective in a FLOW-BUS system via RS485.
Slave Factor
Type
Access
Range
FlowDDE
FLOW-BUS
Modbus
Float
RW
0…500
139
33/1
0xA108…0xA109/41225…41226
The controller output from the master instrument is multiplied by
Slave Factor
/100% to get the slave instrument setpoint.
In systems other than FLOW-BUS via RS485,
Slave Factor
is effective only if
Control Mode
is set to 'Analog slave', and the
analog output signal of the master instrument is redirected to the input of the slave instrument.
Example:
·
master output = 80%
·
Slave Factor
= 50
slave instrument setpoint = 80% x 50%/100% = 40%
3.5
Adjusting zero point
The zero point of the instrument (the point at which it detects no flow) is factory adjusted at approximately 20 °C and
atmospheric pressure. If the ambient conditions or mounting position are significantly different, the instrument may detect
a flow when actually there is none. In that case, the instrument needs to be adapted to the new conditions by re-adjusting
the zero point.
Zeroing an instrument requires that:
·
the ambient conditions (temperature, pressure) match those of the operating environment of the instrument
·
the instrument is filled homogeneously with the operational media
·
there is absolutely no fluid flow through the instrument; preferably, this is done by closing valves directly after the outlet
of the instrument (control valve, shut-off valve)