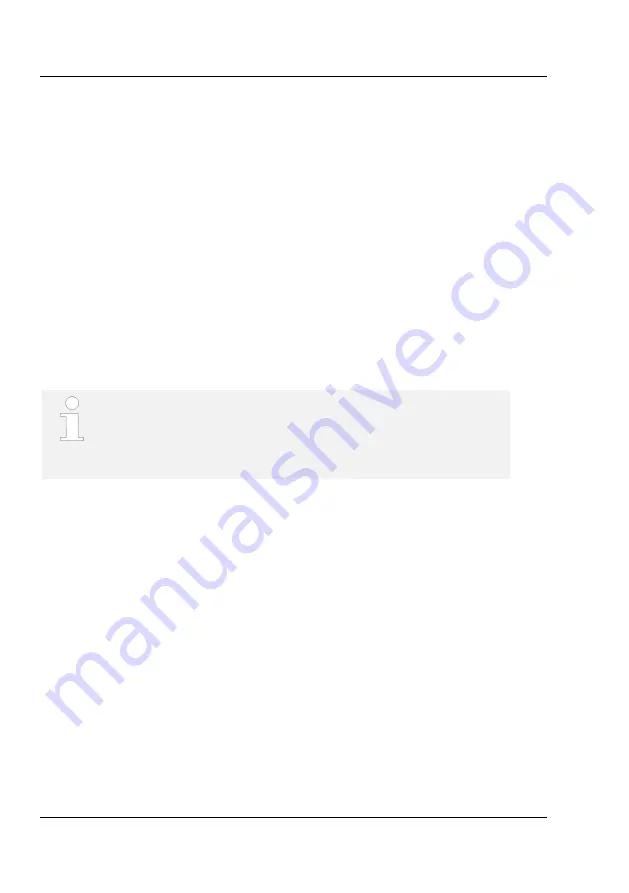
4 Installing the pump controller
42
bplogic intelligent pump controller
18/02/2021
The pump controller (Fig. 14/7) is connected to the machine tool that is to be
supplied (Fig. 14/5) via control line 1.
Control line 1 can be designed as a standard signal (Fig. 14/6) or field bus con-
nection (Fig. 14/4) by using digital or analog signals. The higher-level controller
(e.g. the machine tool
’s controller) works as the master. The higher-level con-
troller transfers its requirements (e.g. pressure increase) to the pump controller.
The pump controller communicates via control line 2 (Fig. 14/8) with the fre-
quency converters for the connected pumps (Fig. 14/9) and exchanges stan-
dard signals (0V-10V, 4mA-20 mA (Fig. 14/2) with the connected actuators and
sensors (e.g. pressure sensors, valves, Fig. 14/1) via the I/O modules.
4.3 Connecting the pump controller electrically
4.3.1 Basic layout of the I/O level
Illustrations in this operating manual are for basic understanding
and may differ from the actual design.
For the individual configuration, see the “Data for setting the
bplogic parameters” questionnaire.
The I/O level can be equipped with different I/O modules.
Fig. 15 shows the typical configuration of the pump controller with one I/O
module 1 (Fig. 15/A) and one I/O module 2 (Fig. 15/B).
Slot C always contains the same power module (Fig. 15/C).
If a slot is not allocated due to a special configuration, it is sealed using a cover
plate.