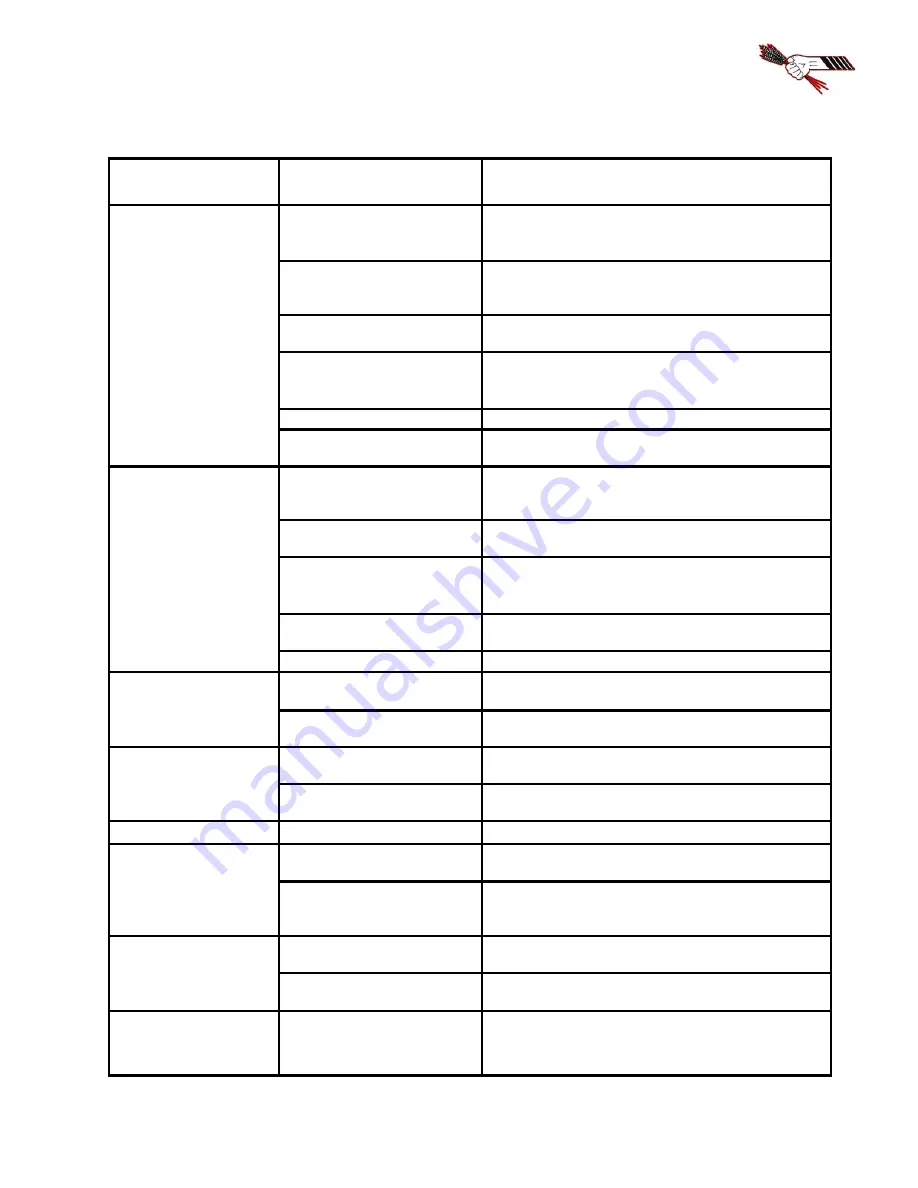
Bridgeview Manufacturing Inc.
35
Trouble-shooting Guide
Problem
Possible Cause
Remedy
Excessive main
shear bolt breakage
Engaging PTO at high engine
speed or too quickly
•
Idle tractor to engage PTO then bring up to full
operating speed
•
Feather PTO lever into position
Excessive twine wrapped on
rotor causing flail movement
to be restricted
•
Cut twine off rotor
Broken flails causing rotor to
be out of balance
•
Replace broken flails (in pairs opposite each other)
Overloading rotor
•
Set hoops to less aggressive position
•
Slow rotation of bale
•
Change direction of bale rotation
Incorrect shear bolt used
•
Use correct shear bolt
Operating machine at less than
1000 PTO RPM
•
Operate machine at rated 1000 PTO RPM
Excessive vibration
while processing
bales
Excessive twine wrapped on
rotor causing flail movement
to be restricted
•
Cut twine off rotor
Broken flails causing rotor to
be out of balance
•
Replace broken flails (in pairs opposite each other)
Overloading rotor
•
Set hoops to less aggressive position
•
Slow rotation of bale
•
Change direction of bale rotation
Operating machine at less than
1000 PTO RPM
•
Operate machine at rated 1000 PTO RPM
Rotor bearing failure
•
Replace failed parts
Agitators stopping
Excessive loose material in
tub causing agitator to jam
•
Reverse direction of bale rotation
•
Turn bale more slowly
Tractor relief pressure set too
low
•
Set tractor relief pressure to at least 2500 PSI
A single agitator
stopping
Mechanical flow divider valve
not functioning correctly
•
Contact your dealer for repairs
Coupler between motor and
agitator broken
•
Replace failed parts
No grain Flow
Flow control valve set too low
•
Increase flow rate in tractor or on flow control valve
Flow Control Valve
going over relief
Flow control valve relief
pressure set too low
•
Use hydraulic pressure gauge to ensure relief
pressure is set to 2200psi.
Auger chute at too shallow of
an angle for grain to clear fast
enough
•
Run auger slower
•
Run chute at steeper angle
3 Bale Kit not
clamping at full
pressure
Second bale is being lifted too
high before clamping
•
Lower fork height to horizontal before clamping
bale
Lockout mechanism is set too
early
•
Adjust lockout mechanism to stop clamp at higher
fork position
With 3 Bale Kit,
fork is not lifting to
full stroke
3 Bale Kit is slightly closed
•
Lower fork and open 3 Bale Kit fully before lifting
Summary of Contents for BALE KING 5300 Series
Page 46: ...Bridgeview Manufacturing Inc 42 Gearbox ...
Page 54: ...Bridgeview Manufacturing Inc 50 Rear Forks ...
Page 56: ...Bridgeview Manufacturing Inc 52 Deflector Hose Cover S N BK7168 Down ...
Page 58: ...Bridgeview Manufacturing Inc 54 S N BK7169 Up ...
Page 62: ...Bridgeview Manufacturing Inc 58 Hose Holder ...
Page 66: ...Bridgeview Manufacturing Inc 62 Left Arm ...
Page 68: ...Bridgeview Manufacturing Inc 64 Lockout Mechanism ...
Page 70: ...Bridgeview Manufacturing Inc 66 Center ...
Page 72: ...Bridgeview Manufacturing Inc 68 Right Arm ...
Page 74: ...Bridgeview Manufacturing Inc 70 TR Kit Option ...
Page 76: ...Bridgeview Manufacturing Inc 72 Tank Front ...
Page 78: ...Bridgeview Manufacturing Inc 74 Tank Rear ...
Page 80: ...Bridgeview Manufacturing Inc 76 Cross Auger ...
Page 82: ...Bridgeview Manufacturing Inc 78 Lid ...
Page 84: ...Bridgeview Manufacturing Inc 80 Fine Chop Option ...
Page 89: ...Bridgeview Manufacturing Inc 85 Hydraulics ...
Page 90: ...Bridgeview Manufacturing Inc 86 ...
Page 91: ...Bridgeview Manufacturing Inc 87 ...
Page 92: ...Bridgeview Manufacturing Inc 88 ...
Page 93: ...Bridgeview Manufacturing Inc 89 ...
Page 94: ...Bridgeview Manufacturing Inc 90 ...
Page 95: ...Bridgeview Manufacturing Inc 91 ...
Page 96: ...Bridgeview Manufacturing Inc 92 ...
Page 97: ...Bridgeview Manufacturing Inc 93 ...
Page 98: ...Bridgeview Manufacturing Inc 94 ...
Page 102: ...Bridgeview Manufacturing Inc 98 Lights Electrical Diverter Controls ...
Page 103: ...Bridgeview Manufacturing Inc 99 ...