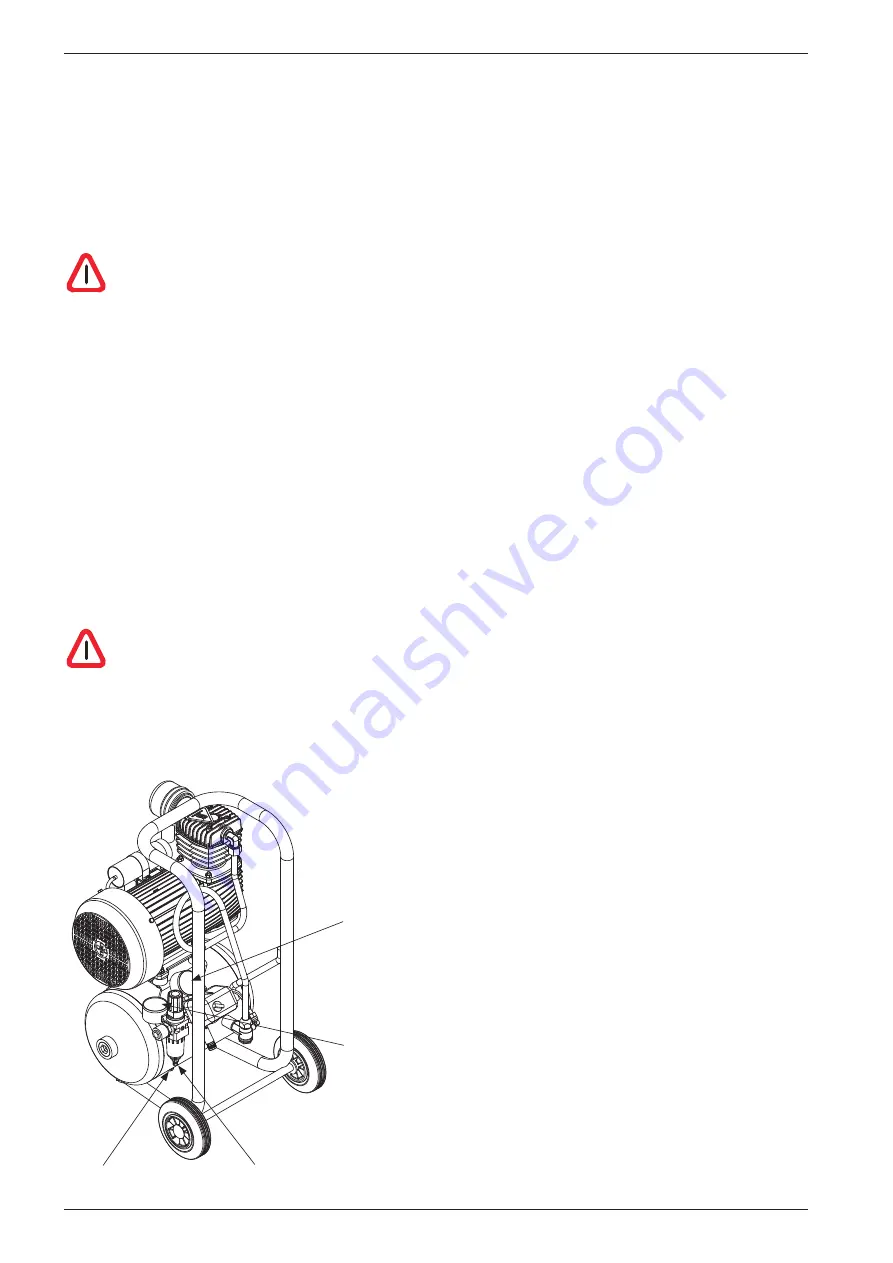
BRAILLO
l
B 650 SW2.1
22
2.8 Compressed air
This equipment requires clean, compressed air, minimum 7.0 bar @ 100 l/min., and max. temperature
50° C to the regulator to function. To make this compressed air, you will need to use some sort of
compressor. No matter what kind of compressor is chosen, there are some important things to re
-
member.
First, please read the enclosed instruction manual for the compressor!
There are many different compressor types on the market, and this chapter will not deal with a
particular compressor, but will discuss the topic more in general. Please see the figure below for an
example, but refer to your compressor manual for the specific information.
Normally a compressor have two pressure gauges and a pressure regulator fitted. The first gauge is
measuring the tank pressure (before the regulator) and the second gauge is measuring the output
pressure (after the regulator). The pressure at the compressor outlet must be adjusted to approx.
seven bar. This can be controlled at the output pressure gauge.
To have long and trouble free operation, the air must be filtered and free from oil and water.
When air is compressed in a compressor, the air temperature is rising. So the air entering the tank will
be hot. When the air is cooling down, the humidity in the air will condensate inside the tank. So the
warmer and more humid the air entering the compressor is, the more water condensates inside the
tank. The compressor is lubricated with oil and small amounts of oil may also get into the tank.
This means that the tank must be drained for oil and water on a regular basis.
If the air is supplied from the smaller types of compressors delivered from Braillo Norway AS, it is
required to keep the compressor in a similar environment as described for the Printer itself. (Temper
-
ature 15 - 30°C (60 - 86°F) and rel. humidity 40 - 60%).
Tank drainage
Filter drainage
Tank pressure
gauge
Output pressure gauge (ad-
just to 7 bar)
If the compressor is placed in a more harsh
environment, it might be necessary to take
further precautions to remove oil and water
from the air.
Basic elements on a compressor: