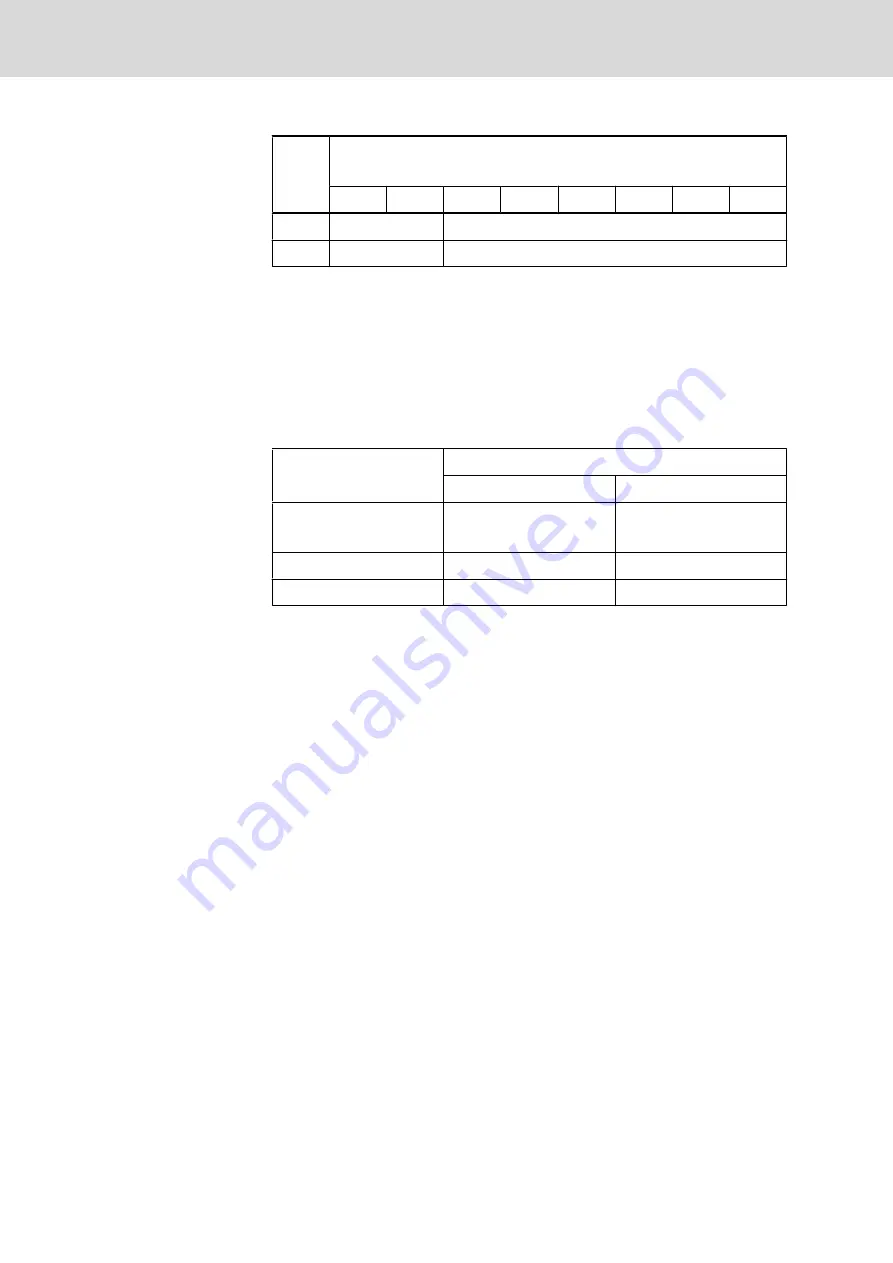
Direc‐
tion
Maximum permissible vibration load (10-2,000 Hz)
for MKE motors in dependance on the encoder design
A
B
C
D
G
K
N
P
axial
10 m/s²
10 m/s²
radial
30 m/s²
10 m/s²
Fig.9-13:
Permissible vibration load for MSK motors
9.8
Shock
The shock load of the motors is indicated by providing the maximum permitted
acceleration in non-stationary use, such as during transport.
Damage to functions is prevented by maintaining the limit values specified.
Based on DIN EN 60721-3-3 and DIN EN 60068-2-6, the following values result
for Rexroth motors:
Size
Maximum permitted shock load (6 ms)
axial
radial
MKE037
MKE047
10 m/s²
1000 m/s²
MKE098
10 m/s²
300 m/s²
MKE118
10 m/s²
200 m/s²
Fig.9-14:
Permitted shock load for MSK motors
9.9
Output Shaft and Shaft Sealing Ring
9.9.1
Plain Shaft
The standard design recommended for MKE motors provides a non-positive
friction-locked shaft-hub connection without play and excellent running smooth‐
ness. Use clamping sets, clamping sleeves or clamping elements to couple the
machine elements to be driven.
9.9.2
Output Shaft with Key
The optional key according to DIN 6885, Sheet 1, version 08-1968, permits
keyed transmission of torques with constant direction, with low requirements
for the shaft-hub connection.
84/131
Bosch Rexroth AG | Electric Drives
and Controls
Rexroth MKE Synchronous Motors | Project Planning Manual
Operating Conditions and Application Notes