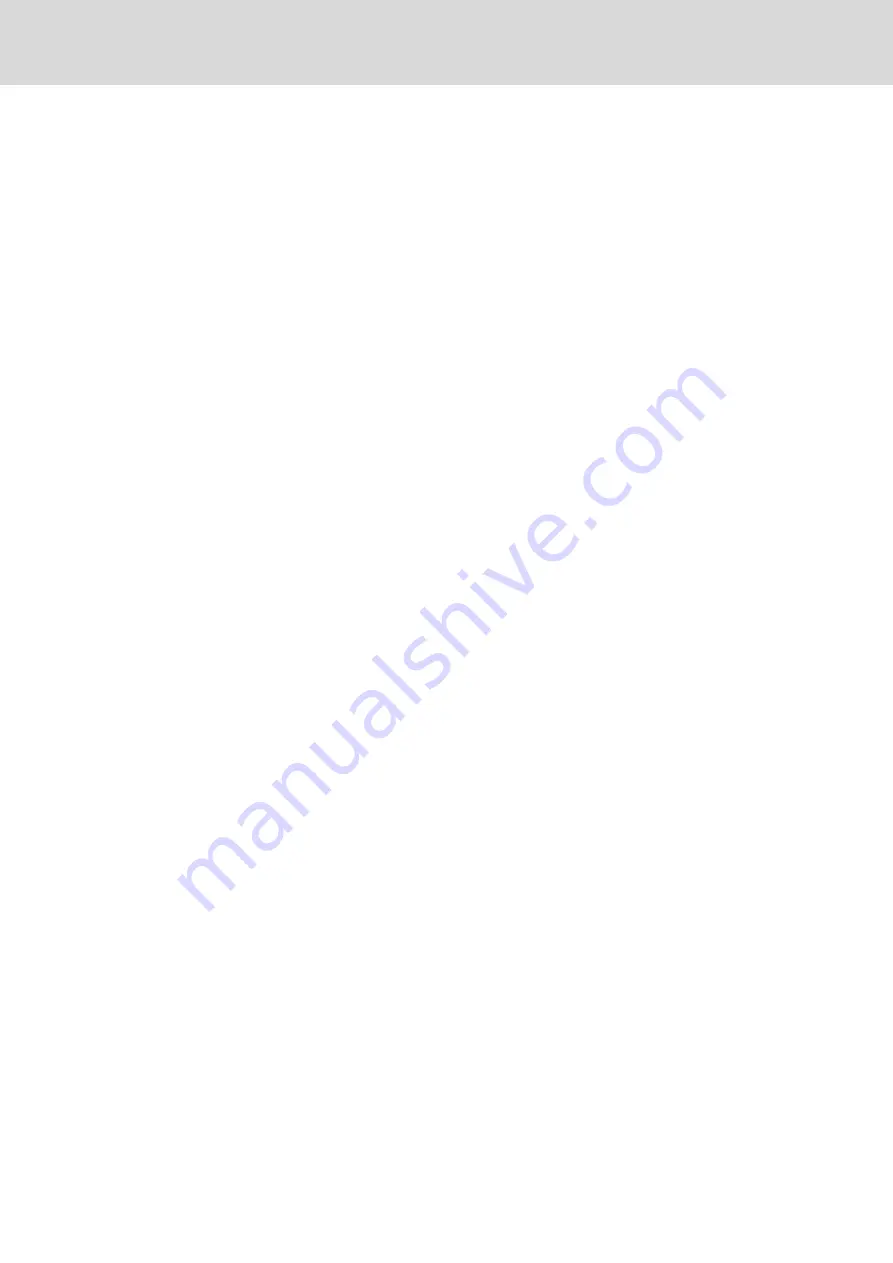
5
Functional principle of integrated safety technology
5.1
Basic functions
5.1.1
Overview
In the case of a standard drive, the axis / spindle / roll is moved according to
the command values of the control unit. In this case, incorrect drive motion
can be caused by operating errors, incorrect installation in the system,
defects in parts or materials, failures in the system, etc. Incorrect drive motion
- even if the errors only occur for a short time and occasionally - can
endanger persons staying in the danger zone of the drive motion.
You therefore have to take measures that limit the effects of errors on the
drive motion to a minimum. The residual risk of danger to persons is then
considerably reduced.
During operation, the safety functions are monitored by the drive system. For
this purpose, measures for detecting static error states were realized in the
system:
●
Dual-channel structure
●
Comparison of the states of both channels
●
Dynamization of static states
These measures ensure that a single error cannot cause the safety functions
to be lost.
The installation or machine manufacturer has to determine in how far this is
sufficient for an existing installation or machine by a risk assessment
according to annex I of the Directive 2006/42/EC.
The following schematic diagram of an IndraDrive Cs device illustrates the
basic functions and functional principles explained in this section. (The
described basic functions and functional principles apply to IndraDrive Cs,
IndraDrive Mi with Kxx02, IndraDrive C/IndraDrive M with Cxx02 control
sections and IndraDrive ML with Cxx02.5 control sections):
DOK-INDRV*-SI3-**VRS**-AP06-EN-P
Rexroth IndraDrive Integrated Safety Technology "Safe Torque Off" (as of MPx-16)
Bosch Rexroth AG
43/149
Functional principle of integrated safety technology
LSA Control S.L. www.lsa-control.com [email protected] (+34) 960 62 43 01