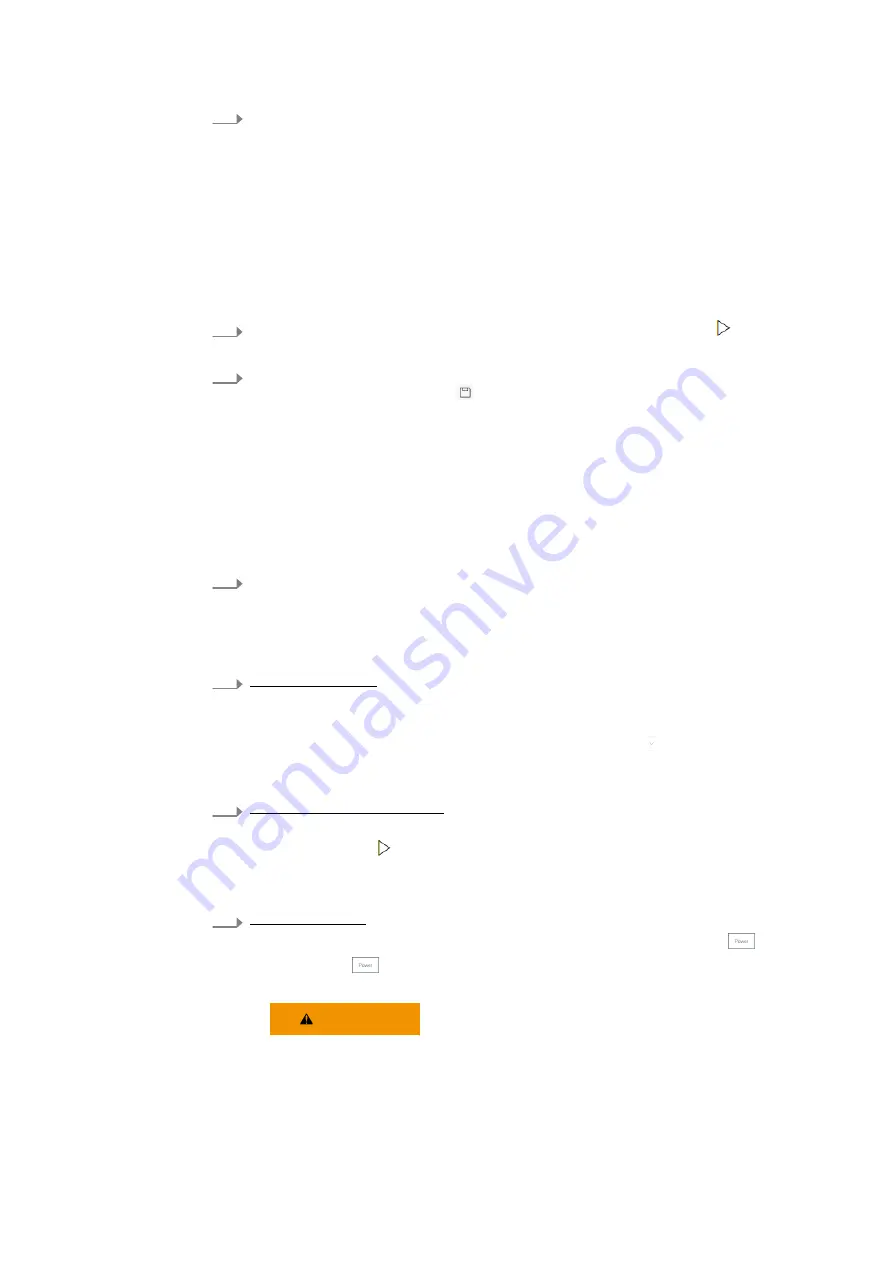
18
ctrlX AUTOMATION First Steps
Step 10 – Commissioning an axis
Bosch Rexroth AG R911403760
Edition 01
7.
Select the respective device variable for each axis profile
●
Inputs:
–
position = AT.Position_feedback_value_1
–
statusword = AT.Power_supply_status_word
●
Outputs:
–
controlword = MDT.Master_control_word
–
position = MDT.Position_command_value
To confirm the assignment, select the button
“Assign”
and exit the dialog
with the Button
“Cancel”
.
The configured axis is in the state “Disabled”.
8.
Switch the Motion mode to the [Running] state using the button .
The Motion switches to the [Running] state.
9.
To save the axis configuration remanently on the control, i.e. also after
switch-off, select the button (Save axis/kinematics configuration) at the
end.
A notification confirms that the configuration was saved.
5.10
Step 10
–
Commissioning an axis
After an axis has been created in step 9 and ctrlX Drive has been assigned, the
axis is commissioned in this step.
Commissioning an axis
1.
In the ctrlX CORE side navigation, navigate to the window
“Motion
Axis
Commissioning”.
The Motion operating state can be commanded, axes selected, their
motion values defined and traversed via a jog command in the
“Axis
Commissioning”
window.
2.
Selecting the axis
If only one axis was configured, it is already shown in the table.
If multiple axes are configured, one axis has to be selected for commis-
sioning. In the
“Axis”
table column, click on the button and select the
axis.
The axis is shown in the table.
3.
Selecting the Motion mode
To switch the Motion to the [Running] state, go to the command bar and
select the button .
The Motion is switched to the
“[Running]”
state.
The selected axis is in the
“Disabled”
state.
4.
Enabling an axis
Switch the axis to the
“ON (AF)”
operating mode using the button
.
The button
is green and the axis is in the
“STANDSTILL”
state.
The axis can now be traversed.
WARNING
The following actions cause machine motions.
Take all required measures to avoid personal injury or machine dam-
ages!
Summary of Contents for rexroth ctrlX AUTOMATION
Page 1: ...ctrlX AUTOMATION First Steps Quick Start Guide R911403760 Edition 01 ...
Page 8: ...8 ctrlX AUTOMATION First Steps Bosch Rexroth AG R911403760 Edition 01 ...
Page 10: ...10 ctrlX AUTOMATION First Steps Bosch Rexroth AG R911403760 Edition 01 ...
Page 24: ...24 ctrlX AUTOMATION First Steps Bosch Rexroth AG R911403760 Edition 01 ...
Page 26: ...26 ctrlX AUTOMATION First Steps Bosch Rexroth AG R911403760 Edition 01 ...
Page 28: ...28 ctrlX AUTOMATION First Steps Bosch Rexroth AG R911403760 Edition 01 ...
Page 30: ...30 ctrlX AUTOMATION First Steps Bosch Rexroth AG R911403760 Edition 01 ...
Page 32: ...32 ctrlX AUTOMATION First Steps ctrlX PLC Engineering Bosch Rexroth AG R911403760 Edition 01 ...
Page 34: ...34 ctrlX AUTOMATION First Steps Bosch Rexroth AG R911403760 Edition 01 ...