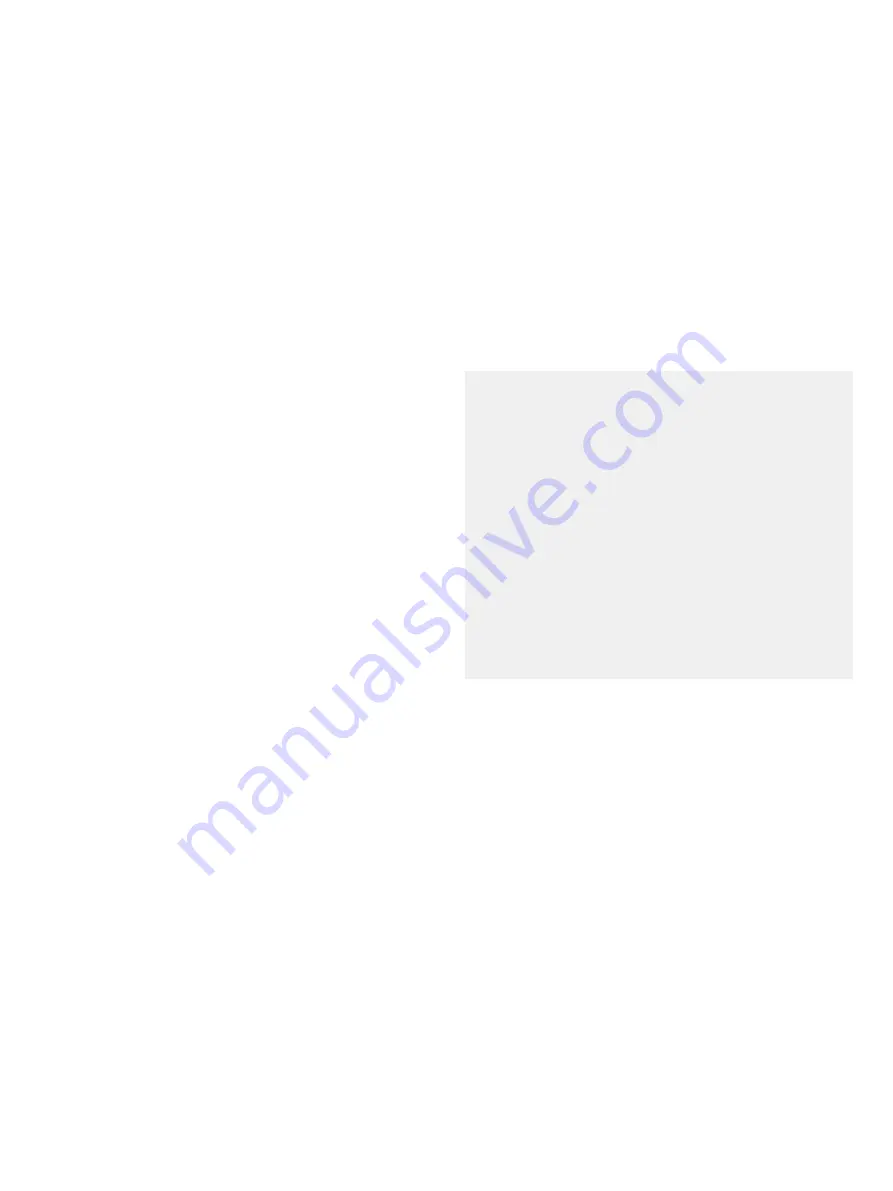
RE 95528/05.2016,
Bosch Rexroth AG
Counterbalance valve |
BVD/BVE Series 52
Project planning notes
13
Project planning notes
▶ The BVD/BVE counterbalance valve is intended for use
in an open circuit.
▶ The project planning, installation and commissioning of
the counterbalance valve require the involvement of
qualified skilled personnel.
▶ Before using the counterbalance valve, please read the
corresponding motor instruction manual completely and
thoroughly. If necessary, these can be requested from
Bosch Rexroth.
▶ Before finalizing your design, please request a binding
installation drawing.
▶ The specified data and notes contained herein must be
observed.
▶ For safety reasons, controls with beginning of control at
V
g min
(e.g., HA) are not permissible for winch drives,
e.g. anchor winches.
▶ Depending on the operating conditions of the axial
piston unit (working pressure, fluid temperature), the
characteristic curve may shift.
▶ Preservation: Our axial piston units are supplied as
standard with preservative protection for a maximum of
12 months. If longer preservative protection is required
(maximum 24 months), please specify this in plain text
when placing your order. The preservation periods apply
under optimal storage conditions, details of which can
be found in the data sheet 90312 or the motor instruc-
tion manual.
▶ Not all versions of the product are approved for use in
a safety function according to ISO 13849. Please consult
the responsible contact person at Bosch Rexroth if you
require reliability parameters (e.g. MTTF
d
) for functional
safety.
▶ Please note the details regarding the tightening torques
of port threads and other threaded joints in the motor
instruction manual.
▶ Working ports:
– The ports and fastening threads are designed for the
specified maximum pressure of the counterbalance
valve. The machine or system manufacturer must ensure
that the connecting elements and lines correspond to
the specified application conditions (pressure, flow,
hydraulic fluid, temperature) with the necessary safety
factors.
– The working ports and function ports are only
intended to accommodate hydraulic lines.
▶ System optimization (reduction) for the first prototype
is recommended with regard to the valve block, axial
piston motor, counterbalance valve and holding brake.
▶ The counterbalance valve converts the entire kinetic
energy/potential energy into heat during the braking/
lowering process. For this reason, sufficient cooling and/
or reservoir capacity must be provided.
▶ We recommend ordering an axial piston motor and
counterbalance valve as a single unit. This guarantees
optimum configuration and joint examination.
To avoid cavitation in the axial piston motor, the following
must be observed:
▶ The complete system must be designed in the customer
vehicle so that the counterbalance valve closes more
quickly than the control block in the customer vehicle.
The recommendation is a proportional valve with pro-
grammable ramp.
▶ Control block: the control spool should be designed with
a throttled A-B-T connection in the neutral position.
▶ An oil supply at port S of the motor reduces the risk of
cavitation. Ensure sufficient supply pressure and
quantity. An oil supply on the motor is recommended.
▶ During commissioning, it must be ensured that all
boundary conditions, e.g. minimum pressure at the
motor input, are observed.
Ordering details
When placing the order, the following parameters are neces-
sary to ensure correct acceptance at our test benches:
▶ Motor type code
▶ Counterbalance valve type code
▶ Flow
▶ Application (e.g. winch, track drive)
▶ Pressure setting of the secondary pressure relief valves
in the motor
For the design of the brake release valve, we require the
minimum pressure for releasing the mechanical holding brake.
Counterbalance valve and axial piston motor can be ordered
as a ready-assembled and tested assembly group.