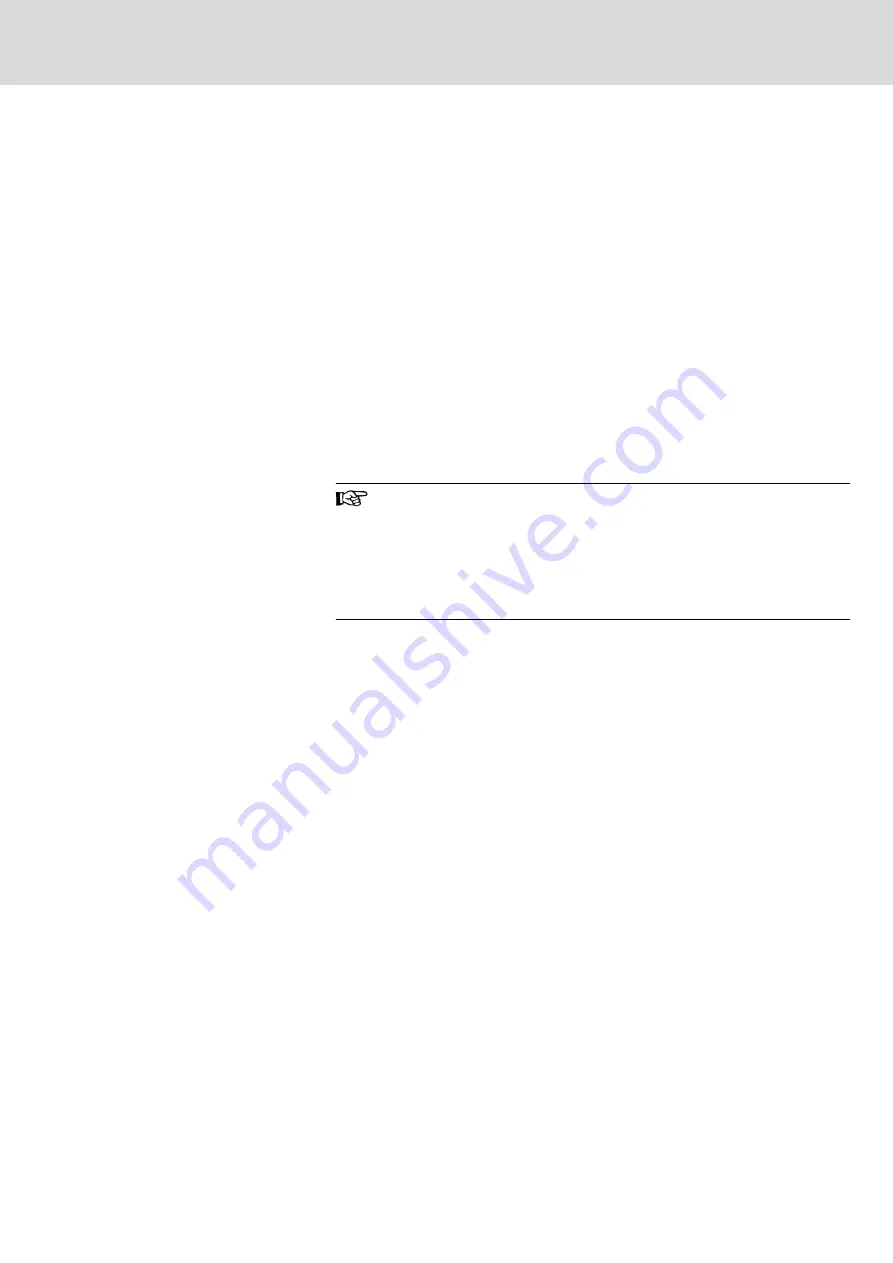
Contamination can reduce the flow rate of the fans and lead to thermal over‐
load of the motors. When the motors are operated in a dirty environment, the
availability of the system is increased by cleaning the fans and motor cooling
fins at regular intervals. When designing the machine, consider the accessi‐
bility of motor and fan for maintenance work. Special instructions for mainte‐
nance and troubleshooting of motor fans can be found in
.
9.12.3
Liquid cooling
General information
Rexroth motors in liquid-cooled version are suitable for increased loads, e.g.
for continuous start-stop operation with high repetition frequencies. MSK mo‐
tors for liquid cooling are marked with “FN” in the type code.
Coolant duct
Coolant ducts can be designed as
●
pipeline system or
●
as hose
system.
Due to the deflection points occurring in piping systems (e.g. 90°
bends), pressure losses occur in the coolant lines. Therefore we
recommend hose line systems.
When selecting the coolant lines, the pressure drop within the
system must be taken into account. For longer lengths, the inner
diameter of the cables should therefore be at least 9 mm and tap‐
er only shortly before connection to the motor.
Operating pressure
The maximum coolant inlet pressure of 6 bar shall be applicable to all MSK
motors. For motors manufactured before 2010-01-01 FD 10W01 the inlet
pressure must be limited to 3 bar.
Please observe that additional screw connections or junctions in the cooling
circuit can have an influence on the flow and supply pressure of the cooling
medium. The pressure drop Δp
n
of the liquid-cooled motors is specified in the
technical data.
Pressure drop
The flow of the coolant in the drive component is exposed to cross-sectional
and directional changes. Friction and deflection losses thus occur in the com‐
ponent. These losses appear in the form of a pressure drop Δp.
It refers to the indicated flow rate of the coolant water. If the flow rate is con‐
verted to a different temperature increase, the pressure drop must be taken
from the following characteristic curve.
DOK-MOTOR*-MSK********-PR12-EN-P
Bosch Rexroth AG
227/279
Synchronous Servomotors MSK
Operating conditions and application notes
Summary of Contents for MSK030B-0900-NN
Page 1: ...Synchronous Servomotors MSK Project planning manual R911296289 Edition 12 ...
Page 12: ...Bosch Rexroth AG DOK MOTOR MSK PR12 EN P 10 279 Synchronous Servomotors MSK ...
Page 24: ...Bosch Rexroth AG DOK MOTOR MSK PR12 EN P 22 279 Synchronous Servomotors MSK ...
Page 160: ...Bosch Rexroth AG DOK MOTOR MSK PR12 EN P 158 279 Synchronous Servomotors MSK ...
Page 180: ...Bosch Rexroth AG DOK MOTOR MSK PR12 EN P 178 279 Synchronous Servomotors MSK ...
Page 238: ...Bosch Rexroth AG DOK MOTOR MSK PR12 EN P 236 279 Synchronous Servomotors MSK ...
Page 242: ...Bosch Rexroth AG DOK MOTOR MSK PR12 EN P 240 279 Synchronous Servomotors MSK ...
Page 248: ...Bosch Rexroth AG DOK MOTOR MSK PR12 EN P 246 279 Synchronous Servomotors MSK ...
Page 260: ...Bosch Rexroth AG DOK MOTOR MSK PR12 EN P 258 279 Synchronous Servomotors MSK ...
Page 268: ...Bosch Rexroth AG DOK MOTOR MSK PR12 EN P 266 279 Synchronous Servomotors MSK ...
Page 274: ...Bosch Rexroth AG DOK MOTOR MSK PR12 EN P 272 279 Synchronous Servomotors MSK ...
Page 276: ...Bosch Rexroth AG DOK MOTOR MSK PR12 EN P 274 279 Synchronous Servomotors MSK ...
Page 280: ...Notes Bosch Rexroth AG DOK MOTOR MSK PR12 EN P 278 279 Synchronous Servomotors MSK ...
Page 281: ...Notes DOK MOTOR MSK PR12 EN P Bosch Rexroth AG 279 279 Synchronous Servomotors MSK ...