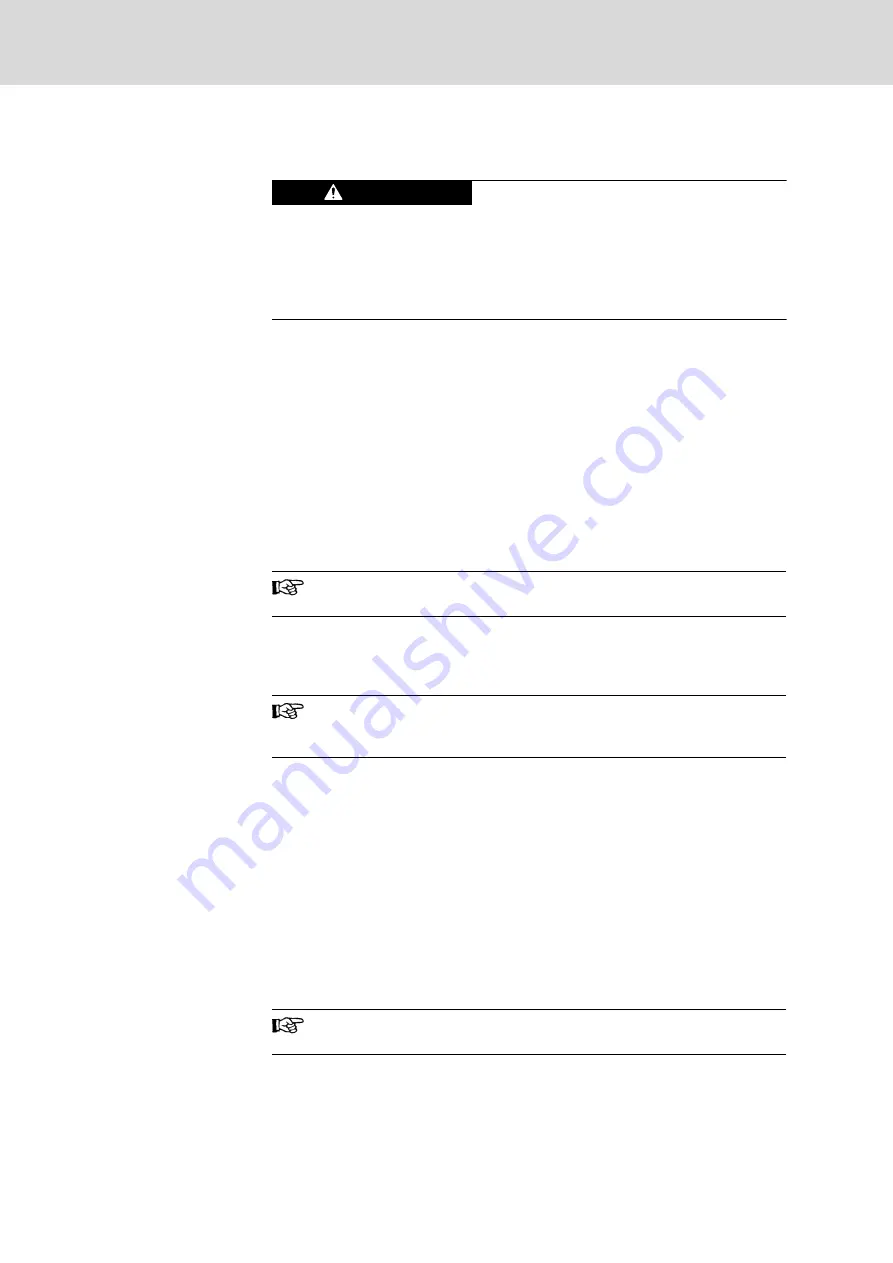
9.9
Attachment of drive elements
Motor damage by intrusion of liquid!
CAUTION
Pending liquids (e.g. cooling lubricants, gearbox oil, etc.) at the drive shaft
are inadmissible.
When installing gearboxes please use gearboxes with closed (oil-proof) lubri‐
cation system only. Gearbox oil should not be in permanent contact with the
shaft sealing ring of the motors.
For any type of attachment of drive elements to the output shaft, such as:
●
Transmissions
●
Couplings
●
Pinions
the following instructions must absolutely be observed.
Attachment of transmissions on
motors
chapter 7.1 "Transmission" on page 179
.
Over-determined arrangement
In general, an over-determined arrangement must be avoided when mounting
drive elements. The indispensable existing tolerances lead to additional
forces on the bearing of the motor shaft and, if necessary, to a significantly
reduced bearing life.
If an over-determined arrangement cannot be avoided, please
contact Bosch Rexroth.
Couplings
The machine design and the attachment elements used must be carefully
matched to the motor type so that the load limits of shaft and bearing are not
exceeded.
When mounting extremely rigid couplings, an unacceptably high
load on the shaft and bearing can occur due to a radial force
which constantly changes the angular position.
Bevel pinion or helical drive pin‐
ions
Due to thermal effects, the flange end of the output shaft can shift by up to
0.6 mm in relation to the motor housing. When using helical drive pinions or
bevel gear pinions mounted directly on the output shaft, this change in length
leads to
●
a shift in the position of the axis, if the driving pinions are not axially
fixed on the machine side,
●
a thermally dependent component of the axial force, if the driving pin‐
ions are axially fixed on the machine side. There is a risk that the maxi‐
mum permissible axial force will be exceeded or that the backlash within
the gearing will increase excessively.
●
Damage to the B-side motor fixed bearing due to exceeding the maxi‐
mum permissible axial force.
Preferably use self-supported drive elements which are connec‐
ted to the motor shaft via axially compensating couplings!
Bosch Rexroth AG
DOK-MOTOR*-MSK********-PR12-EN-P
220/279
Synchronous Servomotors MSK
Operating conditions and application notes
Summary of Contents for MSK030B-0900-NN
Page 1: ...Synchronous Servomotors MSK Project planning manual R911296289 Edition 12 ...
Page 12: ...Bosch Rexroth AG DOK MOTOR MSK PR12 EN P 10 279 Synchronous Servomotors MSK ...
Page 24: ...Bosch Rexroth AG DOK MOTOR MSK PR12 EN P 22 279 Synchronous Servomotors MSK ...
Page 160: ...Bosch Rexroth AG DOK MOTOR MSK PR12 EN P 158 279 Synchronous Servomotors MSK ...
Page 180: ...Bosch Rexroth AG DOK MOTOR MSK PR12 EN P 178 279 Synchronous Servomotors MSK ...
Page 238: ...Bosch Rexroth AG DOK MOTOR MSK PR12 EN P 236 279 Synchronous Servomotors MSK ...
Page 242: ...Bosch Rexroth AG DOK MOTOR MSK PR12 EN P 240 279 Synchronous Servomotors MSK ...
Page 248: ...Bosch Rexroth AG DOK MOTOR MSK PR12 EN P 246 279 Synchronous Servomotors MSK ...
Page 260: ...Bosch Rexroth AG DOK MOTOR MSK PR12 EN P 258 279 Synchronous Servomotors MSK ...
Page 268: ...Bosch Rexroth AG DOK MOTOR MSK PR12 EN P 266 279 Synchronous Servomotors MSK ...
Page 274: ...Bosch Rexroth AG DOK MOTOR MSK PR12 EN P 272 279 Synchronous Servomotors MSK ...
Page 276: ...Bosch Rexroth AG DOK MOTOR MSK PR12 EN P 274 279 Synchronous Servomotors MSK ...
Page 280: ...Notes Bosch Rexroth AG DOK MOTOR MSK PR12 EN P 278 279 Synchronous Servomotors MSK ...
Page 281: ...Notes DOK MOTOR MSK PR12 EN P Bosch Rexroth AG 279 279 Synchronous Servomotors MSK ...