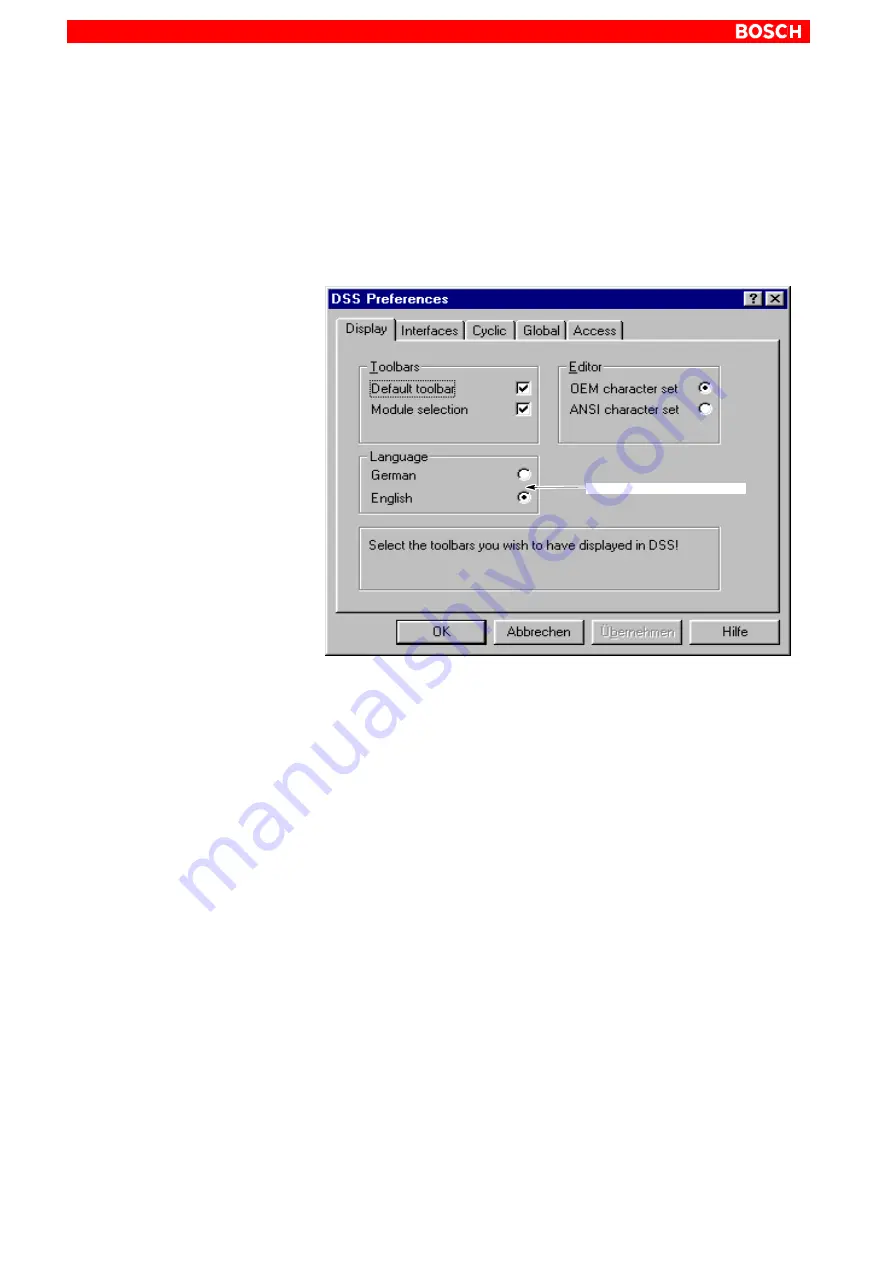
DSS User Interface
4–10
1070 066 028-101 (01.05) GB
4.5
Selecting the language
The DSS user interface language may be changed over, but not the parame-
ter and status texts.
Language of user interface
L
Select: EXTRAS
"
PREFERENCES
Changing over the language
L
To activate the new language, you have to reboot.