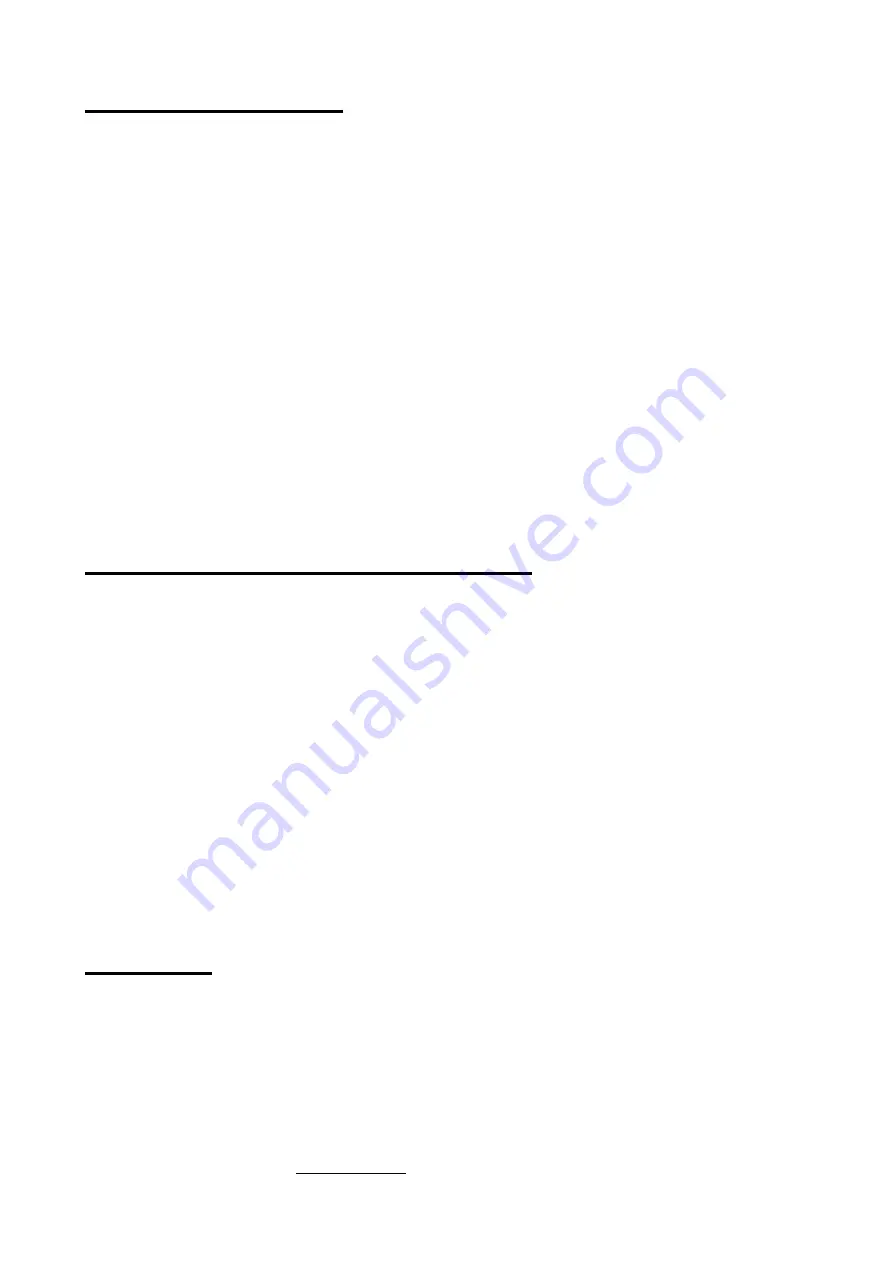
Operation
MX-3
Manual
Rev:00
6 / 12
Making Measurements
In order for the transducer to do its job, there must be no air gaps between the wearface
and the surface of the material being measured. This is accomplished with the use of a
„coupling“ fluid, commonly called „couplant“. This fluid serves to „couple“ or transmit the
ultrasonic sound waves from the transducer into the material and back again.
Before attempting to make a measurement, a small amount of couplant should be applied
to the surface of the material being measured. Typically, a single droplet of couplant is suf-
ficient.
After applying couplant, press the transducer (wearface down) firmly against the area to be
measured. The Stability Indicator should have six or seven bars darkened, and a number
should appear in the display.
If the
MX-3
has been properly „zeroed“ (see page 8) and set to the correct sound
velocity (see page 9 – 10), the number in the display will indicate the actual thickness of
the material directly beneath the transducer.
If the Stability Indicator has fewer than five bars darkened, or the numbers on the display
seem erratic, first check to make sure that there is an adequate film of couplant beneath
the transducer, and that the transducer is seated flat against the material. If the condition
persists, it may be necessary to select a different transducer (size or frequency) for the
material being measured (see page 11).
While the transducer is in contact with the material being measured, the
MX-3
will perform
four measurements every second, updating its display as it does so. When the transducer
is removed from the surface, the display will hold the last measurement made.
Condition And Preparation Of Surfaces
In any ultrasonic measurement scenario, the shape and roughness of the test surface are
of paramount importance. Rough, uneven surfaces may limit the penetration of ultrasound
through the material and result in unstable, and therefore unreliable, measurements.
The surface being measured should be clean and free of any small particulate matter, rust
or scale. The presence of such obstructions will prevent the transducer from seating pro-
perly against the surface. Often, a wire brush or scraper will be helpful in cleaning sur-
faces. In more extreme cases, rotary sanders or grinding wheels may be used, though ca-
re must be taken to prevent surface gouging, which will inhibit proper transducer coupling.
,Extremely rough surfaces, such as the pebble-like finish of some cast irons, will prove
most difficult to measure. These kinds of surfaces act on the sound beam like frosted glass
on light: the beam becomes diffused and scattered in all directions.
In addition to posing obstacles to measurement, rough surfaces contribute to excessive
wear of the transducer, particularly in situations where the transducer is „scrubbed“ along
the surface. Transducers should be inspected on a regular basis, for signs of uneven wear
of the wearface. If the wearface is worn on one side more than another, the sound beam
penetrating the test material may no longer be perpen-dicular to the material surface. In
this case, it will be difficult to exactly locate tiny irregularities in the material being meas-
ured, as the focus of the soundbeam no longer lies directly beneath the transducer.
Probe Zero
Setting the Zero Point of the
MX-3
is important for the same reason that setting the zero
on a mechanical micrometer is important. If the tool is not „zeroed“ correctly, all of the
measurements the tool makes will be in error by some fixed number. When the
MX-3
is
„zeroed“, this fixed error value is measured and automatically corrected for in all subse-
quent measurements.