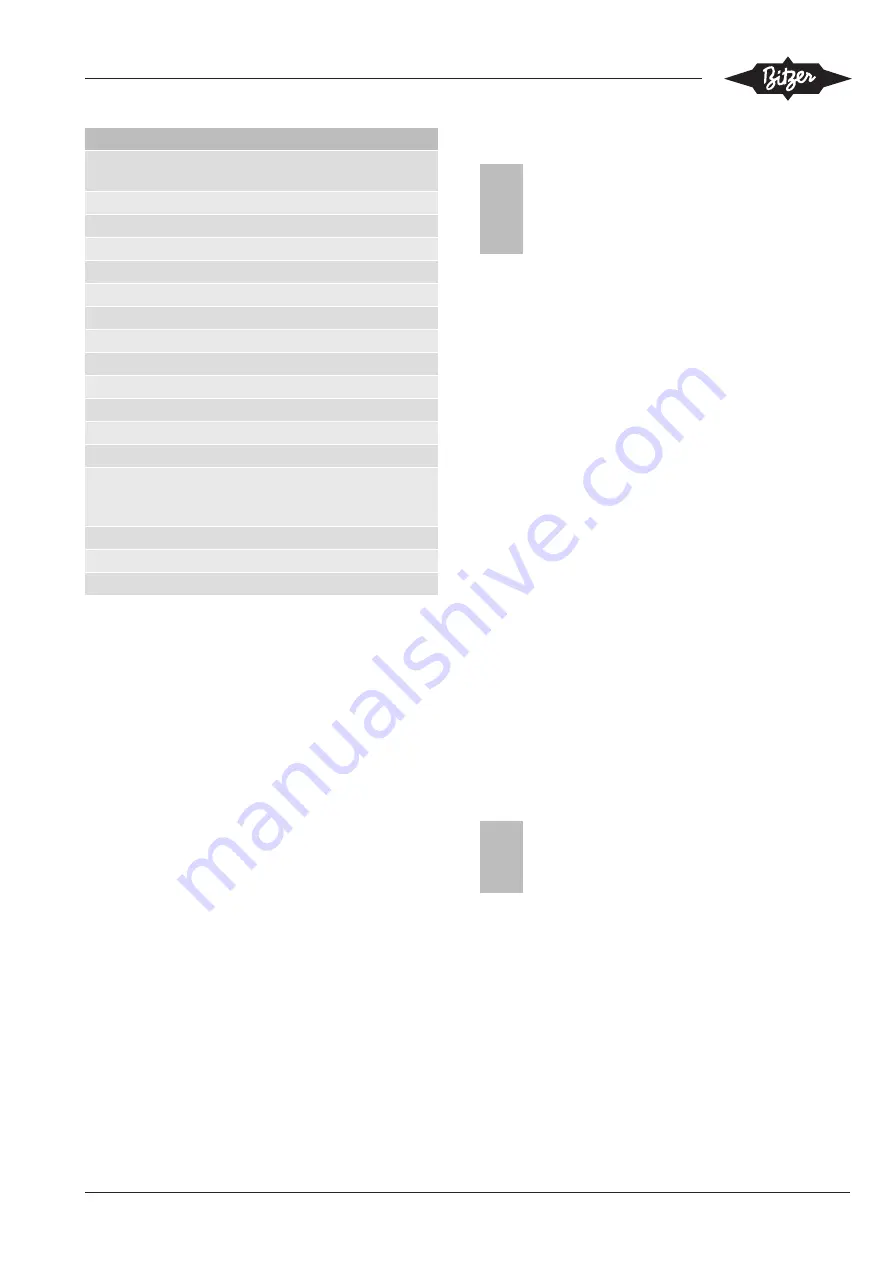
SB-520-2
27
Connection positions
9
Threaded bore for pipe fixture (ECO and LI
lines)
10
Maintenance connection for oil filter
11
Oil drain (oil filter)
13
Oil filter monitoring
14
Oil flow switch
15
Earth screw for housing
16
Pressure blow-off (oil filter chamber)
17
Maintenance connection for shaft seal
18
Liquid injection (LI)
19
Compressor module
20
Slider position indicator
21
Oil level switch
22
Oil pressure transmitter
23
Connection for oil and gas return (for sys-
tems with flooded evaporator adaptor op-
tional)
24
Access to oil circulation restrictor
SL
Suction gas line
DL
Discharge gas line
Tab. 1: Connection positions
Dimensions (if specified) may have tolerances accord-
ing to EN ISO13920-B.
The legend applies to all open drive and semi-hermetic
BITZER screw compressors and includes connection
positions that do not exist in every compressor series.
4.5.1
Additional connections for evacuation
In case of a great system volume, install generously
sized, lockable additional connections on the pressure
and suction side. Sections locked by check valves must
have separate connections.
4.5.2
Capacity control and start unloading
The OS.A95 compressors are equipped with an "infinite
capacity control" (slide control). The compressor mod-
ule controls the solenoid valves.
For the detailed descriptions of the capacity control,
see Technical Information ST-150.
For the start unloading, the compressor module sets
the capacity slider to the minimum displacement. For
this, a time period of approx. 5 min in the system con-
trol must be provided.
5
Electrical connection
!
!
NOTICE
Risk of short-circuit due to condensation water
in the terminal box!
Use only standardised cable bushings.
When mounting, pay attention to proper sealing.
Compressors and electrical equipment comply with the
EU Low Voltage Directive 2014/35/EU.
Connect mains cables, protective earth conductors and
other cables according to the description, see Tech-
nical Information ST-150. Observe EN60204-1, the
safety standard series IEC60364 and national safety
regulations.
5.1
Dimensioning components
▶ Select motor contactors, cables and fuses according
to the maximum operating current of the compressor
and the maximum power consumption of the motor
in case of direct-on-line start. With other starting
methods according to the lower load.
▶ Use the motor contactors according to the opera-
tional category AC3.
▶ Select overload protective devices in case of direct-
on-line start according to maximum operating current
of the compressor. With other starting methods ac-
cording to the lower operating current.
▶ Compare the voltage and frequency specifications
on the motor type plate with the data of the mains
supply. The motor may be connected only if the val-
ues match.
▶ Wire the terminals according to the instructions of
the motor manufacturer.
!
!
NOTICE
Risk of compressor failure!
Operate the compressor only in the intended ro-
tation direction!
5.2
Safety and protection devices
5.2.1
Compressor module
The compressor module monitors the essential operat-
ing parameters and protects the compressor from oper-
ation under critical conditions, see Technical Informa-
tion ST-150.