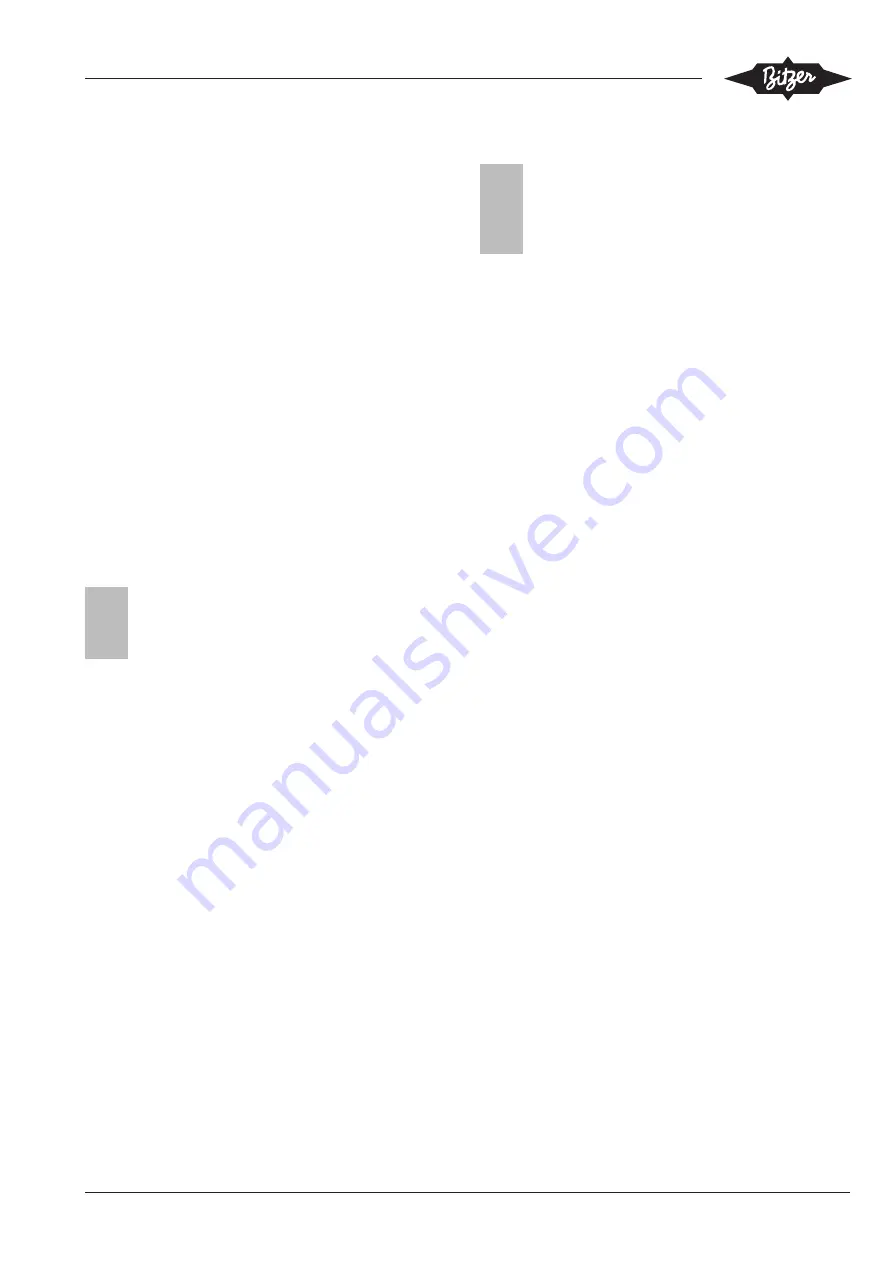
SB-110-4
51
no oil flow within 5 s, switch off immediately. Check oil
supply!
6.7.3
Set high pressure and low pressure
switches (HP + LP)
Check exactly the cut-in and cut-out pressure values
according to the operating limits by testing them.
6.7.4
Setting the condenser pressure control
▶ Set the condenser pressure so that the minimum
pressure difference is reached within 20 s after the
start.
▶ Avoid quick pressure reduction with finely stepped
pressure control.
6.7.5
Vibrations and frequencies
Check the system carefully to detect any abnormal vi-
bration, check particularly pipes and capillary tubes. In
case of strong vibrations, take mechanical measures:
for example use pipe clamps or install vibration
dampers.
!
!
NOTICE
Risk of burst pipes and leakages on the com-
pressor and system components!
Avoid strong vibrations!
6.7.6
Checking the operating data
• Evaporation temperature
• Suction gas temperature
• Condensing temperature
• Discharge gas temperature
– min. 20 K above condensing temperature
– min. 30 K above condensing temperature for
R407C, R407F and R22
– max. 100°C on the outside of the discharge gas
line
• Oil temperature: see chapter Application ranges,
• Cycling rate
• Current values
• Voltage
▶ Prepare data protocol.
For application limits, see BITZER Software and bro-
chure SP-100.
6.7.7
Control logic requirements
!
!
NOTICE
Risk of motor failure!
The control logic of the superior system control-
ler must meet the specified requirements in any
case.
• Desirable minimum running time: 5 minutes!
• Minimum standstill time:
– 5 minutes
This is the time the control slider needs to reach
the optimal start position.
– 1 minute
Only if the compressor has been shut off from the
25%-CR step!
– Also observe minimum standstill times during
maintenance work!
• Maximum cycling rate:
– 6 to 8 starts per hour
• Switching time of the motor contactors:
– Part winding: 0.5 s
– Star-delta: 1 to 2 s.
6.7.8
Particular notes on safe compressor and
system operation
Analysis show that compressor failures are most often
due to an inadmissible operating mode. This applies
especially to damage resulting from lack of lubrication:
• Function of the expansion valve – observe the manu-
facturer’s notes!
– Position the temperature sensor correctly at the
suction gas line and fasten it.
– When using a liquid suction line heat exchanger:
Position the sensor as usual after the evaporator
– in no case after the heat exchanger.
– Ensure sufficiently high suction gas superheat,
while also taking into account the minimum dis-
charge gas temperatures.
– Stable operating mode under all operating and
load conditions (also part-load, summer/winter op-
eration).
– Bubble-free liquid at the expansion valve inlet,
during ECO operation already before entering the
liquid subcooler.