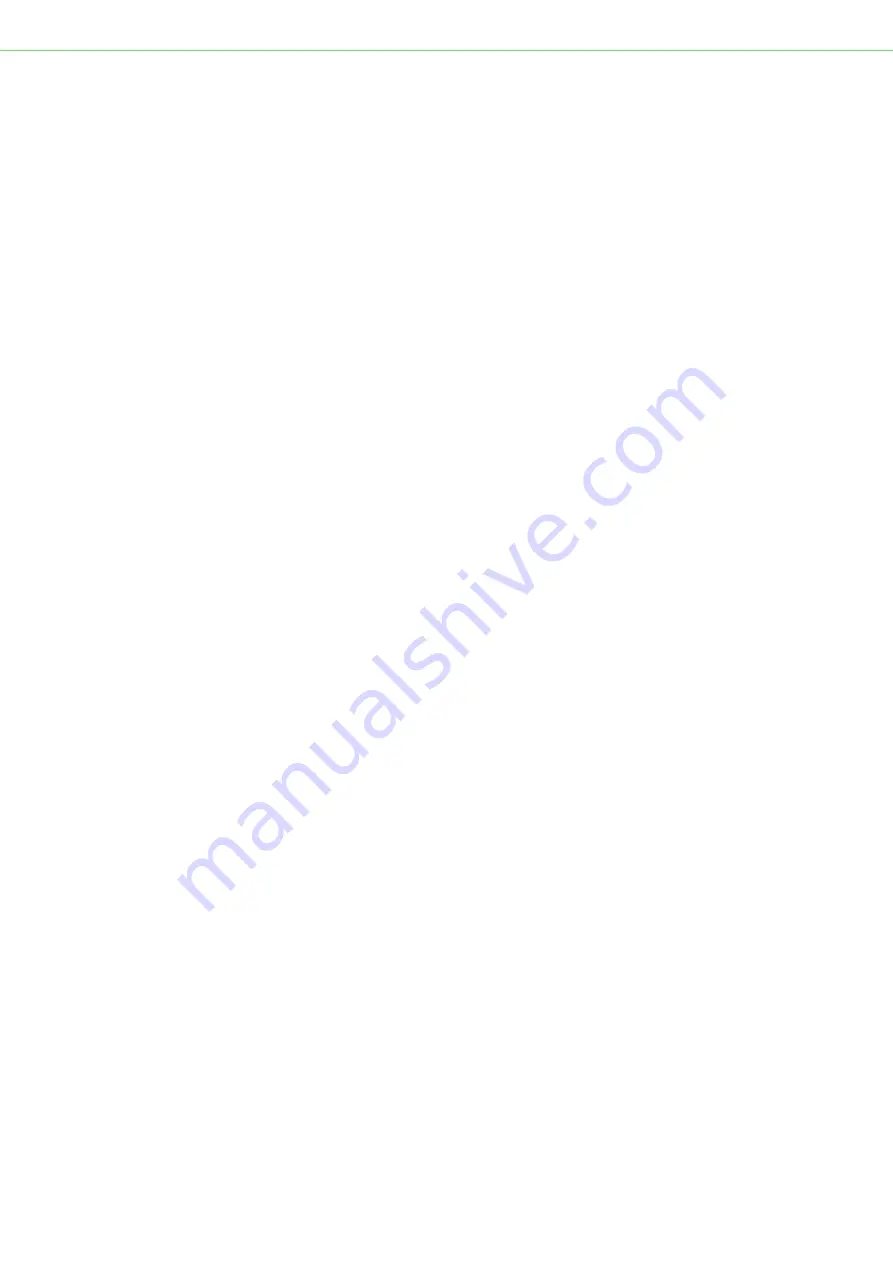
4. Functions
The OLC series consists of the two models, OLC-D1 and
OLC-K1. They have different monitoring functions which
are listed in the following.
4.1. Level monitoring
The OLC series consists of a screw-in prism unit and an
optical level detection device. The prism unit is installed in
the compressors oil chamber or in the vessel.
The level detection device can be replaced without open-
ing to the pressurized part of the compressor or vessel.
Detection of the level is via infrared light. There is a built-in
monitoring system for correct installation.
4.2. Oil level monitoring
The OLC-K1 is used for contactless oil level monitoring in
compressors in order to safeguard sufficient lubrication of
the internal mechanics.
As the refrigerant can be absorbed by oil, fluctuation of
the oil level in the compressor is common in refrigeration
systems and thereby oil levels need to be monitored.
OLC-K1 is for compressor use and locks out if oil level is
not sufficient after 90 seconds of compressor operation.
4.3. Level monitoring in vessels
The OLC-D1 is meant for level monitoring in vessels and
does not have the operation recognition input needed for
compressor operation.
The OLC-D1 releases the relay if the level is too low and
activates the relay if the level is valid. There is a 5 seconds
time delay between switching the relay.
4.4. Red LED status light
At start-up, the OLC will flash shortly with the LED. After
approx. 3 seconds the relay will be activated.
For OLC-D1 the level monitoring starts immediately; for
the OLC-K1 monitoring starts when the D1 signal is applied
and after the 90 seconds delay time the level is evaluated.
If the oil level is too low or there is a failure, the relay will be
opened and the LED will signal the failure.
• LED Off: Oil level good, no failures
• LED On: Oil level low
• LED flashing: OLC not correctly mounted, or Supply
voltage too low, or Internal failure
Page 6