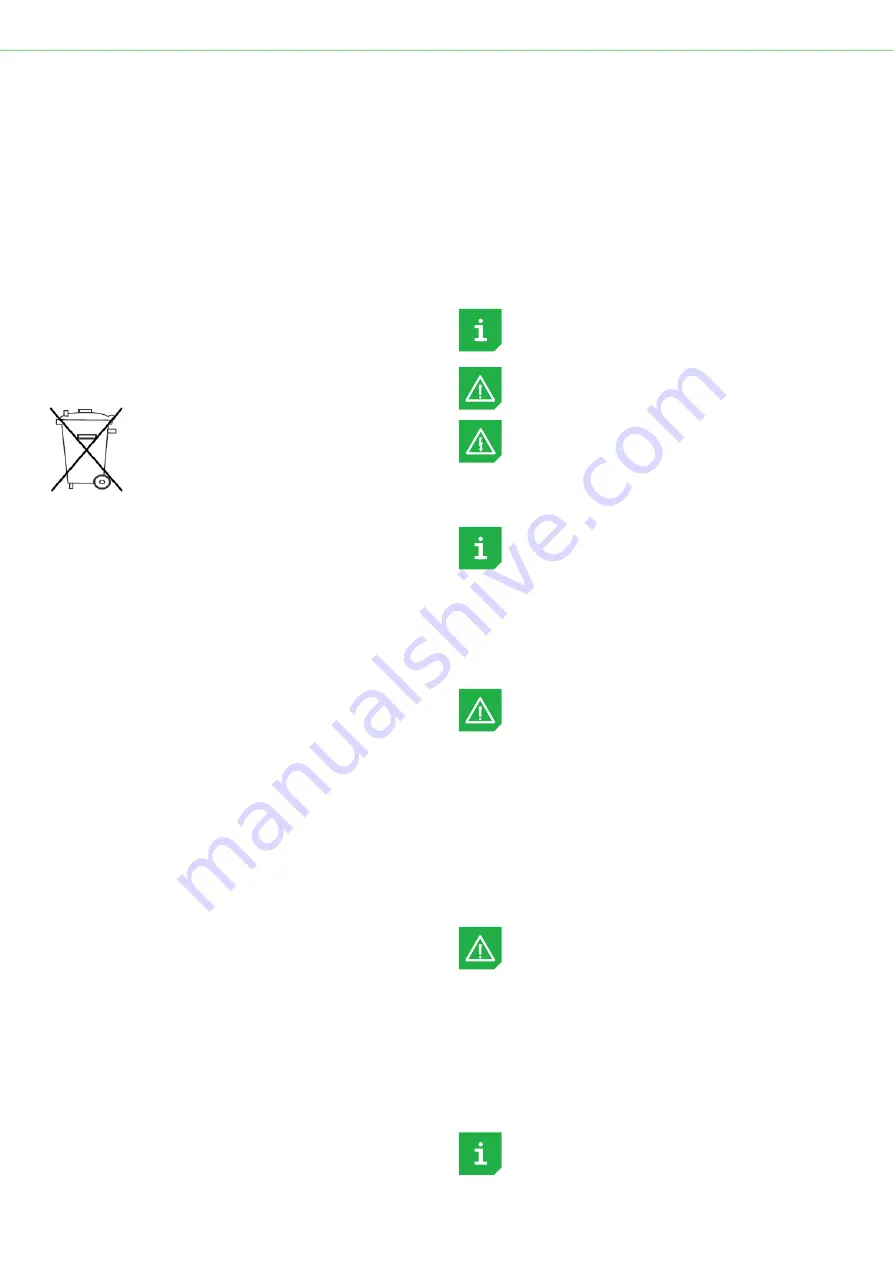
1. Read this first
The contents of this manual are subject to change without
notice. Lodam electronics holds the copyright to this user’s
manual. The user shall follow any instructions given in this
user manual entirely and not only partly. Any non-follow-
ing of this user manual result in exclusion of all warranties,
guarantees, and liabilities. Copyright© 2014 by Lodam
electronics a/s. All Rights Reserved.
Disposing of the parts of the controller:
INFORMATION FOR USERS ON THE
CORRECT HANDLING OF WASTE ELECTRI-
CAL AND ELECTRONIC EQUIPMENT (WEEE)
In reference to European Union directive 2002/96/
EC issued on 27 January 2003 and the related national
legislation, please note that:
1. WEEE cannot be disposed of as municipal waste and
such waste must be collected and disposed of sepa-
rately;
2. The public or private waste collection systems defined
by local legislation must be used. In addition, the equip-
ment can be returned to the distributor at the end of its
working life when buying new
equipment;
3. The equipment may contain hazardous substances:
the improper use or incorrect disposal of such may
have negative effects on human health and on the
environment;
4. The symbol (crossed-out wheeled bin) shown on the
product or on the packaging and on the instruction
sheet indicates that the equipment has been intro-
duced onto the market after 13 August 2005 and that it
must be disposed of separately;
5. In the event of illegal disposal of electrical and elec-
tronic waste, the penalties are specified by local waste
disposal legislation.
1.1. Reading instructions
The following symbols are used to draw the reader’s
attention to different warning levels.
Important information.
Danger!! General danger.
Danger of electrical current or voltage.
1.2. User manual
Before installation the user should be thoroughly
familiarized with this user manual, especially with
purposes, installation and operation.
Special care should be taken when installing and connect-
ing external equipment (high voltage etc.) and handling
the modules correctly according to protection against ESD.
Installation of the OLC-D1/OLC-K1 must be
performed by authorized personnel only. All valid
national legislations regarding electrical installa-
tions must be observed.
All warranties are excluded in case installation is per-
formed by unauthorized personnel or in case the OLC-D1/
OLC-K1 has not been correctly installed.
1.3. Safety
The OLC-D1/OLC-K1 is a protection device and not
a safety component according to the Machinery
Directive and cannot be used in “medical” or “life
support” equipment.
Before plant commissioning the service technician shall
ensure that personal safety requirements are met in
conformity with the Machinery Directive on the basis of
safety estimations.
Electrical plant failures are to be immediately
solved, even though no immediate danger exists;
the OLC-D1/OLC-K1 must be without power.
Page 4