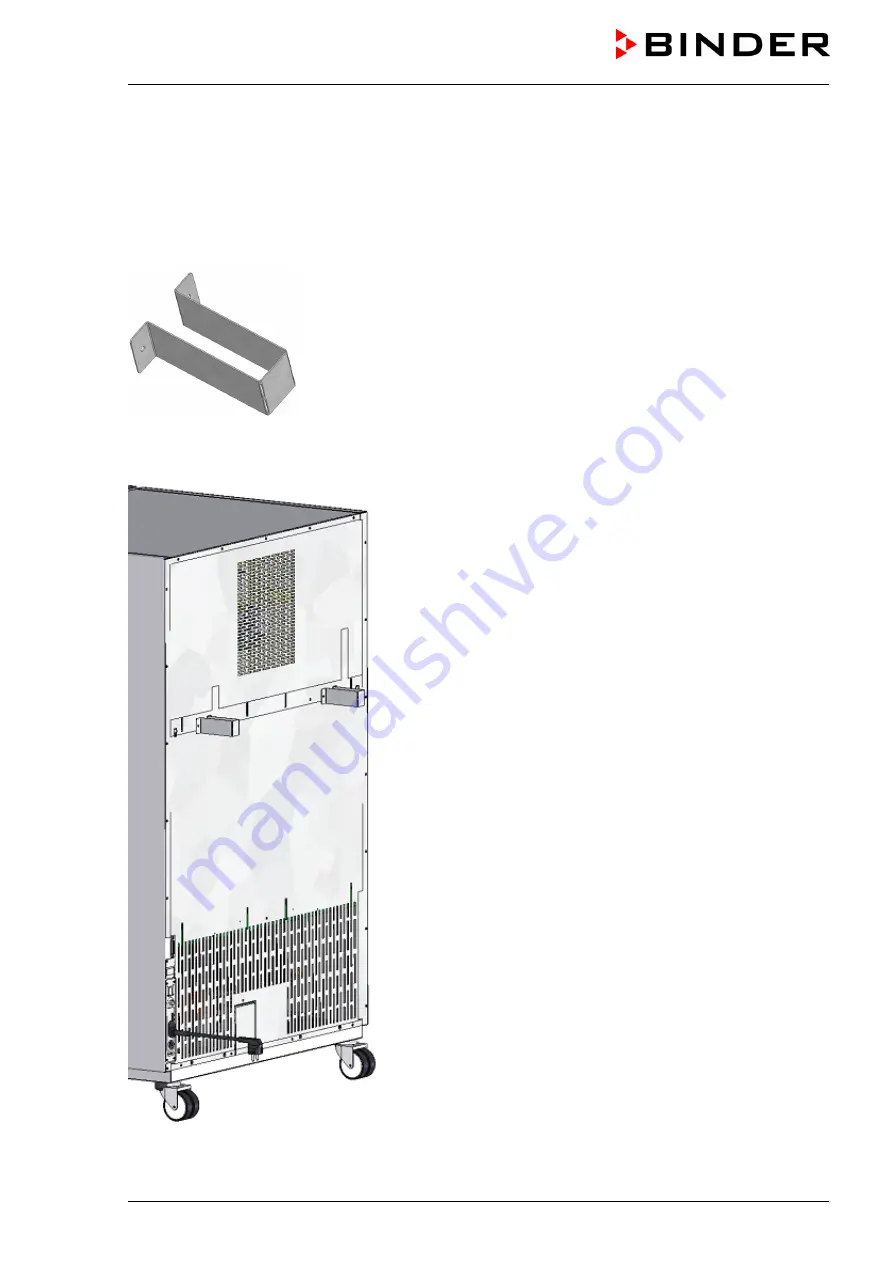
KBF / KBF P (E5.2) 02/2012
page 25/103
4. Installation and connections
4.1 Spacers for rear wall distance
Please fix both spacers with the supplied screws at the unit rear. This serves to ensure the prescribed
minimum distance to the rear wall of 100 mm /
3.94 in
.
Figure 9: Spacer for rear wall distance
Figure 10: Rear KBF / KBF P
with mounted spacers
Summary of Contents for KBF 115 (E5.2)
Page 5: ...KBF KBF P E5 2 02 2012 page 5 103 Product registration ...
Page 98: ...KBF KBF P E5 2 02 2012 page 98 103 19 7 Dimensions KBF 115 ...
Page 99: ...KBF KBF P E5 2 02 2012 page 99 103 19 8 Dimensions KBF 240 KBF P 240 ...
Page 100: ...KBF KBF P E5 2 02 2012 page 100 103 19 9 Dimensions KBF 720 KBF P 720 ...