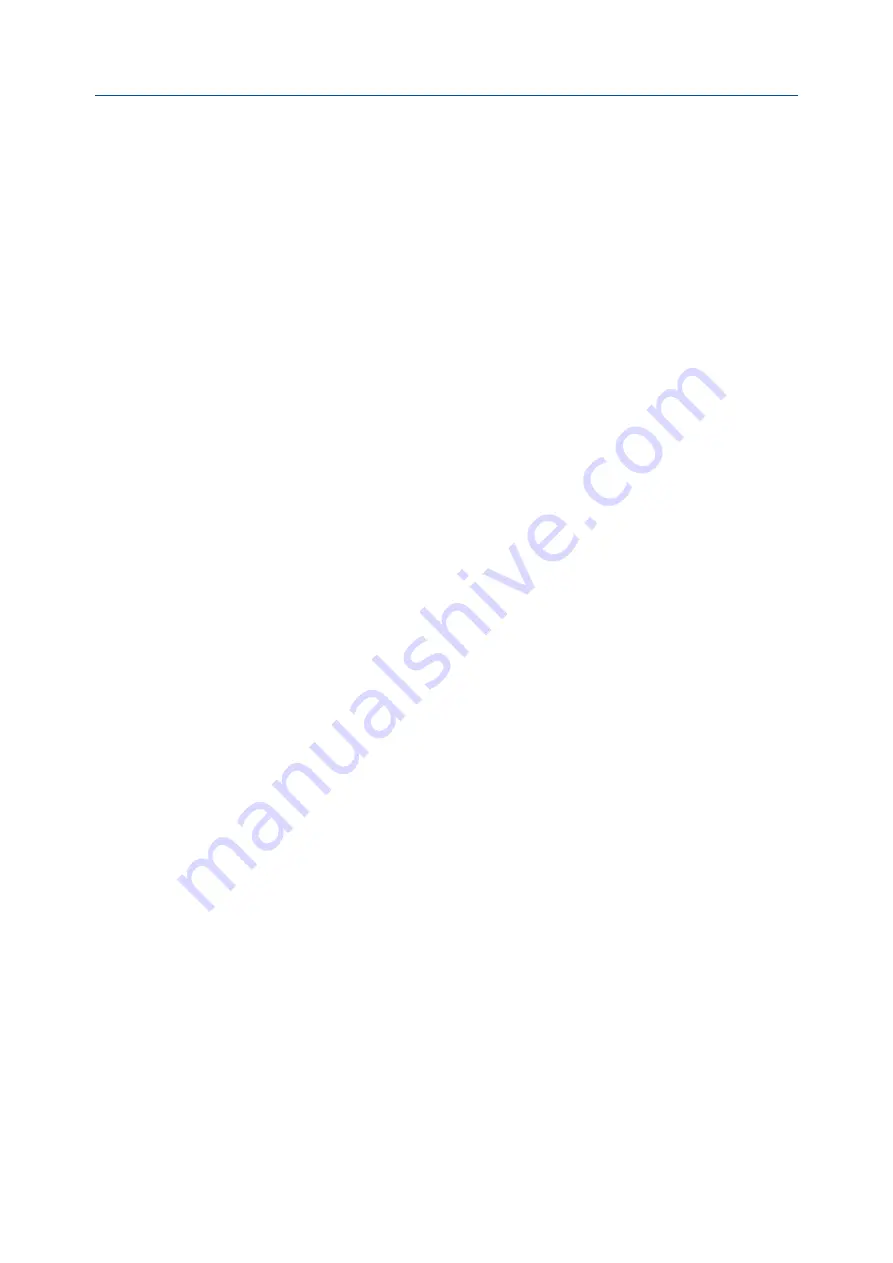
September 2021
Installation, Operation and Maintenance Manual
VCIOM-01249-EN Rev. 0
84
View Routines
Section 10: View Routines
The amount of data to be viewed is large and the local display can only visualize one datum
at a time. To use this function, we suggest to utilize the features available with PDA’s and
PC through Bluetooth™ wireless connection. The figure below shows an example of graph
available on PDA or PC screen, showing the reference opening torque curve and the latest
opening torque curve.
View procedure
•
Move the local selector to OFF and then simultaneously press OPEN and STOP.
Select the language according to the instructions (see “Entering the view mode”).
When the message displayed is “VIEW MODE OK?” press YES. Press NO to scroll
the list of available menus and press YES to select the Maintenance menu.
•
Press NO to scroll the list of routines and press YES to select torque curve.
•
Press NO to scroll the list of available curves (from 1 to 5 and reference). The curve
1 is the latest and the curve 5 is the oldest. Press YES to select.
•
Press YES to select the opening or closing curve. Press NO to exit.
•
Press YES to scroll the list of values. Press NO to exit.
10.4.4
Operation Log
The operation log consists of different counters and routines that provide information
to assist in the maintenance program. The data are grouped into 2 families: general and
recent data. The general data log collects data from “test date” to “present date”. The test
date is set in house, can be viewed in the “nameplate” menu but cannot be changed. The
recent data log collects data from the last “clear recent data log” date to “present date”.
Command “clear recent data log” is available in the SET-UP MENU, Maintenance, Section 7.
This command clears the content of the recent data log and resets the counters to 0. The
old data are lost.
The main differences between “general” and “recent” data log are the following:
•
The general data log gives information relevant to the full life of the actuator,
starting from the manufacturing date.
•
In the recent data log the same data are collected starting from a date set by the
user. The date may be viewed in the MAINTENANCE DATE paragraph.