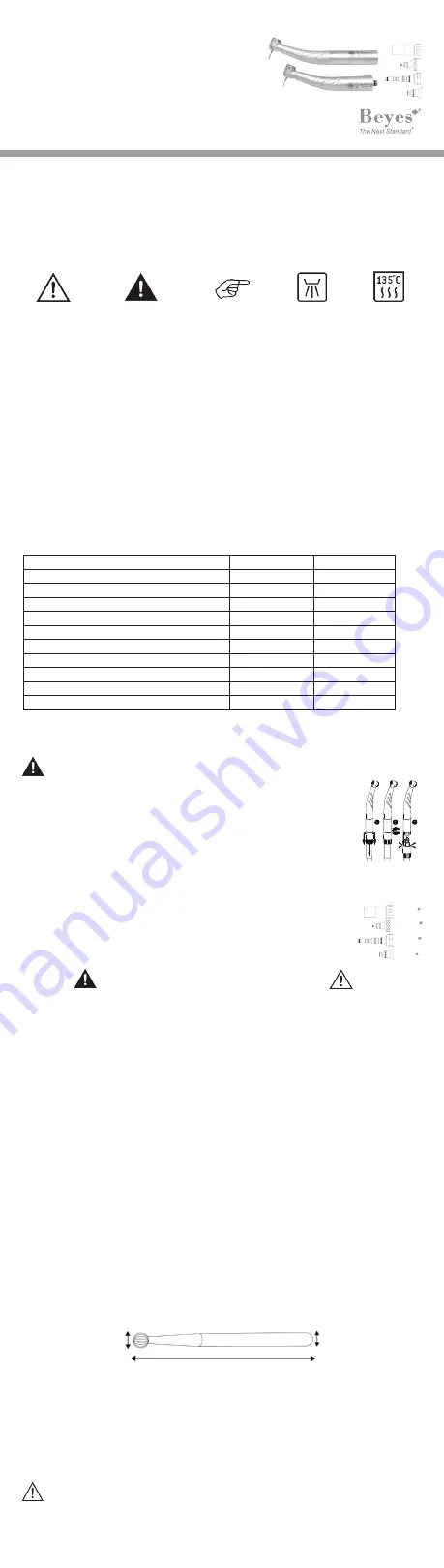
Instructions For Use
X200 High Speed Collection
Table of Contents
• Before You Begin
• Safety Information
• Technical Specifications
• Assembly & Removal
• Friction Grip Bur Specifications
• Bur Insertion & Removal
• Cleaning & Lubrication
• Warranty
WARNING!
(Risk of injury)
ATTENTION!
(To prevent damage)
Thermal washer
disinfectable
General
explanations,
without risk to
persons or objects
Sterilizable
up to the stated
temperature
Technical Specifications
Assembly & Removal
This handpiece should only be used on dental delivery systems that provide filtered
and regulated air and water. Filtration of 25 microns is recommended.
Ez-Swivel PD Coupling
(Fig. 1.1)
1. Ensure PD coupling is firmly attached to the handpiece tubing
2. Align PD coupling into handpiece and push together
3. Ensure handpiece is firmly attached to coupling
4. Pull the retention sleeve of the PD coupling back and remove
the turbine handpiece by pulling in an axial direction
Other Approved Manufacturer’s Couplings
(Fig. 1.2)
Connection: Refer to original manufacturer's instruction for use. (Do NOT use unapproved couplings)
1. Attach the turbine handpiece to the Kavo
®
, NSK
®
, W&H
®
and Star
®
coupling as described by the coupling manufacturer
2. Check that the connection to the coupling is secure.
3. Remove the Kavo
®
, NSK
®
, W&H
®
and Star
®
coupling as described
by the coupling manufacturer.
Before You Begin
Please read this Manual prior to using your Maxso Highspeed Handpiece. The use of this
product is only intended for use by trained dental personnel. We recommend that you
retain this manual for future reference.
Safety Information
• High speed handpieces should be sterilized after each patient to prevent any
transmission of infective organisms.
• Suitable hygienic measures must be taken to prevent cross contamination between
patients, operators and other personnel.
• Only operate this highspeed handpiece when the bur is properly inserted in the chuck.
Do not attempt to extend the length of the bur by improper positioning in the chuck.
Water & Air Adjustment
Coolant Water: Adjust the water volume at the delivery unit to obtain a satisfactory spray mist.
Air Pressure: The operating pressure Must be 2.62 bar to 2.90 bar, and recommendation
is 2.76 bar. It is highly recommended that the operating pressure initially be set using a
handpiece pressure gauge due to the pressure loss caused by the handpiece tubing
material and length.
Warning: Do not exceed 3.52 bar operating pressure as this will shorten turbine life
and may cause additional damage to the handpiece.
Handpiece Operation
Use standard length concentric diamond and carbide burs with 1.59mm nominal diameter
friction grip shanks designed for high speed handpieces.
Use only burs with hardened tempered steel shanks. Before use, verify concentric
rotation by operating handpiece outside the or alcavity in a safe place.
Warning: Do not use burs that produce excessive noise or do not run concentrically. Do
not use burs that are modified, eccentrically designed, or have bent or ‘soft’ (nonheat
treated) shanks.
Friction Grip Bur Specifications
For application details and operating data of the different rotary instruments please refer
to the information provided by the manufacturer.The push button autochuck turbines
have the following bur requirements:
Use only instruments whose shanks comply with the requirements of ISO 1797-1.
• Shank diameter of 1.59—1.60mm
• Overall length up to max. 25mm
• Overall length up to max. 21mm (mini)
• Working diameter up to max. 2.1mm (ISO 021)
Instruments that differ from the specified data must not be used.
Otherwise the mechanism of the clamping system could be damaged.
Fig. 1.2
Kavo
R
NSK
R
W&H
R
Star
R
Rotary instruments
Idle mode speed
Coolant supply volume
Water setting range
Chip air setting range
Return air pressure
Operating pressure
Air consumption
Chip air consumption at 2 bar
Standard Head (S)
350,000-360,000
1.6-0.01
>50
0.7-2
1.5-3
<0.5
30-45
>1.5
>1.5
30-45
0.7-2
1.5-3
<0.5
>50
1.6-0.01
380,000-410,000
2.62-2.90
2.62-2.90
Mini Head (M)
EN ISO 1797-1:1995 (0mm)
(rpm)
(ml/min)
(bar)
(bar)
(bar)
(bar)
(NL/min)
(NL/min)
23
21
Power/Torque
(watt)
Do not assemble/remove during operation!
Fig.2 Bur Specifications
Dia. max. 2.1mm
Dia. 1.59
●
1.60mm
Controler/Racer max.25mm
Mini max. 21mm
Maxso
®
Fig. 1.1