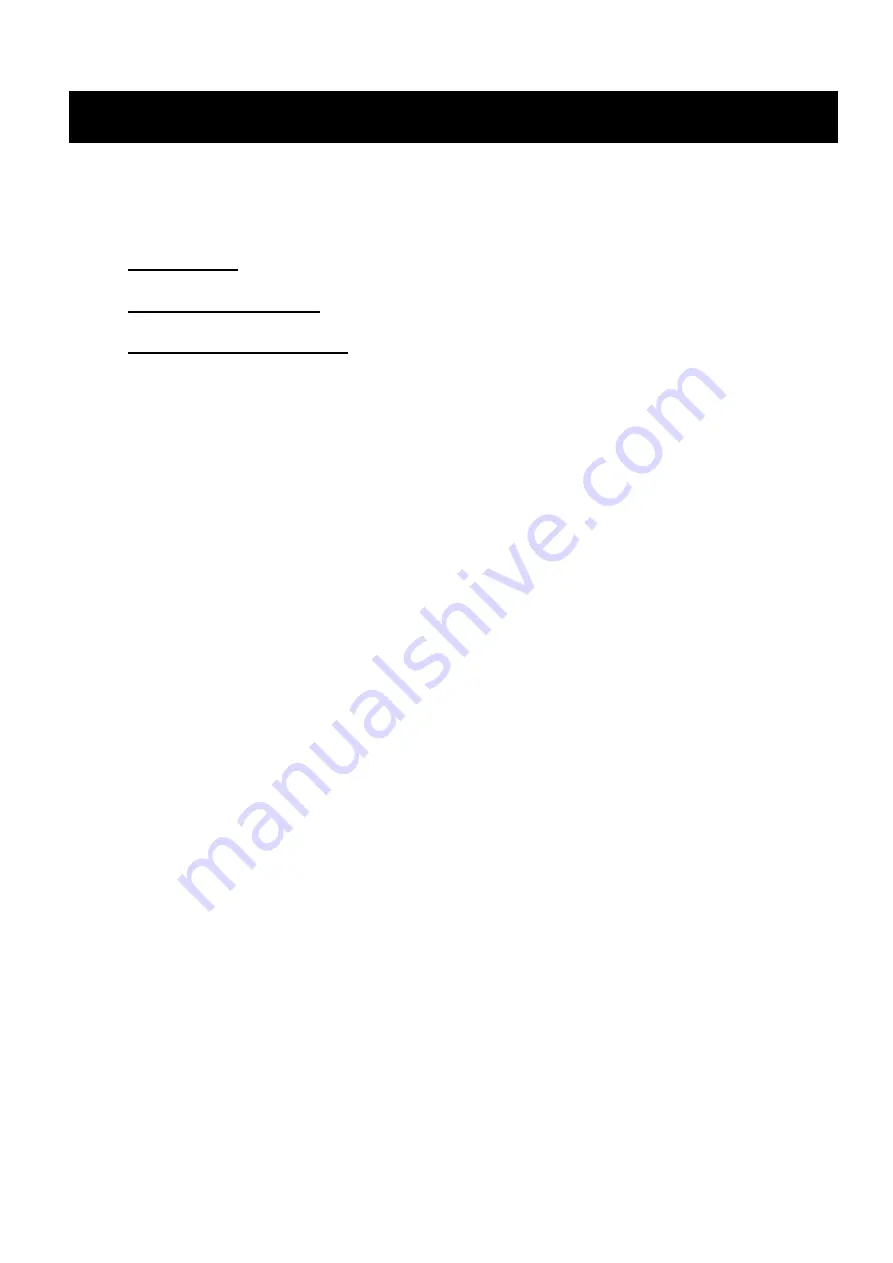
16
5.1 Safety devices
The system in which the pump is installed must always be equipped with the safety
devices described below:
Safety valve
: this is an appropriately calibrated relief valve, which relieves the
excess pressure if a fault occurs in the high-pressure circuit.
Pump shaft protection
: Prevents the operator from accidentally coming into contact
with moving parts of the shaft and transmission.
Pressure regulating valve
: This valve allows the operating pressure to be regulated
and excess fluid to flow back into the tank, thus preventing the pressure from rising
dangerously.
5.2 Fault prevention
5.2 A) Protection against overpressure
This is a displacement pump, so the same amount of water always comes out at each turn
of the shaft. Since the liquids are practically incompressible, if an impurity accidentally clogs
the nozzle and prevents the water from flowing out, the pistons would actually push against
a solid element. Without a protection valve, the pump would be immediately destroyed in
these conditions.
Safety valve.
A good quality safety valve of the right size overcomes these problems.
If, however, during normal use (with a spray gun and washing system for instance),
the water is frequently shut off, it is re-circulated by the relief valve at calibration
pressure, causing overheating and consequently damaging the pump.
Automatic regulating and bypass valve.
An automatic valve reduces this problem since the water is re-circulated at a very low
pressure in this type of valve and takes much longer to heat.
5.2 B) Protection against abrasive particles
No water is free from impurities and abrasive particles, even drinking water.
Not only do abrasive particles rapidly damage the seals, but they also cause the inlet and
delivery valves, the regulating valves and nozzles to wear out very quickly.
A filter
, of an adequate size, installed immediately upstream of the pump guarantees
a long service life to the entire system
However,
remember that the filter must always be
efficient and clean and must
be inspected
even daily.
5.2 C) Protection against cavitation and sizing of the suction circuit (NPSHr)
Cavitation is caused by the formation of gaseous bubbles in the feeding circuit and leads to
wear on the gaskets and erosion of the metal parts of the pump.
The most evident sign of cavitation is a continuous or intermittent hammering sound from
the pump. In addition, the performance, pressure and flow rate often reduce or become
discontinuous.
All liquids tend to form vapor, and this tendency is especially evident when the temperature
rises or when the suction head drops.
During their return stroke, the pistons generate a vacuum which draws water into the
pumping chambers. The greater the resistance the water opposes along the route from the
5- SAFETY AND FAULT PREVENTION DEVICES
Summary of Contents for 74.1030.97.3
Page 39: ...39...
Page 40: ...40 PART No 74 0066 99 2 REV 00...