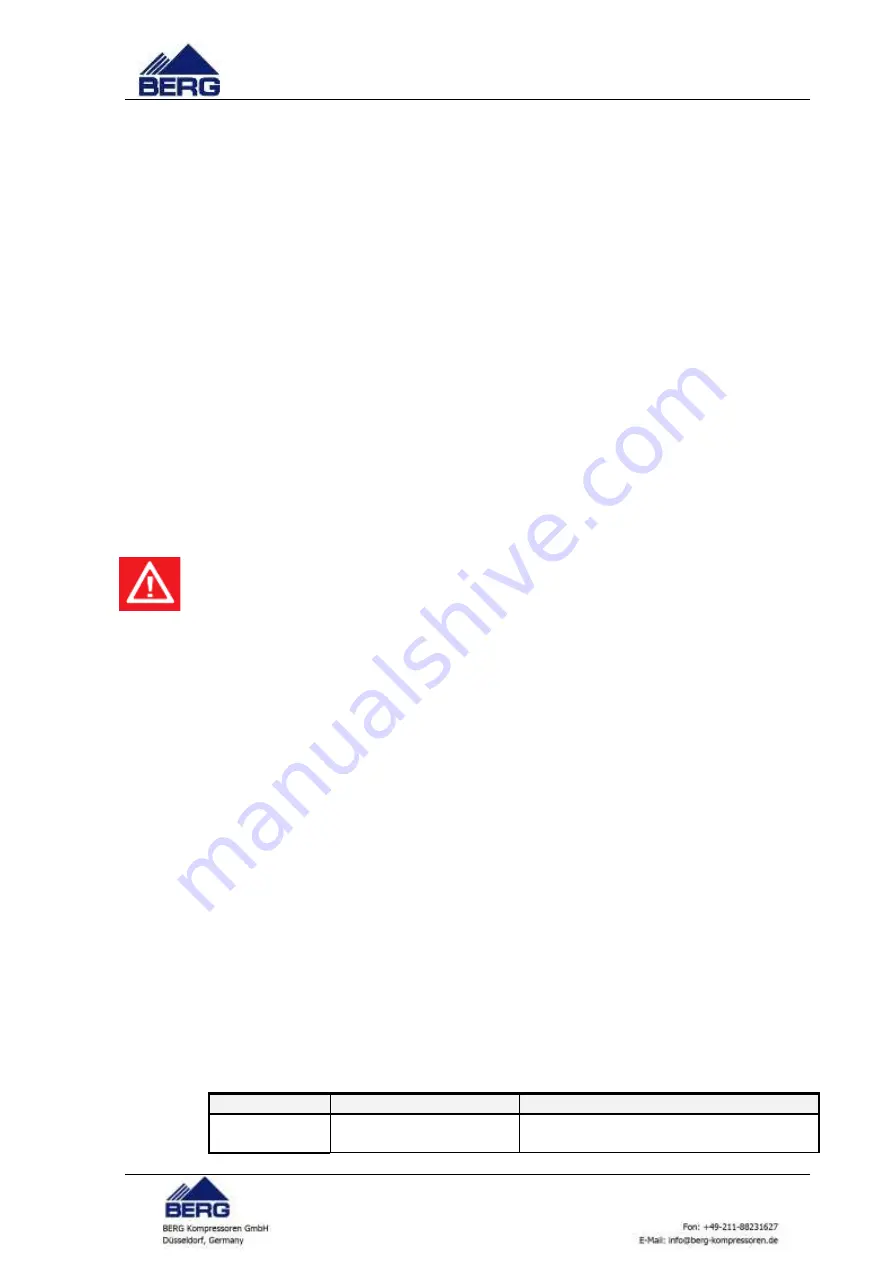
valve mechanism, and consequently damage the entire pressure unit. Therefore, during the
equipment operation particular attention should be paid to the following:
-
Correct setting of the safety valve, appropriate to the operating parameters of the equipment
being protected,
-
Appropriate protection of the valve mechanism against unauthorized adjustment and a risk of
damage. The valve seal must be intact,
-
Periodic inspections of the valve for correct operation according to the requirements of the office
of technical inspection regulations.
The safety valve operation inspection involves blowing the valve by pulling the handle (wheel)
upwards. The pin, lifted by pulling the wheel up, releases the pressure of the valve spring and
moves the head a little up and allows the compressed air to flow through the valve.
The handle can be loosened at the pressure equal at least 50% of the operating pressure.
The valves delivered require no special maintenance. They should only be periodically (every
1000 hours) blown by pulling the handle of the push pin. Special care must be taken while
performing this operation. Keep away from the stream of air blown out (caution
–
the air may be
hot!).
In case of the valve leaks, contact the manufacturer service to arrange its repair. The valve
cannot be repaired by the user itself.
Blocking the pin, tightening the adjustment nut or covering the valve outlets is not allowed.
In addition to the guidelines and requirements listed in this paragraph, the user is obliged to
observe the regulations being in force in the country in which the equipment is operated.
The safety valves are intended only for protection of: pressure tanks, conduits for
compressed air or other neutral gases, sources of compressed air from overpressure
(above the limit for that type of equipment).
The safety valves may not be used as relief valves for pressure adjustment.
8. Troubleshooting
Symptom
Cause
Remedy
the compressor
will not start
power failure
check for supply voltage in the power supply
terminals