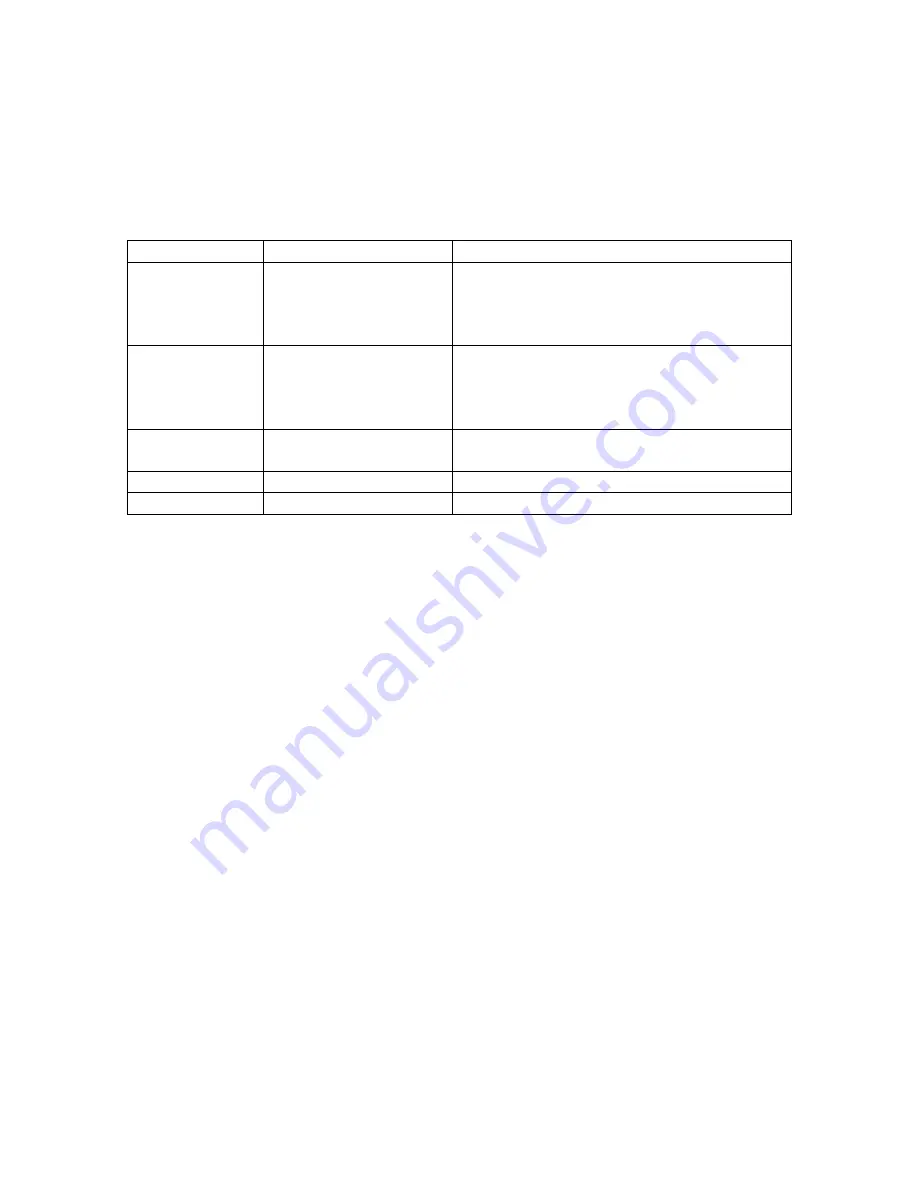
Selkirk College IATPL Program Manual
Beech 95 POH
Effective September 1, 2005
Appendix 14 - 18
Airspeed Indicator Markings
Airspeed indicator markings and their color code significance are shown below.
Note that all speeds are
calibrated
speeds, even though they are painted on the airspeed
indicator.
Marking
KCAS value of range
Significance
White Arc
61 - 113
Full Flap Operating Range: Lower limit is
maximum weight Vso, in landing
configuration. Upper limit is maximum
speed with flaps extended.
Green Arc
71 - 161
Normal Operating Range: Lower limit is
maximum weight Vs at most forward CG.
Upper limit is maximum structural cruising
speed.
Yellow Arc
161 - 208
Operations must be conducted with caution
and only in smooth air.
Red Line
208
Maximum speed for all operations
Blue Line
94
Vyse at maximum weight and sea level.
Power Plant Limitations
Engine Manufacturer: Avco Lycoming
Engine Model: IO-360-B1B
Maximum rated Power: 180 BHP @ 2700 rpm for all operations
Engine Operating Limits for Takeoff and Continuous Operations:
Maximum engine speed: 2700 rpm
Maximum engine pressure: 29 inches of mercury
Fuel Grade: See fuel limitations
Oil Grade (Specifications):
................................................................................. MIL-L-6082
................................................................................. MIL-L-2285
............................................................................... MIL-L-22851
Propeller Manufacturer: Hartzell
Propeller Model Number: HC-92WK-2B
Propeller Pitch settings: 84.0 high - 14.0 low
Propeller Diameter: 71 to 72 inches
An operating manual supplement was issued on February 28, 1975 which specifies that
more than 23” Manifold Pressure may not be used below 2300 rpm.
Summary of Contents for Beech 95 2017
Page 2: ...Selkirk College IATPL Program Manual Beech 95 POH Effective September 1 2005 Appendix 14 2 ...
Page 3: ...Selkirk College IATPL Program Manual Beech 95 POH Effective September 1 2005 Appendix 14 3 ...
Page 43: ...Selkirk College IATPL Program Manual Beech 95 POH Effective September 1 2005 Appendix 14 43 ...
Page 51: ...Selkirk College IATPL Program Manual Beech 95 POH Effective September 1 2005 Appendix 14 51 ...
Page 80: ...Selkirk College IATPL Program Manual Beech 95 POH Effective September 1 2005 Appendix 14 80 ...
Page 81: ...Selkirk College IATPL Program Manual Beech 95 POH Effective September 1 2005 Appendix 14 81 ...