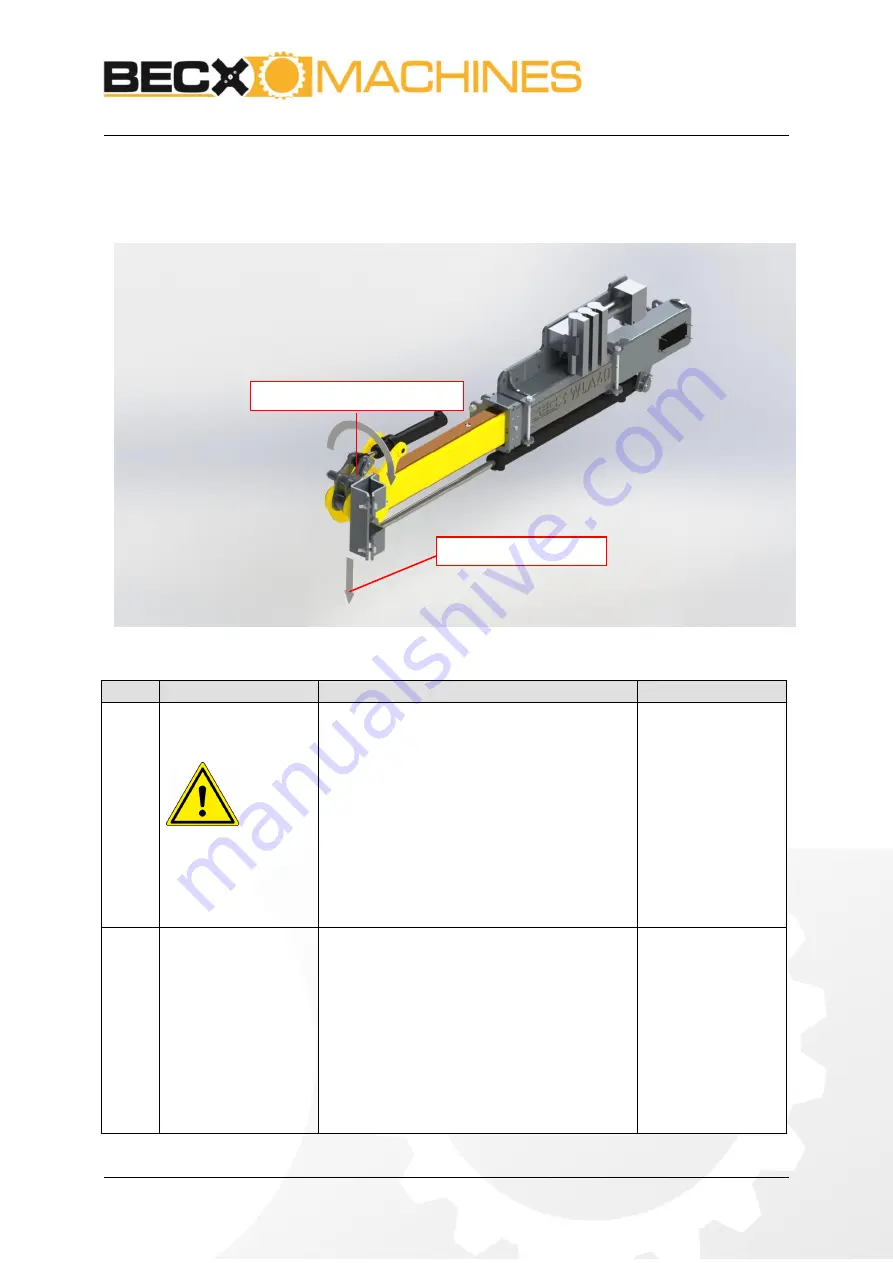
Loader arm
Type: WLA60
Version: 1
July 2019
Page 15 van 23
5.
Operations
5.1.
Assembly and adjustment of the loader arm
Figure 7: maximum forces arm and tool
No.
What to do
Action
Result
1
Select the correct tool
carrier and lifting arm
Make sure that the tool carrier and lifting
arm are sufficiently strong and stable for
the weed brush (see chapter 1: Technical
data for the load when lifting and the
exerted moment of the lifting).
Make sure that the maximum pressure
and number of revolutions (oil flow) are
not exceeded.
Make sure that the correct rapid
attachment connections are installed.
Make sure that the correct clasp is used.
Ignoring the stated
values can result in
damage to
equipment and
injury to persons.
2
Connect the loader
arm to the loader
mechanically
Make sure the base is vertical
Connect the adapter plate (Figure
3:3) with at least 4 of the provided 12
connection holes to the loader.
Place the base (Figure 3:6) on the
desired position on the adapter plate.
Depending on the preference of the
user, it can be mounted on different
positions.
Lock the base properly
Moment tool
Vertical force tool