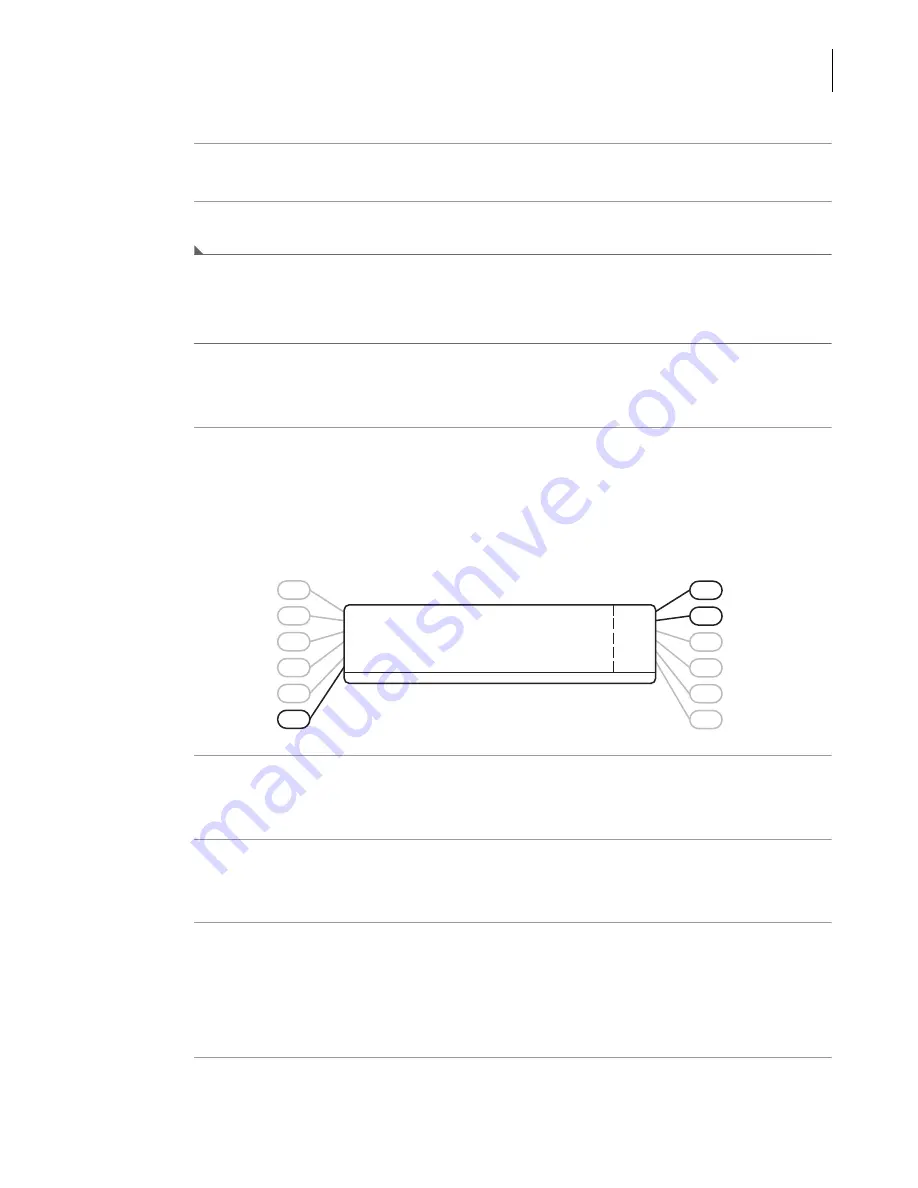
PN B10093AE
2-15
Operation
Programmed Operation
2
7
Press the
SAVE
soft key when programming is complete.
8
Press the
EXIT
soft key to exit program mode.
Modifying a Program
1
Press the
OPT
key.
The
Prog Recall:
field flashes, and the message “
Enter program number (1–30)
” appears.
2
Press
OPT
again to move the cursor to the
Setup:
field.
a.
Enter the number of the program to be modified.
•
The program number appears in the
Setup:
field.
•
A message appears asking if you want to overwrite the program.
•
YES
and
NO
soft keys appear.
3
Press the
YES
soft key.
The step 1 parameters appear.
4
To see step 2 parameters, press the
STEP2
soft key.
The step 2 parameters appear.
5
Modify the parameters for either step.
a.
Press
ENTER
when done.
b.
Repeat for the other step, if required.
The newly entered parameters appear.
6
Press the
SAVE
soft key to save both program steps.
SPEED
TIME
TEMP
A/D
OPT
ROTOR
Accel : MAX Decel : MAX
Prog Recall: - - Setup: 1 Step #
YES
NO
Rotor : JA-30.50
Speed : 0 RPM = x G
Time : 00:00
Temp : 25°C Max Temp : 29°C Shutdown? No
Program number used, overwrite Y/N?
Summary of Contents for Avanti J-26S XPI
Page 4: ...PN B10093AE iv Revision History ...
Page 12: ...xii Contents Avanti J Series Centrifuge Warranty Related Documents ...
Page 14: ...xiv Illustrations ...
Page 16: ...xvi Tables ...
Page 20: ...PN B10093AE xx Introduction Multi Compliance Label ...
Page 36: ...PN B10093AE 1 16 Description Available Rotors ...
Page 66: ...PN B10093AE 3 10 Troubleshooting JCF Z Rotor Identification ...
Page 82: ...PN B10093AE A 10 Preinstallation Requirements Using J2 Series Rotors in the Avanti J 26S XPI ...
Page 86: ...PN B10093AE Warranty 2 Beckman Coulter Inc Avanti J Series Centrifuge Warranty ...
Page 87: ......