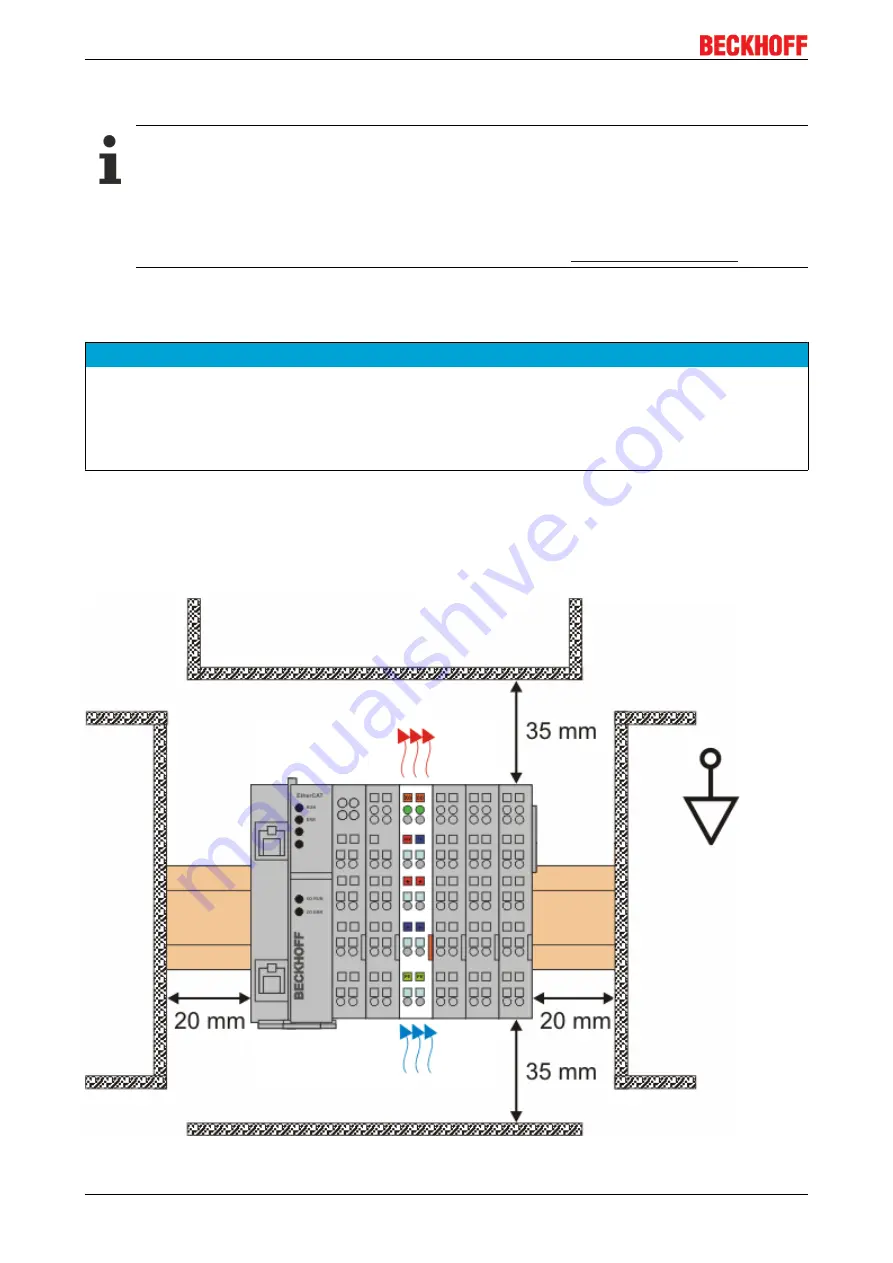
Mounting and wiring
EL1052, EL1054
36
Version: 1.1
4.8
ATEX Documentation
Notes about operation of the Beckhoff terminal systems in potentially explosive ar-
eas (ATEX)
Pay also attention to the continuative documentation
Notes about operation of the Beckhoff terminal systems in potentially explosive areas (ATEX)
that is available in the download area of the Beckhoff homepage
!
4.9
Installation positions
NOTE
Constraints regarding installation position and operating temperature range
Please refer to the technical data for a terminal to ascertain whether any restrictions regarding the installa-
tion position and/or the operating temperature range have been specified. When installing high power dissi-
pation terminals ensure that an adequate spacing is maintained between other components above and be-
low the terminal in order to guarantee adequate ventilation!
Optimum installation position (standard)
The optimum installation position requires the mounting rail to be installed horizontally and the connection
surfaces of the EL/KL terminals to face forward (see Fig.
“Recommended distances for standard installation
position”
). The terminals are ventilated from below, which enables optimum cooling of the electronics through
convection. "From below" is relative to the acceleration of gravity.
Fig. 27:
Recommended distances for standard installation position
Summary of Contents for EL1052
Page 2: ......