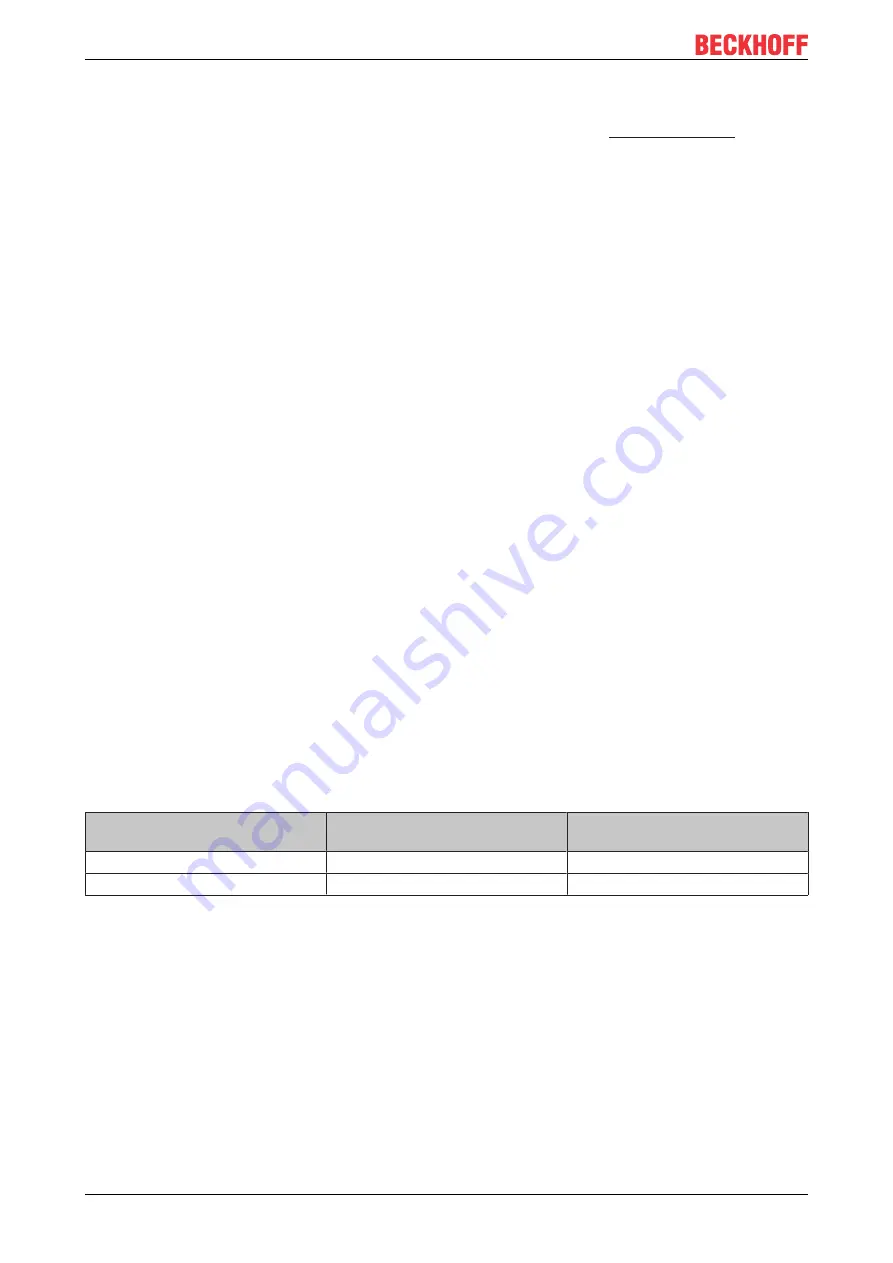
Technical description
Synchronous servomotor
16
Version: 2.1
Axial force
Axial forces arise when assembling pinions or pulleys on the shaft and using angular gearheads, for
example. Please use the force calculation program available from our website (
calculation of the axial Forces.
Coupling
Double-coned collets, possibly in association with metal bellows couplings, have proven themselves as
excellent, zero backlash coupling elements.
6.3.3
Flange
Flange dimensions according to IEC standard, fit j6 (h7 at AM811x), accuracy according to DIN 42955
Tolerance class:
N
6.3.4
Shaft
Cylindrical shaft according to DIN 748 part 3, centering bore with thread (DIN 332 part 2) for motors of the
series AM812x, AM813x and AM814x.
6.3.5
Protection class (EN 60034-5)
Standard version - housing
IP65 (IP54 = AM811x)
Standard version - shaft feedthrough
IP54
Shaft feedthrough with shaft sealing ring
IP65
6.3.6
Insulation material class
The motors conform to insulation material class F according to IEC 60085 (UL 1446 class F).
6.3.7
Vibration class
The motors are made to vibration class A according to DIN EN 60034-14. For a speed range of 600-3600
rpm and a shaft centre height between 54 - 97 mm, this means that the actual value of the permitted
vibration severity is 1.6 mm/s.
Speed [rpm]
Max. rel. vibration displacement
[µm]
Max. run-out [µm]
<= 1800
90
23
> 1800
65
16
6.3.8
Vibrations and shocks
OCT and Multiturn:
Vibration according to EN 60068-2-6 50 g / 10…2000 Hz
Shocks according to EN 60068-2-27 100 g / 6 ms
6.3.9
Connection technology
The motors are fitted with rotatable, angular connectors for the power supply and the feedback signals (only
resolver).
The mating connectors are not included in the scope of supply. We can supply preassembled feedback (only
resolver) and power cables.