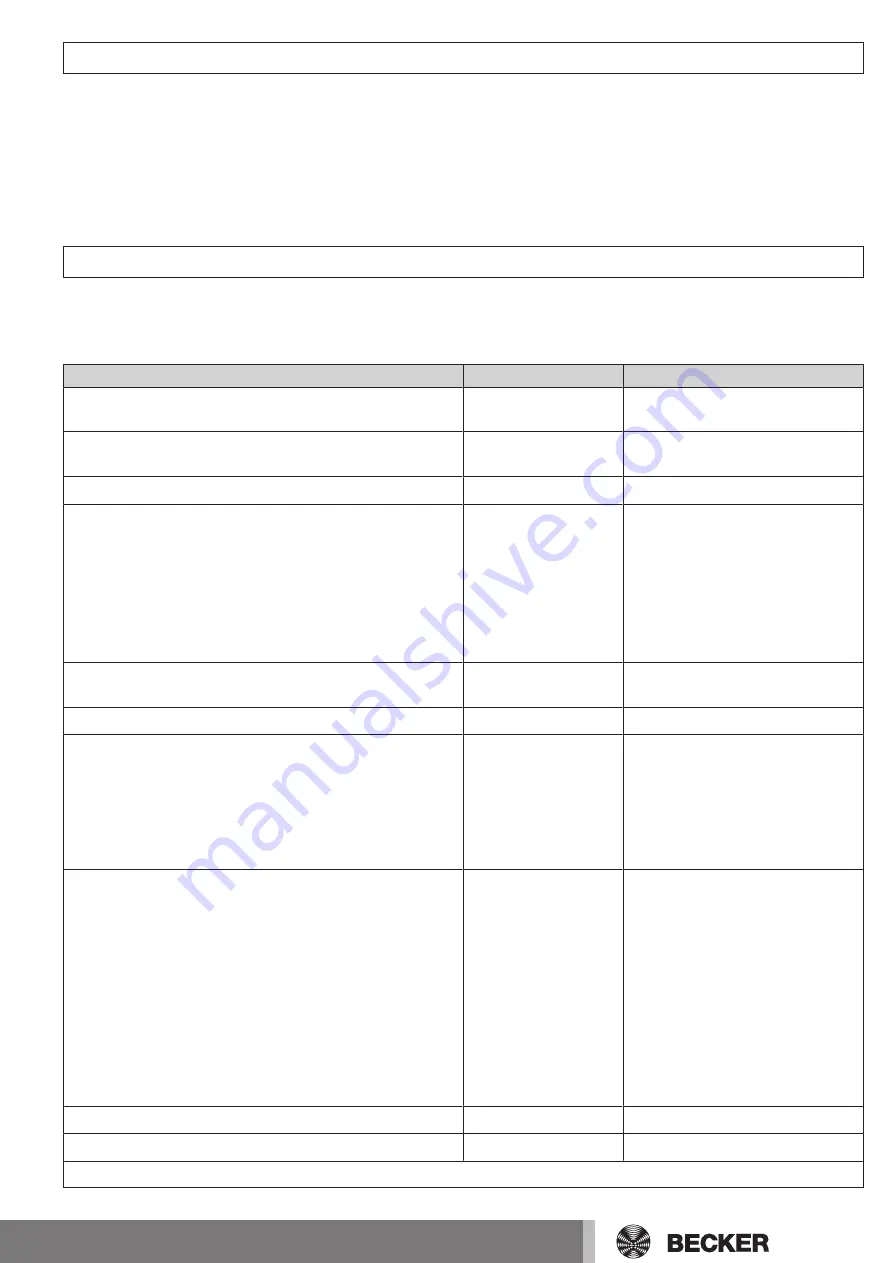
Positioning system
The control unit can be used for both mechanical limit switches (
P.991:0; P.991:1
) and absolute value encoders (
P.991:2
).
Various parameters are preset when setting the profile. Note that there are different parameters and different connecting dia-
grams for mechanical limit switches and absolute value encoders. It is also possible to set company-specific door profiles.
The positioning systems are identified in the text as follows:
MLS
: Mechanical limit switch
AE
: Absolute value encoder
The absolute value encoders must meet Performance Level “c” in combination with the control unit. Becker-Antriebe GmbH drives
with a Kostal single-turn absolute value encoder meet these requirements.
Initial operation
After switching on the control unit for the first time, or after choosing to "Restore factory setting", parameters are automatically
called up. You must set the parameters as applicable and then leave the parameterisation mode.
Below, the steps are described for the automatic call-up of parameters and how you can then set the limit positions (the control
unit must be fully connected).
Step
Display
Description
1.
Connect the control unit to the power supply.
bdcI
The abbreviation for the control unit
software.
2.
"bdcl" appears on the display, and after a short time "P.991"
is displayed.
P.991
Prompt for the selection of the door
profile.
3.
Briefly press the rotary-push button (DDT).
-
Jump to the parameter.
4.
Turn the rotary-push button (DDT) to the desired profile:
- 0: mechanical limit switching
- 1: mechanical limit switching
- 2: Absolute value encoder
Save the value by pressing and holding the rotary-push button
(DDT). "PrOG" appears on the display for several seconds once
the profile has been saved.
-
The door profile is activated. (see
Door profiles [
32]).
5.
Determine the type of safety edge.
P.4E0
Prompt for the type of safety edge
(see Function inputs FE).
6.
Briefly press the rotary-push button (DDT).
-
Jump to the parameter.
7.
Turn the rotary-push button (DDT) until the value for the de-
sired type of safety edge appears on the display.
- 1: electric safety edge
- 2: Optoelectronic safety edge OSE
Save the value by pressing and holding the rotary-push button
(DDT).
1..2
The safety edge is activated.
8.
Turn the rotary-push button (DDT) to the desired profile.
- 1.00: Electric safety edge 8.2 kΩ
- 1.01: Electric safety edge 1.2 kΩ
- 1.02: Pressure-wave safety edge, 8.2 kΩ
- 1.03: Pressure-wave safety edge, 1.2 kΩ
- 1.04: PNP with testing
- 1.05: NPN with testing
- 2.00: Optoelectronic safety edge OSE
Save the value by pressing and holding the rotary-push button
(DDT).
-
Safety edge profile is activated.
9.
Briefly press the rotary-push button (DDT).
P.4E1
The prompts are concluded.
10.
Press and hold the rotary-push button (DDT).
The parameterisation mode is exited.
The limit positions can be set as described in the chapter "Setting the door limit positions".
15