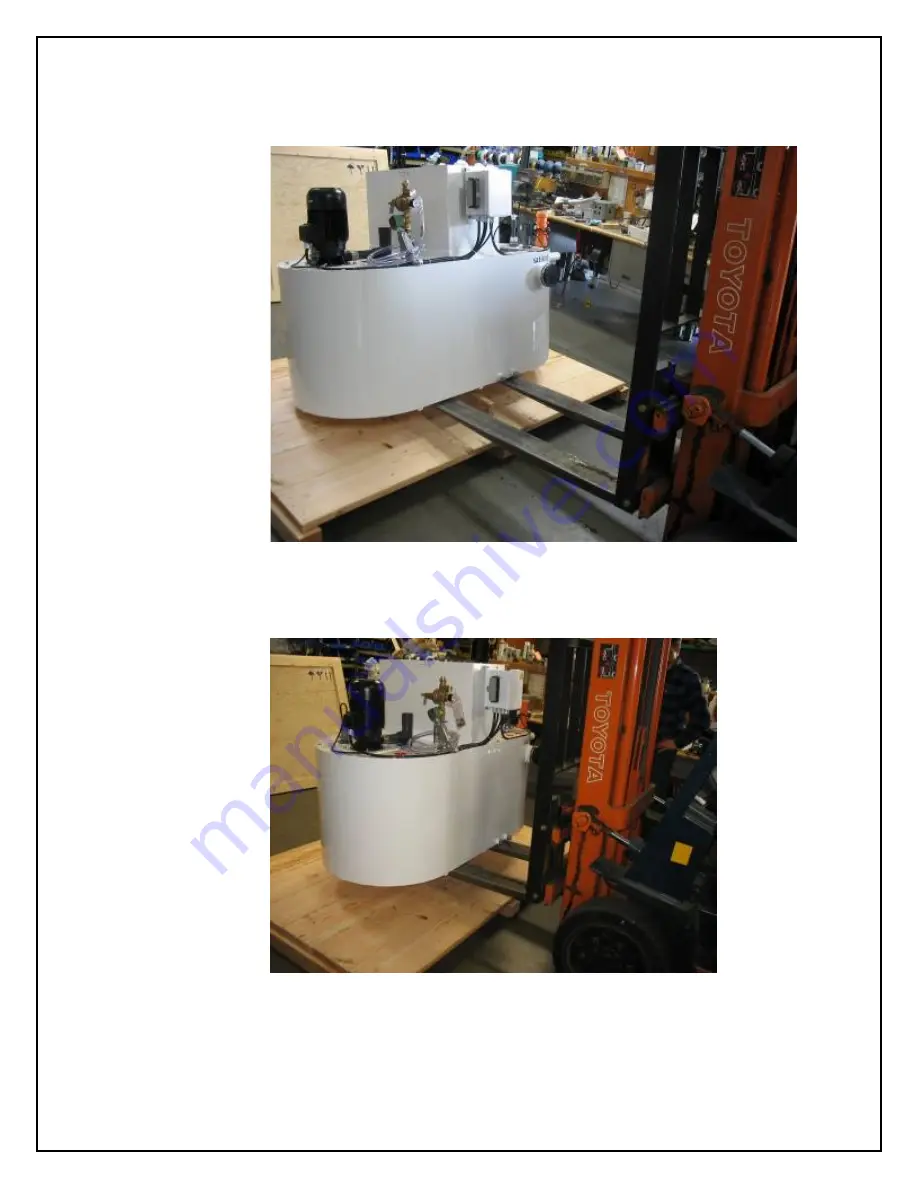
Microseparator™ Coolant Systems Transport, Installation, & Initial Startup
M000005_A - V Twin Ultra Transport & Installation 5.2-EN TM
19/78
Lifting the Main Tank Assembly
Figure 8 - Lifting Main Tank Assy
After removing the surrounding crating material and packaging, lift the
tank assembly as shown. Block with wood to allow the forklift tangs to
pass fully under the tank assembly.
Figure 9 - Lifting Main Tank Assy
Lift the entire assembly and transport to the installation point.