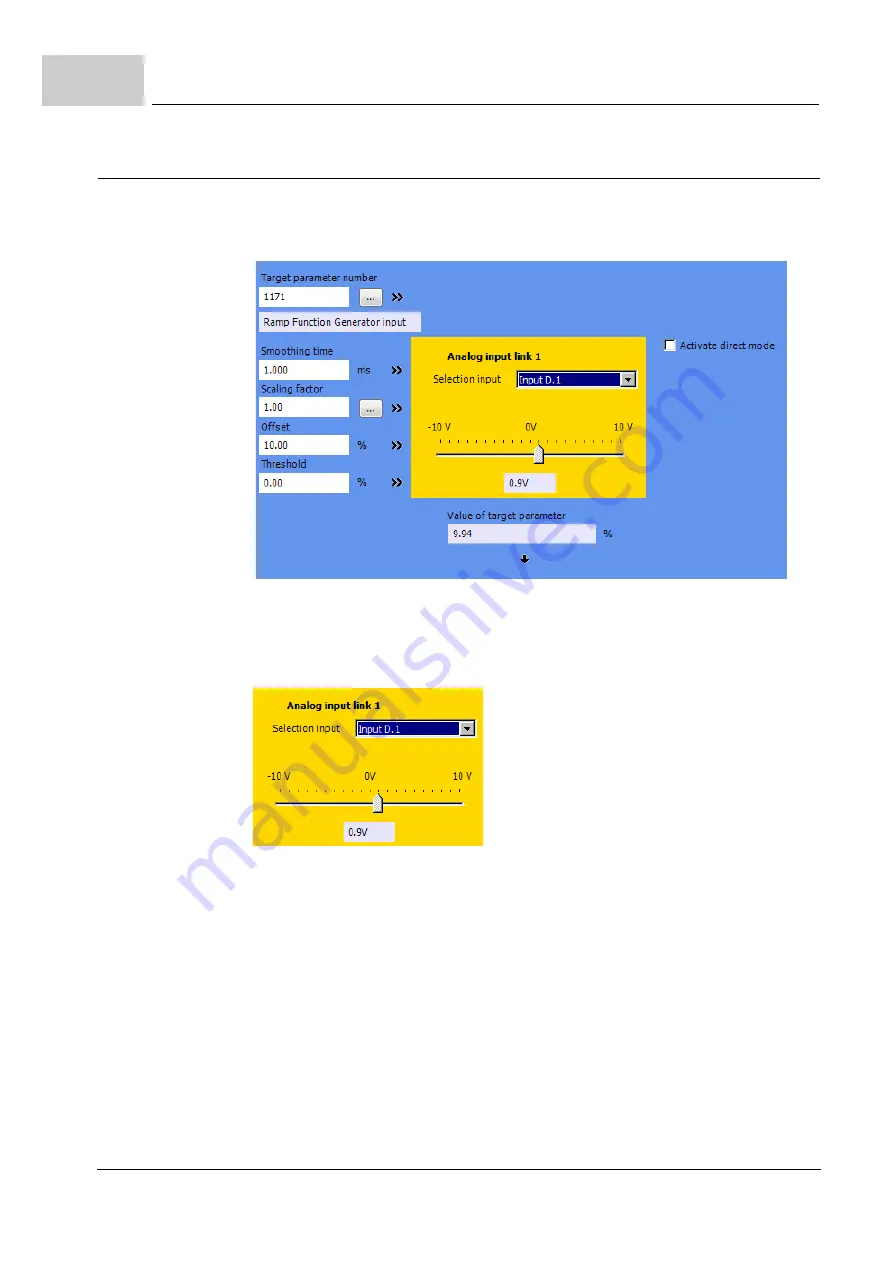
Procedure of the commissioning
Instruction handbook
b maXX
(BM4-F-)AIO-XX (Analog IO module)
Document No.: 5.01045.08
Baumüller Nürnberg GmbH
50
8.2
8.2.2.1 Testing of inputs AIO-01, -02 and -03
1
ProDrive Navigation „IO analog inputs“.
2
Select „Analog input link 1“ in ProDrive.
Figure 15:
Analog input link 1, AIO-01, -02 and -03
3
By clicking on the
g
-symbol, select the entry „Input D.1“ („D“
⇒
module in position D,
„1“
⇒
input 1) from the drop-down list.
Figure 16:
Input selection AIO-01, -02 and -03
4
Enter in menu „analog input link 1“:
m
Target parameter number
: „1171“, (ramp function generator input)
m
Smoothing time
: „10 ms“,
m
Scaling factor
: „1“,
m
Offset
: „0“,
m
Threshold
: „0“,
A scale is displayed and shows the applied voltage (set by the potentiometer), e. g. +10 V.
Summary of Contents for AIO Series
Page 83: ......