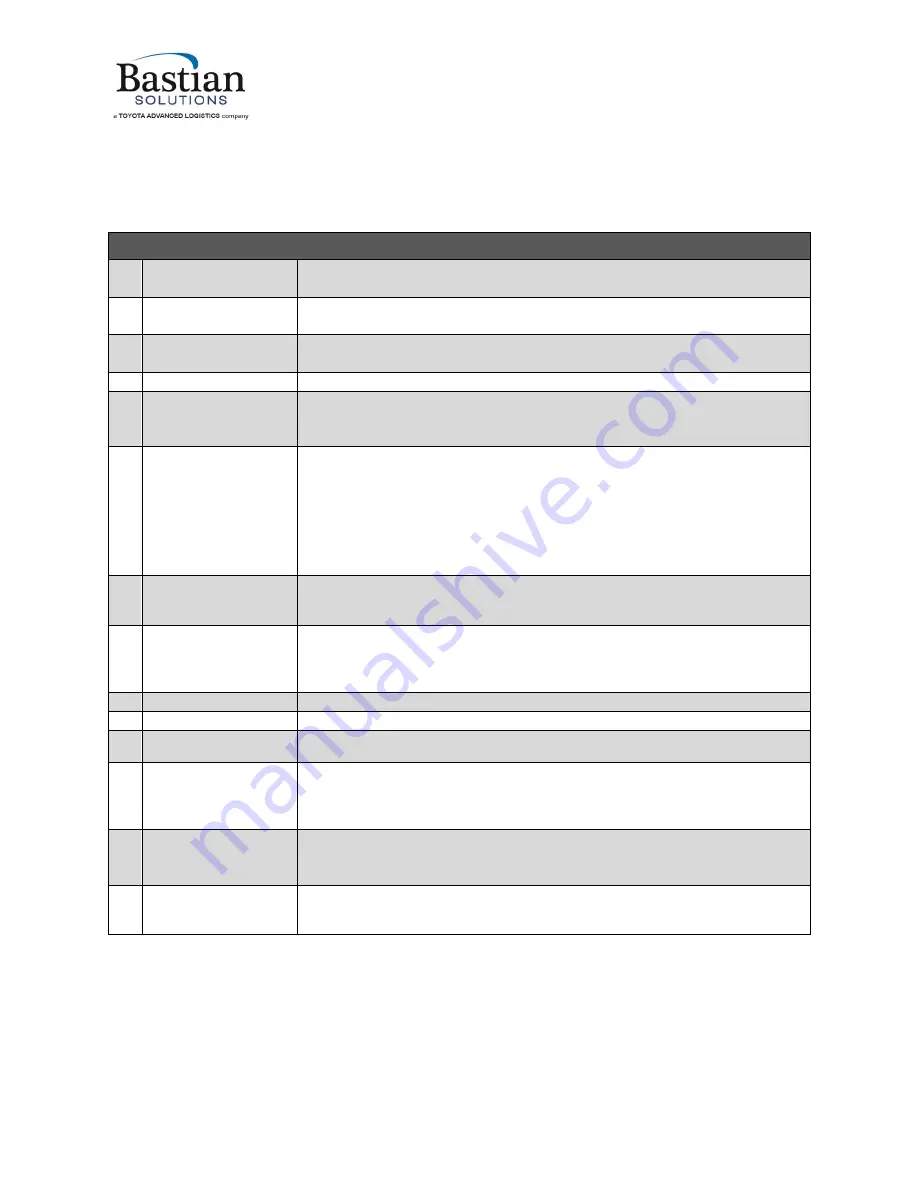
Installation and Maintenance Manual: Shoe Sorter
_____________________________________________________________________________________________
Installation and Mai ntenance Manual: Shoe Sorter
Published October 2019
Rev.A1
42
7.4
Recommended Preventative Maintenance Schedule
Table 3-Recommended Preventative Maintenance Schedule
✓
INTERVAL
DESCRIPTION OF CHECK
Before each startup
Make sure the conveyor is clear of foreign objects and all personnel are safely
away from moving parts.
Once per shift
Visual and auditory inspection to check for oil leakages, hardware security, or any
unusual noise that may indicate there is a problem with the equipment.
Daily
Inspect all the photoeyes and proximity switches to make sure they are secure
and properly aligned.
Weekly
Check for product build-up around and on slats. Clean if necessary.
Weekly
Visually inspect the slats for damage, unseated spring clips, excessive
spillage/residue or other problems (additional inspections as needed based on
maintenance history).
Weekly
Refill the oiler (as needed) and monitor for correct oil consumption.
1.
Ensure the oiler is dispensing oil at regular intervals (if the rate of usage
drops significantly, it may indicate a clog or obstruction) and refill when
necessary.
2.
Refill with SAE 30 mineral oil or SAE 85W gear oil (ISO 100), for operation
between 40°F and 100°F.
a.
Consult ZiPline for operation at temperatures outside these limits.
Monthly or 300 hours
Clean the pin sensor windows in the divert switches. (Additional cleaning to be
performed as needed if sensor faults are recorded.)
Monthly or 300 hours
Verify free movement of the divert switch gate, verify the lead-ins and switch
gate are undamaged, and clean out any accumulated debris or dirt in and around
the switch gate mechanism and sliding surfaces.
Monthly or 300 hours
Clean the surfaces of all slats to allow free motion of shoes.
Monthly or 300 hours
Check for loose bolts, nuts, fittings, and sensors. Tighten if necessary.
Monthly or 300 hours
Remove any accumulated debris on the gearbox or motor housing.
Monthly or 300 hours
Check the proper functioning of all proximity switches and photoeyes. Secure all
mounting brackets, clean the lenses and reflectors, and replace any that are
defective.
After first 24 hours,
and every 2 months or
500 hours thereafter
Check torque of all set screws (see ABB Instruction Manual for DODGE® Bearings
for appropriate torque values).
3 months or 1,000
hours
Regrease all bearings with No. 2 lithium complex base grease (see ABB
Instruction Manual for DODGE® Bearings for detailed lubrication instructions).