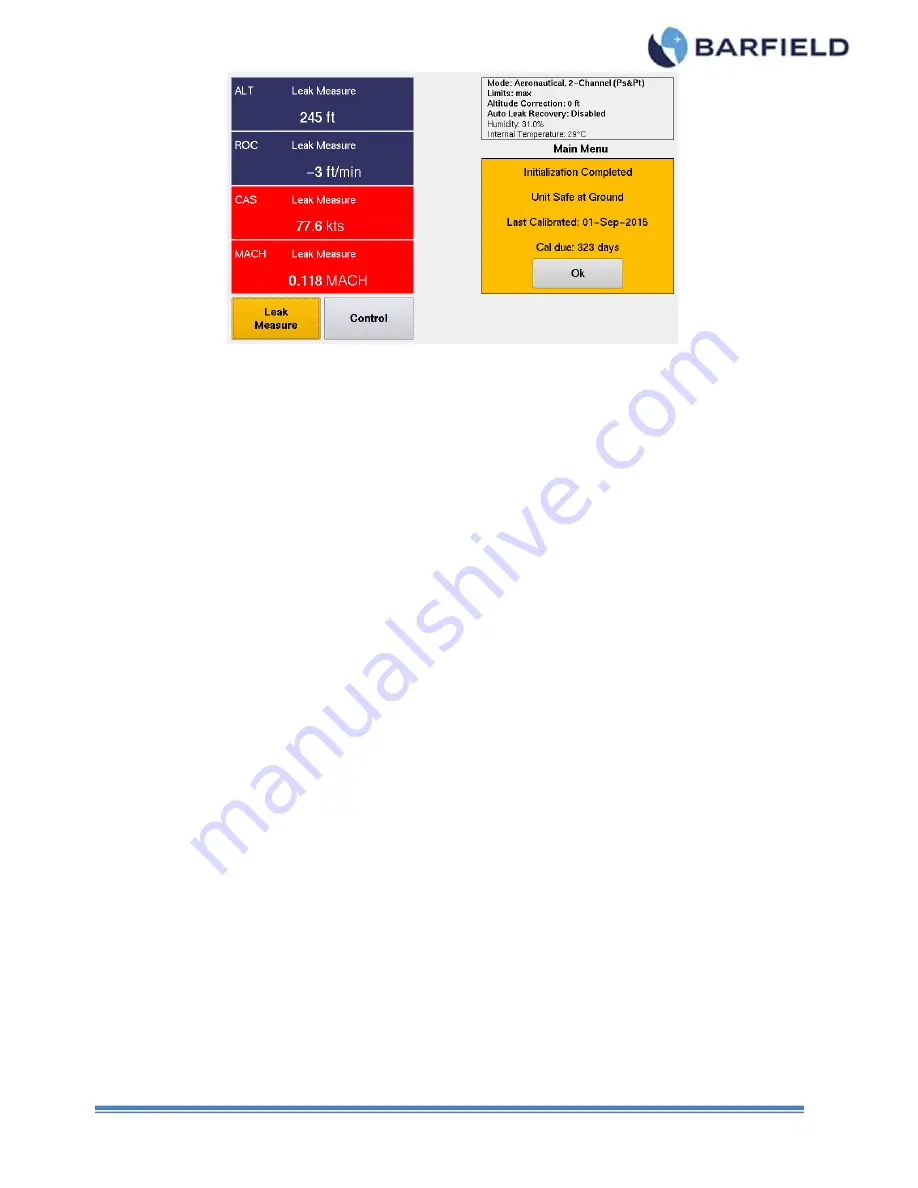
56-101-01175 Revision P Page | 44
Figure 49
Initialization Display
C.
Leak Measure Mode
The Test Set has two modes of operation, (1) Leak Measure and (2) Control. The default
mode of operation for the Test Set is Leak Measure mode. At the conclusion of power ON
initialization the Test Set will be placed in the Leak Measure mode.
While in Leak Measure mode the Test Set is continuously measuring / monitoring the
pressure on both the Static (Ps) and Pitot (Pt) ports. The display will be continuously
updated (~ 2 times/second) with the latest pressure measurement results. In Leak
Measure mode, the pneumatic pressure pump, vacuum pump and four proportional
control values (PvPs_V, PvPs_P, PvPt_V, PvPt_P, refer to
) are off.
When the Display Setup is configured for Aeronautical mode, the Test Set has some
additional features and safeguards such as ALR and Leak Test ATP.
While in Leak Measure mode, the ALR “Auto Leak Recover” (if enabled) monitors the leak
rate of ROC and RtCAS. If the rates exceed the values defined under the Limits menu
(Example: with Limits = default, ALR for ROC = 1,000 ft/min and RtCAS = 25 kts/min) the
Test Set will automatically switch into Control mode with the Target values set to the
current ALT and CAS values and the Test Set pneumatic controller will try to overcome
the leak and stabilize the pressures on the Static (Ps) and Pitot (Pt) ports. When this
occurs, the following message will be displayed,
“Excessive Leak Detected.”
The Leak Test ATP profiles are only available when the Display Setup is configured for
Aeronautical display mode. When the user selects Pressure or EPR “Engine Pressure
Ra
tio” display mode, the Leak Test ATP is not available, only the Leak Rate Timer feature
is available under these two display modes.
D.
Control mode
The Control mode provides a two-channel pneumatic controller. The Test Set controller is
referred to as the PCM (Pneumatic Control Module). This module provides an absolute
pressure controller for the Static (Ps) channel and a differential pressure controller for the
Pitot (Pt) channel.
The two-channel precision controller is used to control and simulate the Target pressure
and vacuum set point conditions and rates as requested by the user setting Target set
points.