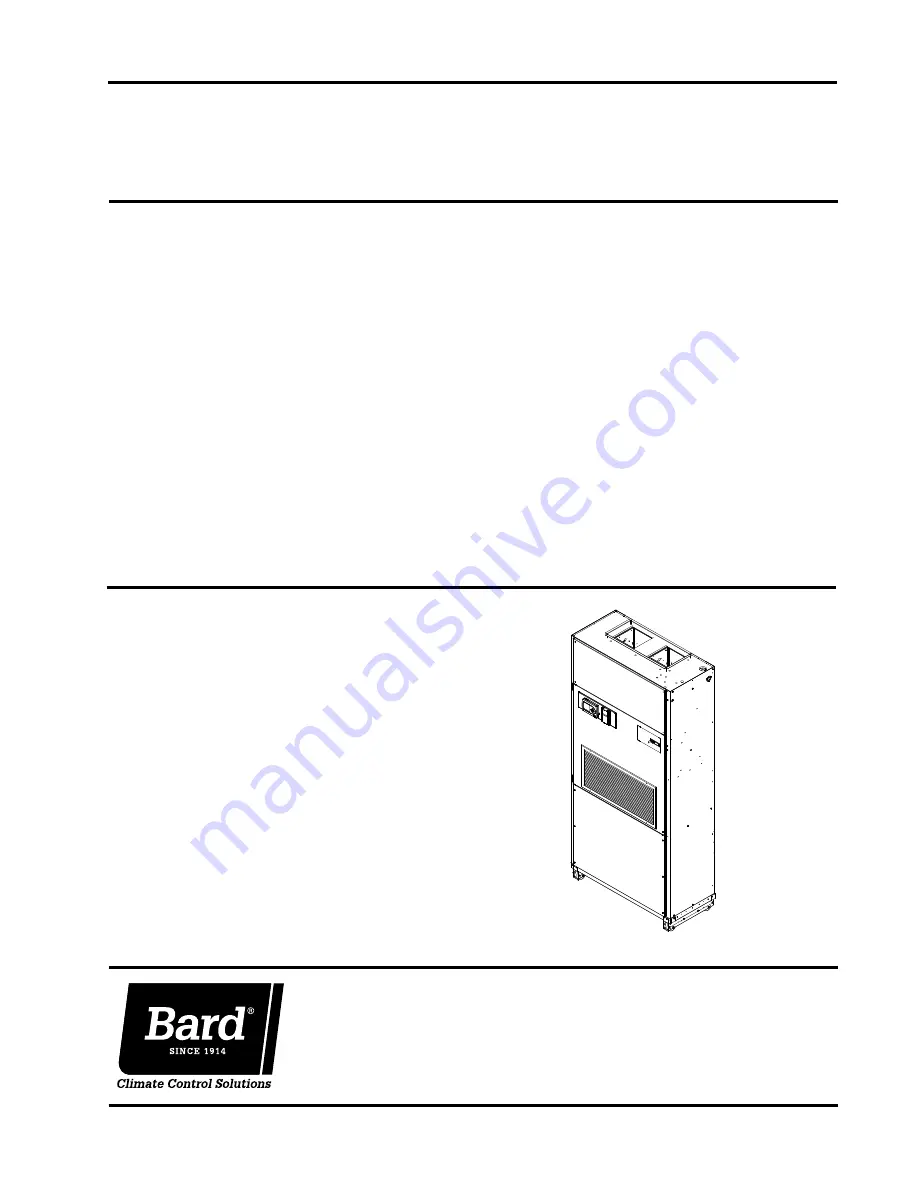
Page
1 of 50
Earth Loop Fluid
Temperatures 25 – 110
Ground Water Temperature 45 – 75
INSTALLATION INSTRUCTIONS
Bard Manufacturing Company, Inc.
Bryan, Ohio 43506
www.bardhvac.com
Manual No.: 2100-577C
Supersedes: 2100-577B
Date: 7-25-17
QW SERIES GEOTHERMAL R-410A
STAGED CAPACITY PACKAGED HEAT PUMP
Models:
QW2S2-A
QW2S2-B
QW2S2-C
QW2S2DA
QW2S2DB
QW2S2DC
QW3S2-A
QW3S2-B
QW3S2-C
QW3S2DA
QW3S2DB
QW3S2DC
QW4S2-A
QW4S2-B
QW4S2-C
QW4S2DA
QW4S2DB
QW4S2DC
QW5S2-A
QW5S2-B
QW5S2-C
QW5S2DA
QW5S2DB
QW5S2DC
MIS-2736
MIS-2736