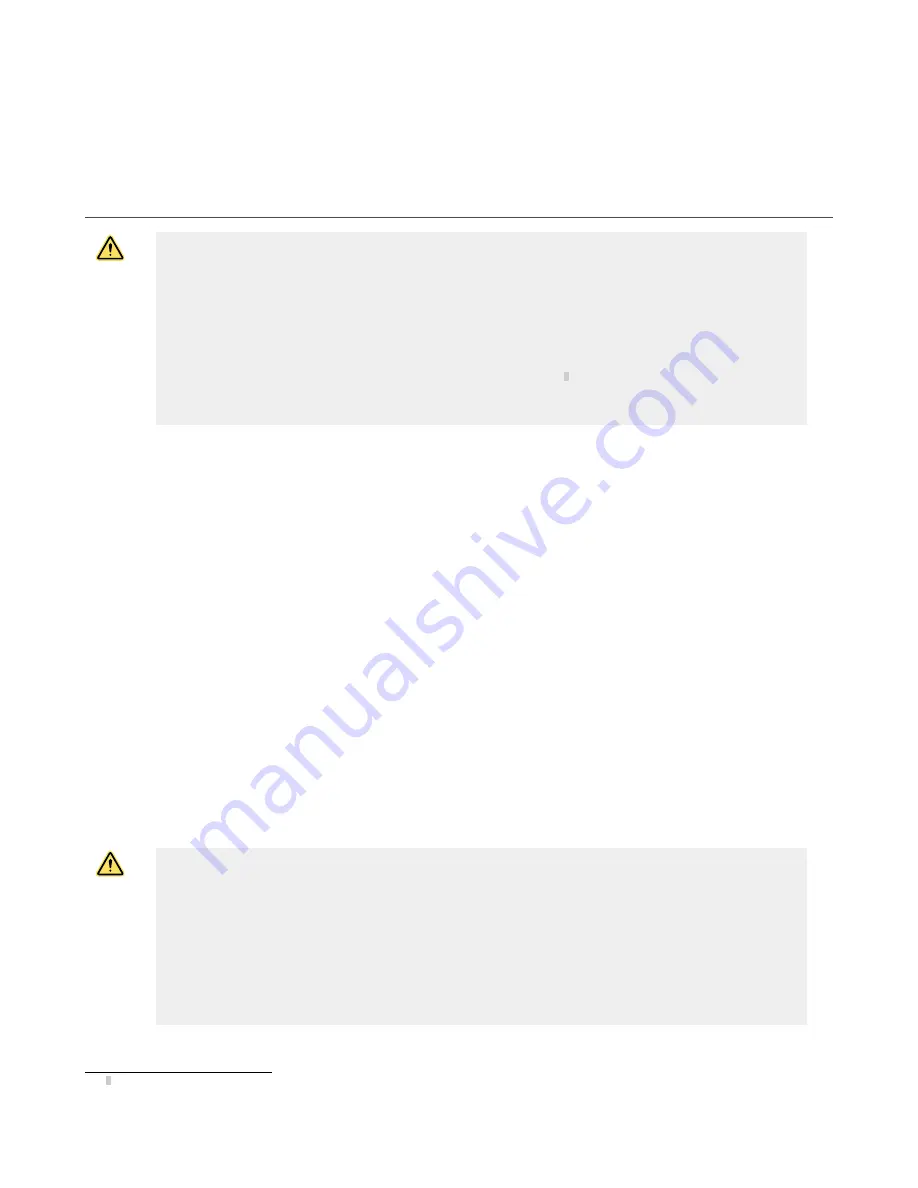
If used, connect the external reset switch to the reset wire of the machine interface cordset and to 24 V DC. See warning
about the physical location of the reset switch in
on p. 37. The reset switch must be a normally open
switch that is held closed for approximately 0.5 to 4 seconds, and then re-opened to accomplish the reset. The switch must
be capable of switching 10 to 30 V DC at 30 mA.
If used, connect the area switch inputs to the configured pins. This must be done to verify each Zone Set.
4.3 Electrical Connections to the Guarded Machine
WARNING:
•
Risk of electric shock
•
Use extreme caution to avoid electrical shock. Serious injury or death could result.
•
Always disconnect power from the safety system (for example, device, module, interfacing, etc.),
guarded machine, and/or the machine being controlled before making any connections or
replacing any component. Lockout/tagout procedures might be required. Refer to OSHA
29CFR1910.147, ANSI Z244-1, or the applicable standard for controlling hazardous energy.
•
Make no more connections to the device or system than are described in this manual. Electrical
installation and wiring must be made by a Qualified Person
8
and must comply with the applicable
electrical standards and wiring codes, such as the NEC (National Electrical Code), NFPA 79, or
IEC 60204-1, and all applicable local standards and codes.
Verify that power has been removed from the SX and the machine/vehicle to which it will connect. Make the electrical
connections described as required by each individual application.
Lockout/tagout procedures may be required (refer to OSHA CFR 1910.147, ANSI Z244-1, or the appropriate standard for
controlling hazardous energy). Follow relevant electrical standards and wiring codes, such as the NEC, NFPA79 or IEC
60204-1.
The connections for supply power, external reset (if used), external device monitoring (EDM) (if used), and Zone Set area
switch inputs (if used) should already be connected. The SX must also have been configured, mounted and passed the initial
on p. 64.
The final connections to be made are:
•
OSSD outputs
•
Warning Auxiliary (if used)
•
FSD/MPCE Interfacing
•
Mute Sensor inputs (if used)
•
Mute Enable input (if used)
•
Mute Lamp output (if used)
•
Override input (if used)
4.3.1 Connecting the OSSD Outputs
Both halves of each pair of output signal switching device (OSSD) outputs must be connected to the machine control so that
the machine’s safety-related control system interrupts the circuit or power to the machine primary control element(s) (MPCE),
resulting in a non-hazardous condition.
Final switching devices (FSDs) typically accomplish this when the OSSDs go to an OFF state. Refer to the output
specifications and the warnings below before making OSSD output connections and interfacing the Scanner to the machine.
WARNING:
•
Interfacing both output signal switching devices (OSSD)
•
Failure to follow these instructions could result in serious injury or death.
•
Unless the same degree of safety is maintained, never wire an intermediate device(s) (PLC, PES,
PC) between the safety module outputs and the master stop control element it switches such that
a failure causes a loss of the safety stop command or the failure allows the safety function to be
suspended, overridden, or defeated.
•
Connect both OSSD outputs to the machine control so that the machine’s safety-related control
system interrupts the circuit to the machine primary control element(s), resulting in a non-
hazardous condition.
8
A person who, by possession of a recognized degree or certificate of professional training, or who, by extensive knowledge, training and
experience, has successfully demonstrated the ability to solve problems relating to the subject matter and work.
SX Safety Laser Scanner
48
www.bannerengineering.com - Tel: + 1 888 373 6767