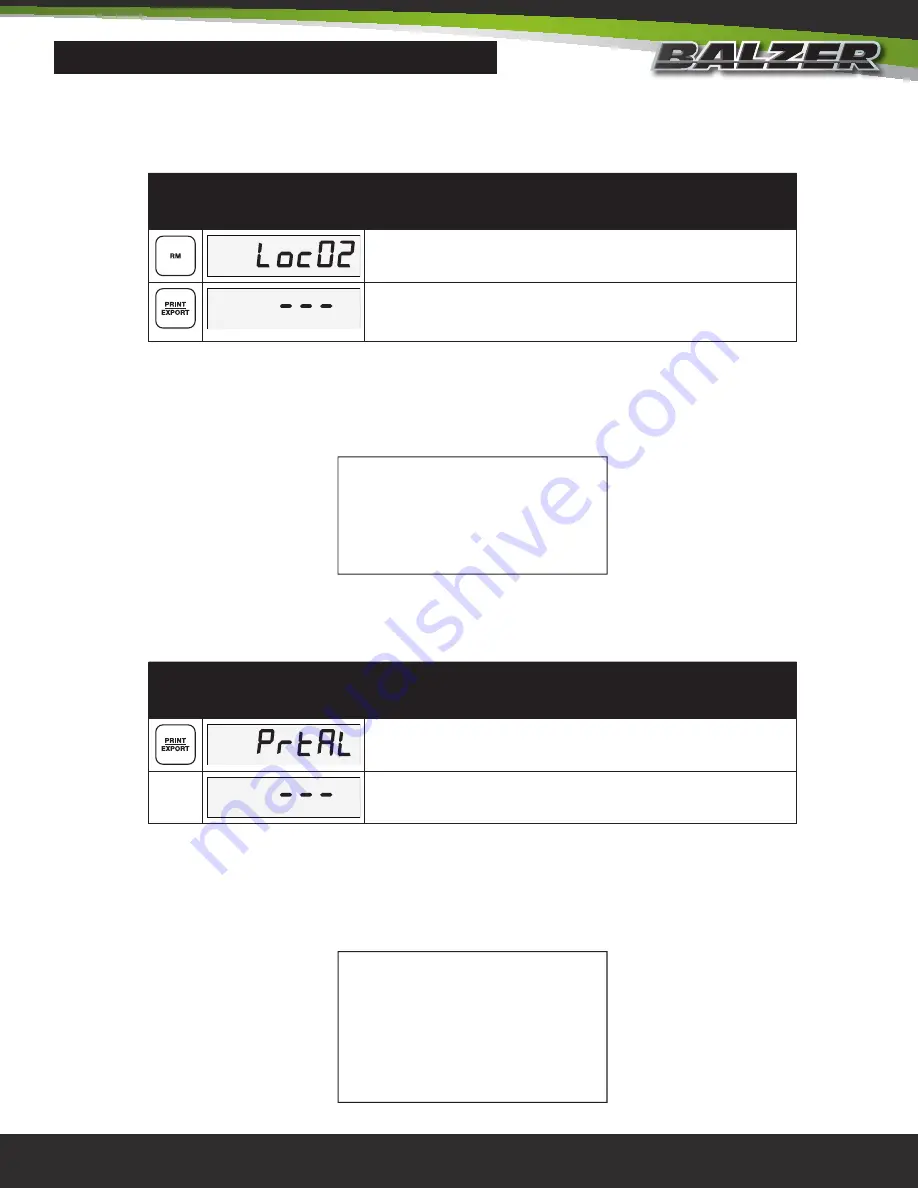
61
Field Floater 6 Grain Cart User Manual
Export a Memory Location to USB
Insert a USB flash drive into the USB port on the host indicator The green light on the USB port should light up
When exporting the data from memory locations to the USB flash drive, the data will write a text ( TXT) file to the flash drive
Each additional export will add to that text file
Figure 81
shows how the data will appear for the export of a single memory
location
Export All Memory Locations to USB
Insert a USB flash drive into the USB port on the host indicator The green light on the USB port should light up
When exporting the data from memory locations to the USB flash drive, the data will write a text ( TXT) file to the flash drive
Each additional export will add to that text file
Figure 82
shows how the data will appear for the export of all memory locations
Using Memory Locations (Continued)
WEIGH SYSTEM PROGRAMMING
Program a Memory Location
Button
Press
Screen
Display
Description
The current memory location will flash on the display Use the
arrow keys to change memory locations to export
The system will write the selected memory location to the USB
flash drive, then return display to current weight of grain in
cart
APR 03, 2015 07:59am
MEM LOC# 2
ID: CORN
TOTAL WEIGHT: 128270 lb
ACCUM COUNT: 05
AVG WEIGHT: 25654 lb
FIGURE 81
APR 03, 2015 08:06am
MEMLOC COUNT AVGWT TOTAL
CORN 05 25654 lb 128270 lb
BEANS 06 25112 lb 150670 lb
TOTAL 11 25358 lb 278940 lb
FIGURE 82
Program a Memory Location
Button
Press
Screen
Display
Description
Press and hold until display shows that it is printing all
memory locations
The system will write all memory locations to the USB flash
drive, then return display to current weight of grain in cart
Summary of Contents for FIELD FLOATER 6
Page 2: ...Serial Number Date of Purchase Purchased From Dealer s Address Dealer s Telephone ...
Page 4: ......
Page 8: ...4 Field Floater 6 Grain Cart User Manual ...
Page 9: ...Field Floater 6 Grain Cart User Manual 5 Safety ...
Page 15: ...Field Floater 6 Grain Cart User Manual 11 Technical Data ...
Page 18: ...14 Field Floater 6 Grain Cart User Manual ...
Page 19: ...Field Floater 6 Grain Cart User Manual 15 Operation ...
Page 39: ...Field Floater 6 Grain Cart User Manual 35 Maintenance ...
Page 52: ...48 Field Floater 6 Grain Cart User Manual ...
Page 53: ...Field Floater 6 Grain Cart User Manual 49 Troubleshooting ...
Page 60: ...56 Field Floater 6 Grain Cart User Manual ...
Page 61: ...Field Floater 6 Grain Cart User Manual 57 Weigh System Programming ...
Page 78: ...74 Field Floater 6 Grain Cart User Manual ...
Page 79: ...Field Floater 6 Grain Cart User Manual 75 Notes ...
Page 80: ...76 Field Floater 6 Grain Cart User Manual Date Notes NOTES ...
Page 81: ...77 Field Floater 6 Grain Cart User Manual Date Notes NOTES ...
Page 82: ...78 Field Floater 6 Grain Cart User Manual Date Notes NOTES ...
Page 83: ......
Page 86: ...Serial Number Date of Purchase Purchased From Dealer s Address Dealer s Telephone ...
Page 88: ......
Page 91: ...Tracks User Manual 3 Technical Data ...
Page 93: ...Tracks User Manual 5 Operation ...
Page 97: ...Tracks User Manual 9 Maintenance ...
Page 103: ...Tracks User Manual 15 Notes ...
Page 104: ...16 Tracks User Manual Date Notes NOTES ...
Page 105: ...17 Tracks User Manual Date Notes NOTES ...
Page 106: ...18 Tracks User Manual Date Notes NOTES ...
Page 107: ......