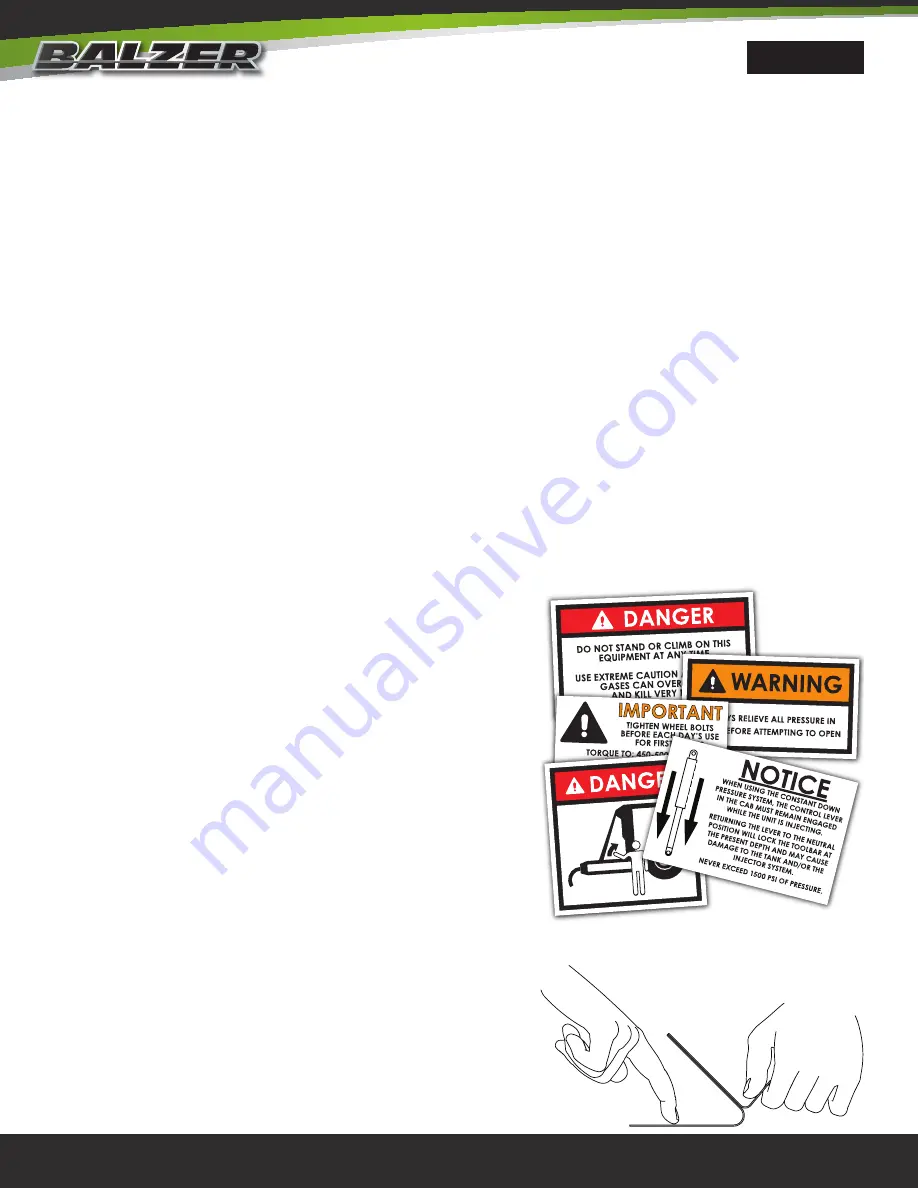
10
Eliminator Vacuum Tank (Tandem) User Manual
Do not wear loose fitting clothing or have long, free-hanging hair when operating the PTO (Power Take Off) or near ANY rotating
equipment .
Never exceed the recommended operating speed (PTO and drive) for the particular equipment in use .
When operating stationary PTO driven equipment, always apply the tractor’s parking brake lock and block the rear wheels front
and back .
To avoid injury, do not clean, adjust, unclog, or service PTO driven equipment when the tractor engine is running .
When finished with the operation of PTO driven equipment, shift the PTO control to neutral, shut off the engine, remove the key,
and wait until the PTO stops before exiting the tractor .
Implement input drivelines, clutches, and freewheels are designed for specific machine types and power requirements .
They must not be replaced by any shaft other than that recommended by the implement manufacturer . Note the Operating
Instructions from both the tractor manufacturer and the implement manufacturer . Ensure the implement driveline is securely
connected at both ends .
Only use a completely guarded drive system (Figure 1) . PTO drive systems with complete guarding include: the tractor master
shield, the implement driveline guard (end cones, telescoping section sleeves, guard chain), and the implement safety shield .
These safety devices must be installed at all times .
If any component of the guarding system has been removed for any reason, it must be repaired or replaced prior to operation
of the machine .
Safety Signs and Decals
Safety signs or decals provide very important information and instructions designed to alert you to dangers and hazards which
can be present during operation of this equipment . These safety signs and
decals MUST be read, understood, and followed to be effective .
Replacement of Safety Signs and Decals
Safety signs and decals must be kept clean and readable . If they become
unreadable for any reason, they must be replaced with an identical
replacement sign or decal . Safety signs and decals must also be replaced
if damaged when repairing this equipment or if not included with the
replacement part .
Application of Safety Decals
Surface preparation is very important for the safety decals to properly adhere .
Grease, oil, and dirt must be removed and the surface must be smooth and
dry . After wiping the surface clean, use an ammonia-free window cleaner to
provide the best surface for decal adherence .
Most decals have a split backing which is meant to be removed from the split
outward . To apply decals, follow these steps:
1 . Position the decal in the proper location and hold firmly over the
largest portion of the backing .
2 . Use one hand to hold the decal in position . With the other hand,
carefully roll the loose end over and peel the backing outward .
When the backing is removed as shown in Figure 3 and with even
and gradual pulling, the decal will roll onto the surface smooth and
wrinkle free,
3 . With the smallest portion of the decal attached, the repeat Step 2 for
the other half of the decal .
When the decal has been attached in place, use a cloth or soft paper towel
to burnish the decal onto the cleaned surface . Work gently from the middle
outwards to avoid creating any wrinkles and to remove any air bubbles .
PTO Operation Safety (Continued)
Figure 2
Do NOT paint over, cover, or rem
ove this decal
37284
Do NOT paint over, cover, or remove this decal 11231
Do NOT paint over, cover, or remove this decal 11233
Do NOT paint over, c
over, or remove this d
ecal
60306
Do NOT p
aint over, c
over, or re
move this d
ecal
60829
Figure 3
SAFETY
Summary of Contents for ELIMINATOR VACUUM TANK Series
Page 2: ...Serial Number Date of Purchase Purchased From Dealer s Address Dealer s Telephone...
Page 4: ......
Page 8: ...4 Eliminator Vacuum Tank Tandem User Manual...
Page 9: ...Eliminator Vacuum Tank Tandem User Manual 5 Safety...
Page 15: ...Eliminator Vacuum Tank Tandem User Manual 11 Technical Data...
Page 19: ...Eliminator Vacuum Tank Tandem User Manual 15 Operation...
Page 31: ...Eliminator Vacuum Tank Tandem User Manual 27 Maintenance...
Page 45: ...Eliminator Vacuum Tank Tandem User Manual 41 Troubleshooting...
Page 52: ...48 Eliminator Vacuum Tank Tandem User Manual...
Page 53: ...Eliminator Vacuum Tank Tandem User Manual 49 Notes...
Page 54: ...50 Eliminator Vacuum Tank Tandem User Manual Date Notes NOTES...
Page 55: ...51 Eliminator Vacuum Tank Tandem User Manual Date Notes NOTES...
Page 56: ...52 Eliminator Vacuum Tank Tandem User Manual Date Notes NOTES...
Page 57: ......