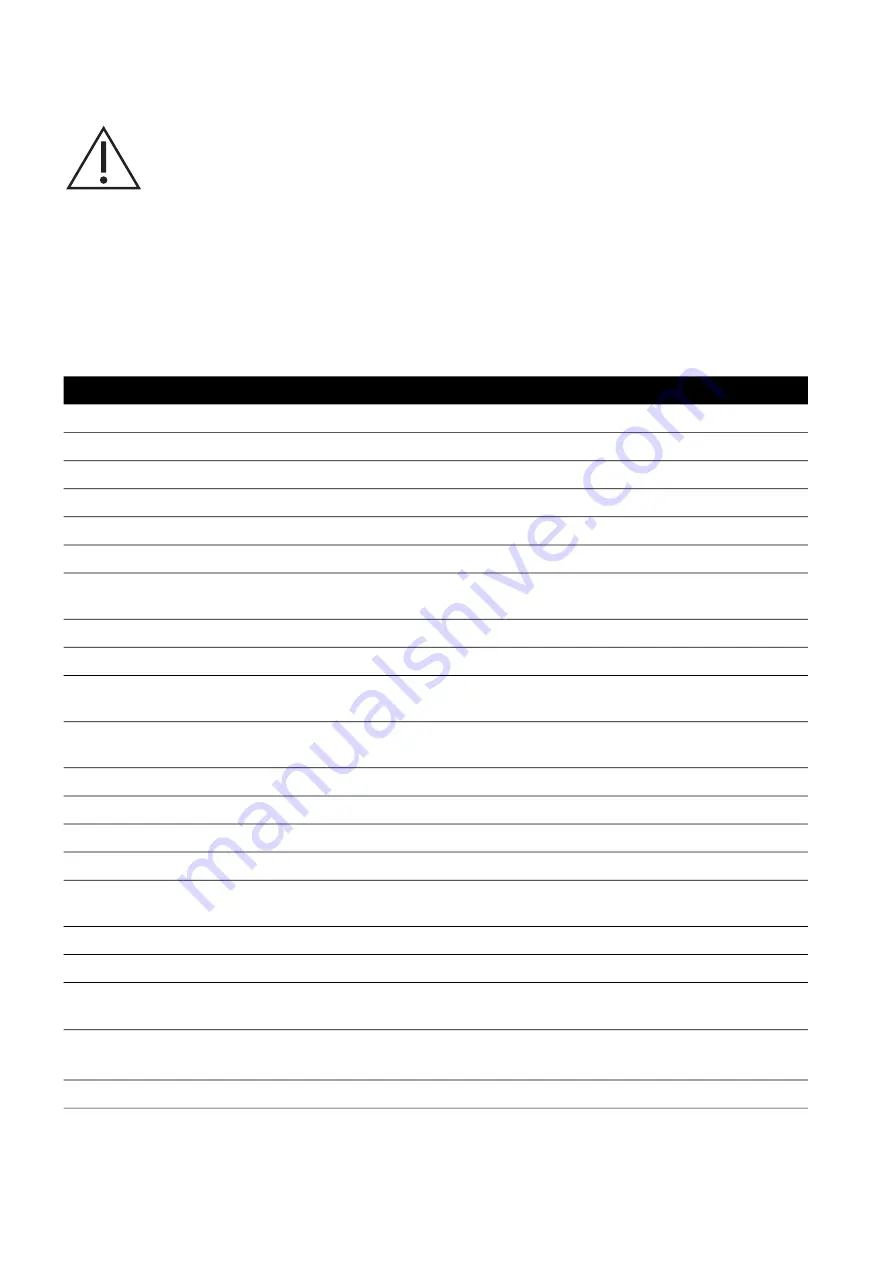
Copyright 2022 Baker Hughes Company.
42 | PTC Temperature Calibrators–English
12.3 Disposal of Calibration Liquid
12.4 Disposal of Calibrator
See “Marks and Symbols on the Equipment” on page
ii for details of the Druck WEEE take-back
scheme.
13. Specification
13.1 Shared Specification
CAUTION
Dispose of the calibration liquid in accordance with the Technical
Safety Data Sheet.
Specification
Dry
PTC and Liquid
PTC Models
Display:
Type
17.8
cm (7″) Color Touch Screen
Resolution
0.1 / 0.01 / 0.001
°C / °F / K
Display units.
°C / °F / K
Display for sensor failure.
On-screen message.
Sensor failure behavior.
The control is switched off.
Excess temperature behavior.
Thermal fuses interrupt the power supply on excessive temperature
inside the housing.
Environmental:
Operating temperature range.
0°C to 50
°C (32°F to 122
°F)
Transportation and storage
temperature.
-
10
°C to 60
°C (14
°F to 140
°F)
Relative humidity.
<
80
% to 31
°C (87.8
°F), reducing linearly to 50
% at 40
°C (104
°F)
(none condensing)
Operating conditions:
-
Location
Indoor use only.
-
Altitude
Up to 2000
m (6561
ft)
-
Operating position
Standing upright / vertically.
EMC
Tested in accordance with EN
61326
-
1, class
A (Industrial
environments)
Electrical Characteristics:
PC interfaces
Ethernet, 3 × USB
Mains cable
H05VV-F 3 G 0.75 mm
2
with angled protective contact plug and cold
equipment plug. Length ~
2
m (6.6
ft)
Safety
Over-voltage (Installation) Category
II
Pollution Degree
2 according to IEC
61010-1
Protective earth
Protective earth conductor (PE) must be available.