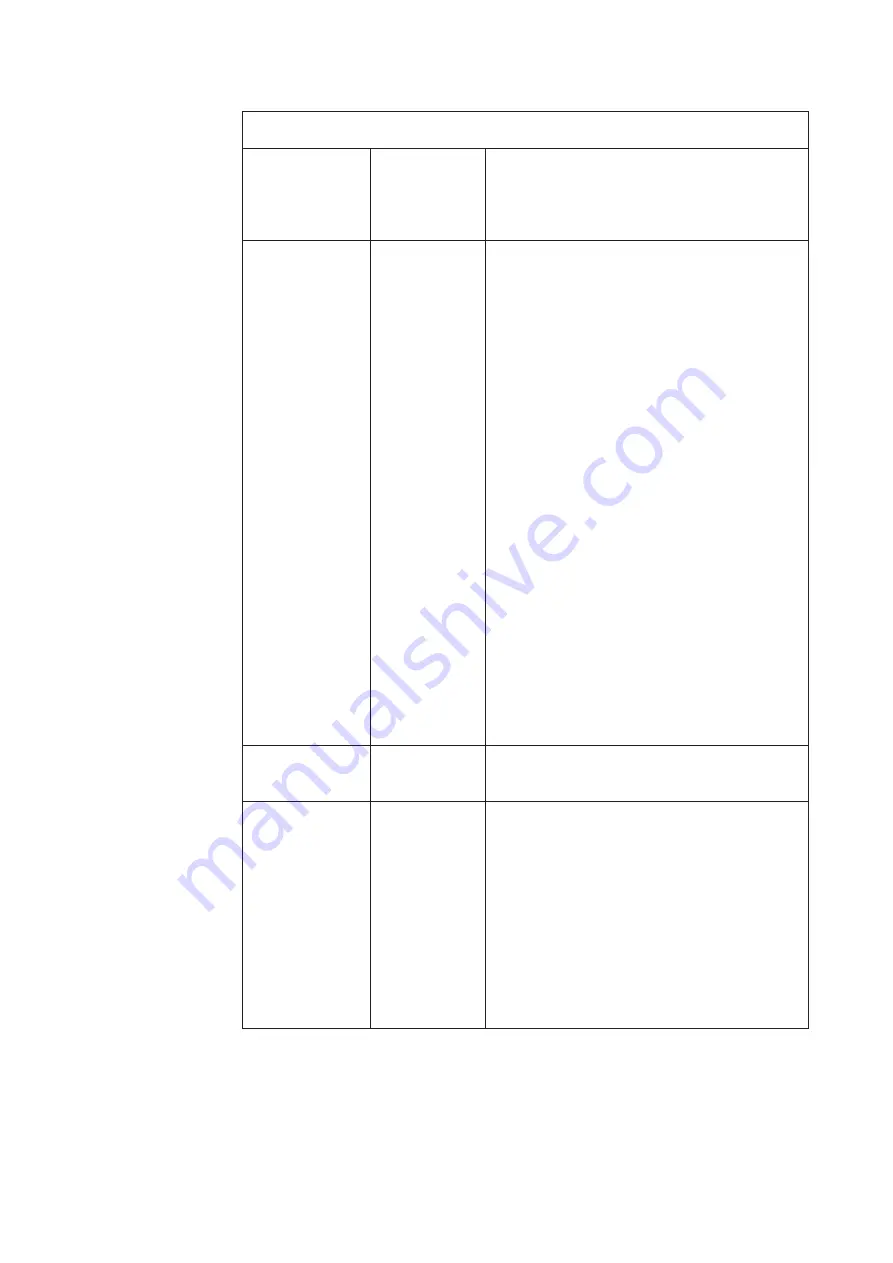
67
Transducer Block (FF parameters)
Parameter
Write access
with operating
mode
(MODE_BLK)
Description
Block Error
(BLOCK_ERR)
Read only
The active block errors appear on the display.
Display:
OUT OF SERVICE
The block is in the “out of service” operating mode.
The following block errors are only shown in the
Sensor Transducer Blocks:
INPUT FAILURE
Error at one or the two sensor inputs
MAINTENANCE NEEDED
The device must be checked since an active device
error is pending. The detailed cause of the error
can be called up in the “Advanced Diag.nostic”
Transducer Block by means of the
“ACTUAL_STATUS_CATEGORY” and
“ACTUAL_STATUS_NUMBER” parameters.
LOST STATIC DATA / LOST_NV_DATA
The memory is inconsistent.
POWER-UP: Status message during the startup
procedure.
SIMULATE ACTIVE: The DIP switch for the
simulation is active.
BLOCK CONFIGURATION ERROR: The block
was configured incor.rectly.
0x000: No active block error present.
An exact error description as well as information on
rectifying faults can be found in Section 7-2.
Update Event
(UPDATE_EVT)
AUTO - OOS
Indicates whether static block data have been altered,
including date and time.
Block Alarm
(BLOCK_ALM)
AUTO - OOS
The current block status appears on the display with
information on pending configuration, hardware or
system errors, including information on the alarm
period (date, time) when the error occurred.
Notes:
In addition, the active block alarm can be
acknowledged in this param.eter group.
The device does not use this parameter to display
a process alarm since this is generated in the
BLOCK_ALM parameter of the Analog Input
function block.