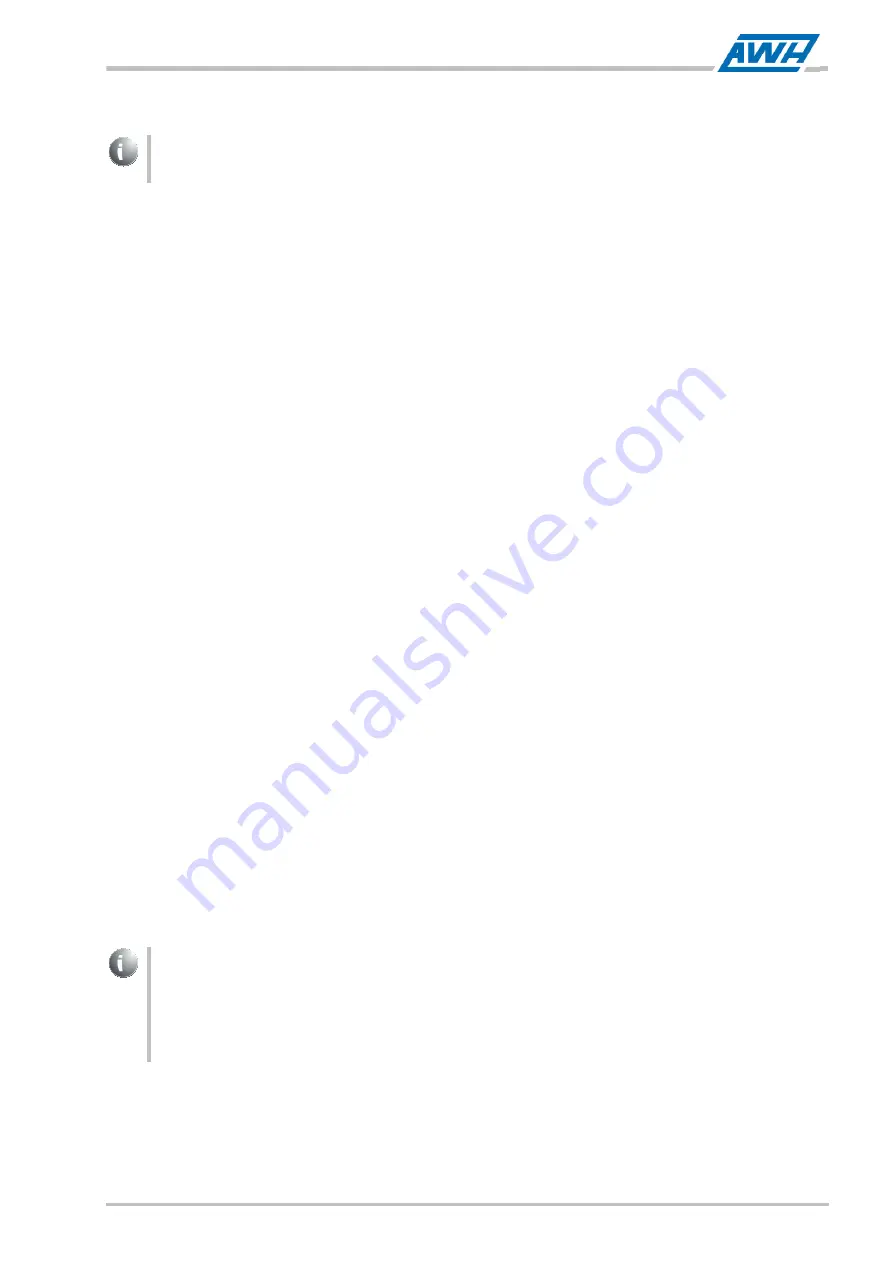
Jet Cleaner TANKO-JM
3 Construction and Function
Translation of the original Operating / Installation Instructions 2016/12
17/90
3.2.1
Function of the JM100
The item numbers shown in brackets refer to the
Figure 7.5-1: Internal construction
The cleaning fluid enters at the connection cover (01) and flows through the holes of the flow-in disk (09)
into the inside of the device in order to cause turbulent movement underneath the flow-in disk (09) in
the liquid around the rotor shaft (10).
The liquid flows downwards on the outside of the rotor shaft (10) and hits the rotor star wheel (11).
The rotor star wheel (11) sets the rotor shaft (10) in rotation.
The liquid then flows through the side bores in the rotor shaft (10) into the axle for nozzle carrier (13)
and is distributed through the bores in the axle for nozzle carriers (13) in the bevel gear wheels with
nozzle carrier (14) with the nozzles (06). From there, the fluid passes through the nozzle openings and
back out again.
Any leakages from the cleaning device are used for the device’s self
-cleaning.
The rotation of the rotor shaft (10) causes an orbital rotation of the bevel gear wheels with nozzle
carrier (14) around the rotor shaft (10). A simultaneous rotational movement of the bevel gears with
nozzle carrier (14) around the axle for nozzle carriers (13) is triggered by the gearing of the bevel
gears (12; 14).
The different number of teeth in the bevel gear wheels (12; 14) causes an offset in the nozzle position
with each revolution and thus the initiation of a 360° spray angle.
JM100 cleaning times:
The speed of the cleaning head varies depending on the volume flow rate which is determined in
particular by the number of nozzles, the size of the bores in the nozzles and by the pressure of the
cleaning agent.
–
If the entry pressure is 3 - 20 bar (44 - 290 psi), the speed of the cleaning head is 5 - 20 rpm.
Fluctuations of 10
–
15% are to be expected due to the design.
–
A complete cleaning cycle is completed after 45 revolutions. At a speed of 5 rpm, 9 minutes are
required for a complete cleaning cycle.
–
In order to determine the cycle time, divide the number 45 by the number of revolutions of the
cleaning head per minute.
The speed of the cleaning head can be modified in the medium or bypass plug in the inflow disk to
match the various operating situations (e.g. pressure, installation position and temperature of the
cleaning medium).
When the medium pressure on the device is the same, the exchange of the medium plug
(bypass) with the smaller bore leads to lower consumption. The flow speed via the bores/plugs
of the inflow disk increases at the same time. This causes the actuator to become
stronger/faster up to a certain ratio of pressure and volume flow rate and results in an increase
in the speed of the cleaning head.
After installation of the device, you must check the speed of the cleaning head (see
section 6.2.
). The speed must be adjusted if it is outside the recommended range. In
the event of spontaneous pressure increase, a run-in period of 2-4 minutes may be required before the
device reaches the speed.